2025 Author: Howard Calhoun | [email protected]. Last modified: 2025-01-24 13:10
Technologies for the processing of building materials for the most part are developing in the direction of increasing power and productivity. These are important workflow indicators for the maintenance of solid materials, but for fragile products, other characteristics come to the fore. Virtually any glass processing must provide an accurate and accurate impact on the material so as not to disturb the structure of the future work surface.
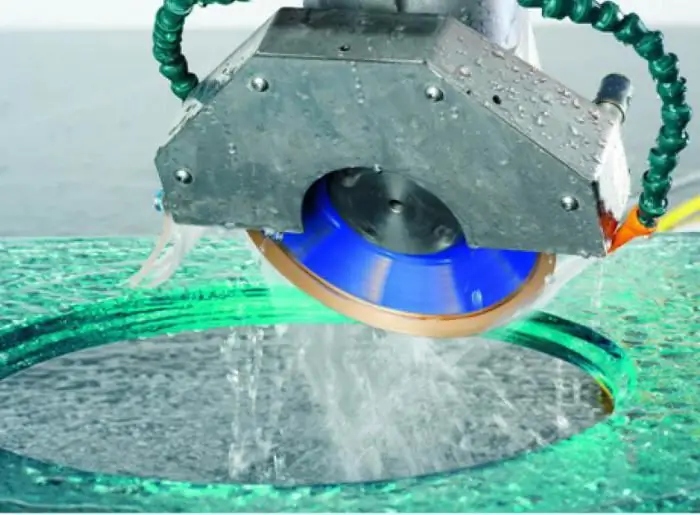
Glass cutting techniques
In industry and in production, an automated method of such processing is used. Machine tools can be different - for example, equipment with mechanical cutting heads is traditionally used. A rather promising direction is waterjet cutting of glass, which is distinguished by high accuracy and the absence of negative side effects. The operator of such an installation can accurately and very finely perform processing, regardless of the complexity of the cut line. In this case, the direct working element for cutting is a water jet supplemented with sand abrasive particles.
The waterjet method was preceded by sandblasting. In essence, the principle of operation is the same, but air is used instead of a liquid medium. WhatAs for the quality of the result, glass cutting with a sandblaster is inferior to waterjet. But on the other hand, this method turns out to be more economical due to the lack of the need to supply a water resource.
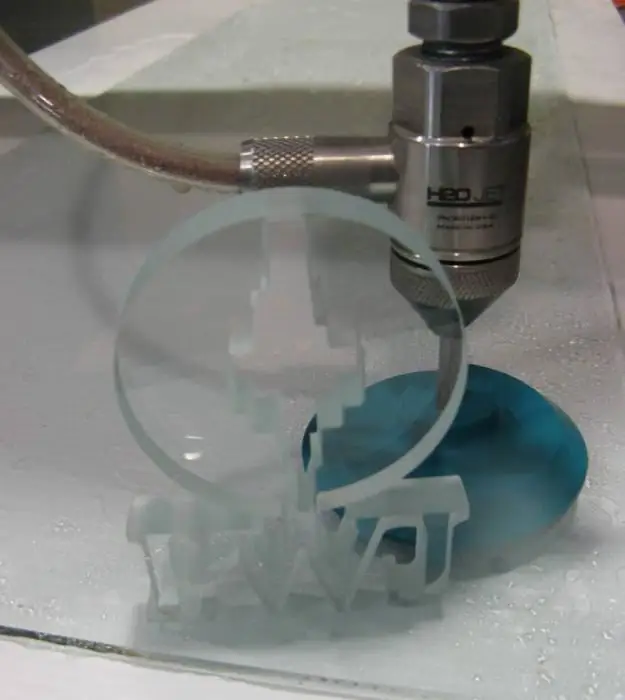
Mattifying
The purpose of this treatment is to make the glass surface matte. This task is achieved by mechanical action on the product by the mentioned sandblasting. Of course, in this case, completely different indicators of power and power supply of the abrasive are used, but the principle of operation of the equipment remains the same. A jet of compressed air, diluted with sand elements, is delivered to the surface of the target object. It is important to note that the glass sandblasting machine is able to perform not only a complete matting, but also to form decorative patterns and patterns on the surface. That is, the device can also allow decoration - the main thing is to set a special operating mode for this and adjust the abrasive grain parameters.
Bevelling
The edge of the glass sheet is often processed as well. The beveling technique also provides a very precise and accurate processing, which involves several stages. First of all, rough grinding is performed with cleaning of pronounced surface defects. This is followed by a clean sanding and two final stages of polishing. As a rule, glass edge processing is carried out in order to round corners. But depending on the capabilities of the beveling machine, the user may receive special angle parameters.according to individual requirements. Equipment for such purposes is mainly supplied from China and can process almost all standard sizes of sheet glass.
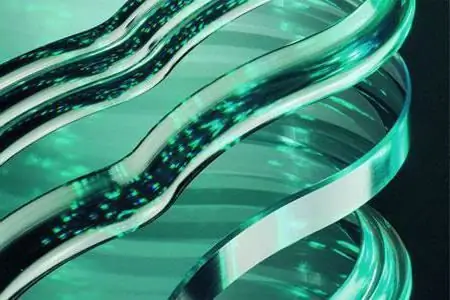
Glass tempering
Tempering process is aimed at increasing the strength characteristics of glass. A furnace is used as the basic equipment, which operates at temperatures of about 6000 °C. When heated, the conveyor rollers move the workpieces, protecting individual edges from overheating. The next stage of hardening involves a cooling effect. Temperature treatment of glass forms mechanical compression forces on its surface, which contributes to an increase in the strength of the material by several times. According to technologists, hardening also endows products with increased heat resistance and tolerance to strong vibration loads. It is worth noting that glass should be directly machined before the tempering process, as it will no longer be possible to do this after it.
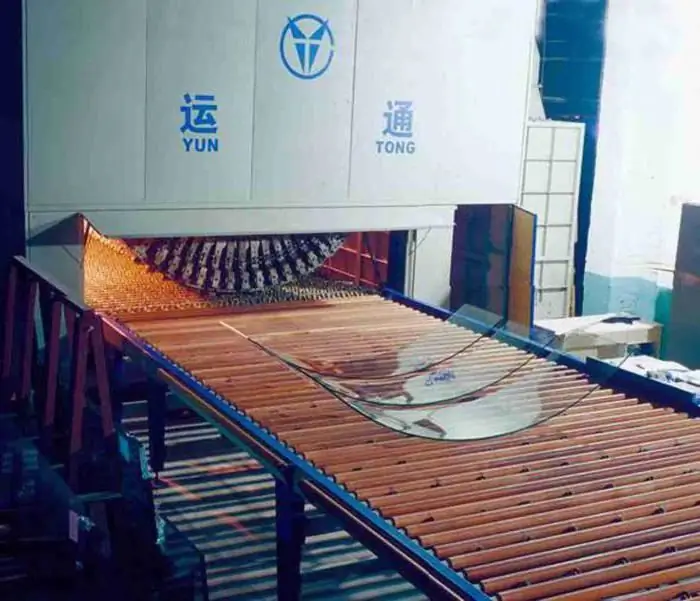
Bending
Also a popular processing technique, during which the master changes the shape of the product in accordance with certain requirements. A typical operation of this kind, for example, is the creation of bends. Technologically, the process involves the implementation of the procedure under high-temperature exposure, which softens the structure of the material. For subsequent molding, a special matrix is used, in which the glass is processed by bending. Depending on thethe thickness of the product and the configuration of the bend, the correction process can take from 2 to 20 hours. At the end of the operation, as in hardening, cooling is performed by air flows. By the way, equipment for hardening and bending is often combined on the same production line. Together with heat treatment, the user can perform the forming of flat and curved glass products.
Chemical etching
The purpose of this technique is also to provide a haze to the glass surface. Only, unlike the previous method, not a sandblasting tool is used, but a chemical effect. On special molds, contact between glass and acid vapors is ensured, which as a result form insoluble s alts. It must be said that the types of glass processing by etching are quite diverse precisely because of the use of a wide group of chemical reagents. In this case, not only directly active elements are noted, but also substances that cover areas that are not intended for processing. This is especially true for artistic processing operations. Another important difference between chemical treatment and sandblasting is the passage of hardening after contact with acidic environments.
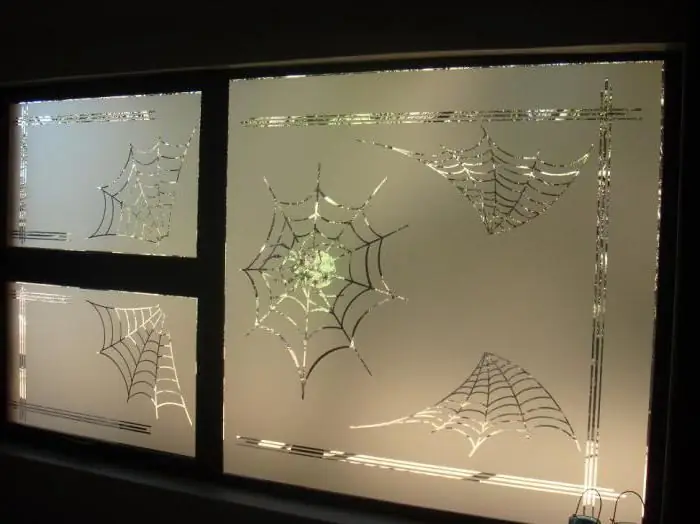
UV bonding
The bonding and soldering technology comes from the need to solve a common problem in the electronics industry. The fact is that the combination of metal and glass into a single part did not allow for sufficient gas-tight resistance before. The solution to the problem was the emergence of new methods that make it possible to implement better soldering. One of the most popular methods is gluing with special compounds. In addition to applying an adhesive, glass treatment with ultraviolet radiation is also expected. In the process of polymerization, the connection acquires sufficient strength and a wide range of other protective properties, not to mention the tightness of the bond.
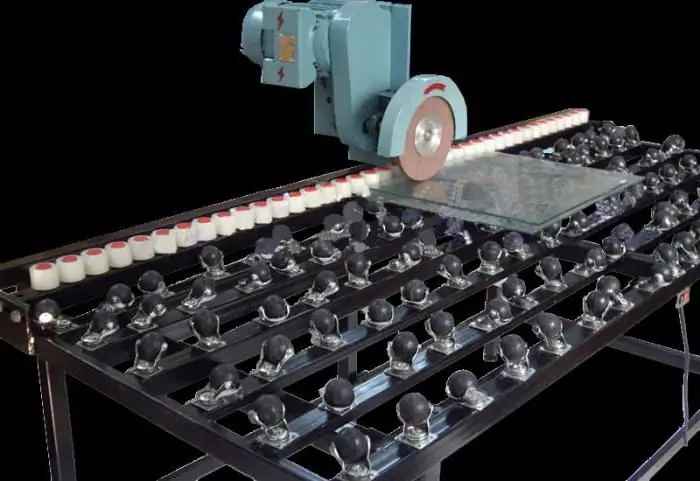
Conclusion
Methods of processing glass products mainly differ in the nature of the impact. The traditional and most common way to change the characteristics of such materials is mechanics. Cutting heads on machine tools and sandblasters act mechanically, allowing you to get both a high-quality cut and an artistic pattern on the surface. Glass processing equipment is also used, which provides for thermal exposure. As a result, blanks acquire higher technical and operational qualities. This applies to hardening technologies as well as chemical pickling. There are also new approaches to the processing of brittle material. Among them, waterjet cutting and gluing under the influence of ultraviolet rays can be distinguished.
Recommended:
How to make glass? Glass production technology. glass products
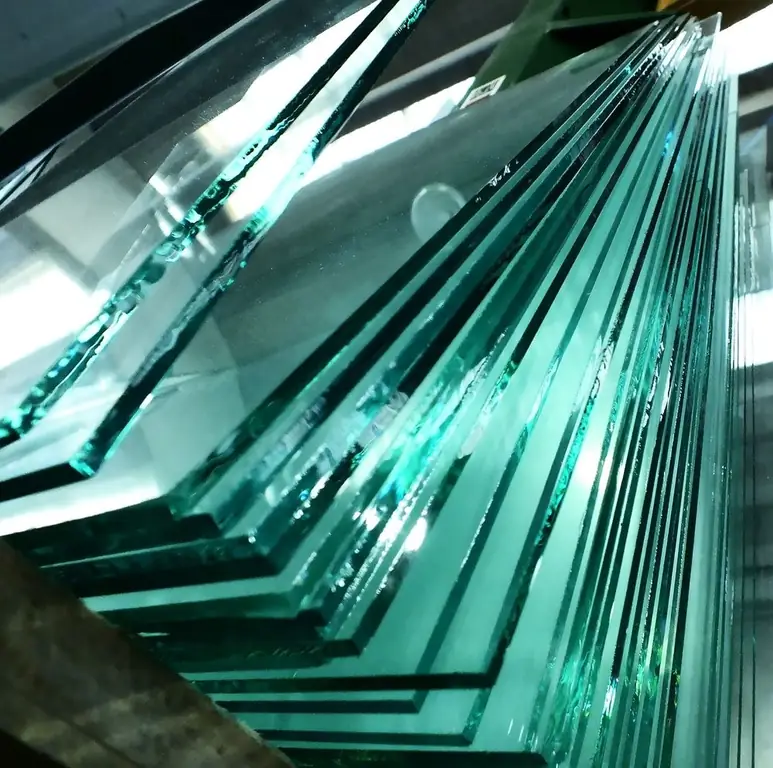
Glass is familiar to everyone. But the process of making it is extremely exciting. Each stage is important and affects the quality of the final product. The basis is sand, soda, lime. The process is almost entirely automated. Surprisingly, glass can even be made at home
Glass sandblasting: glass processing description, equipment, application, photo
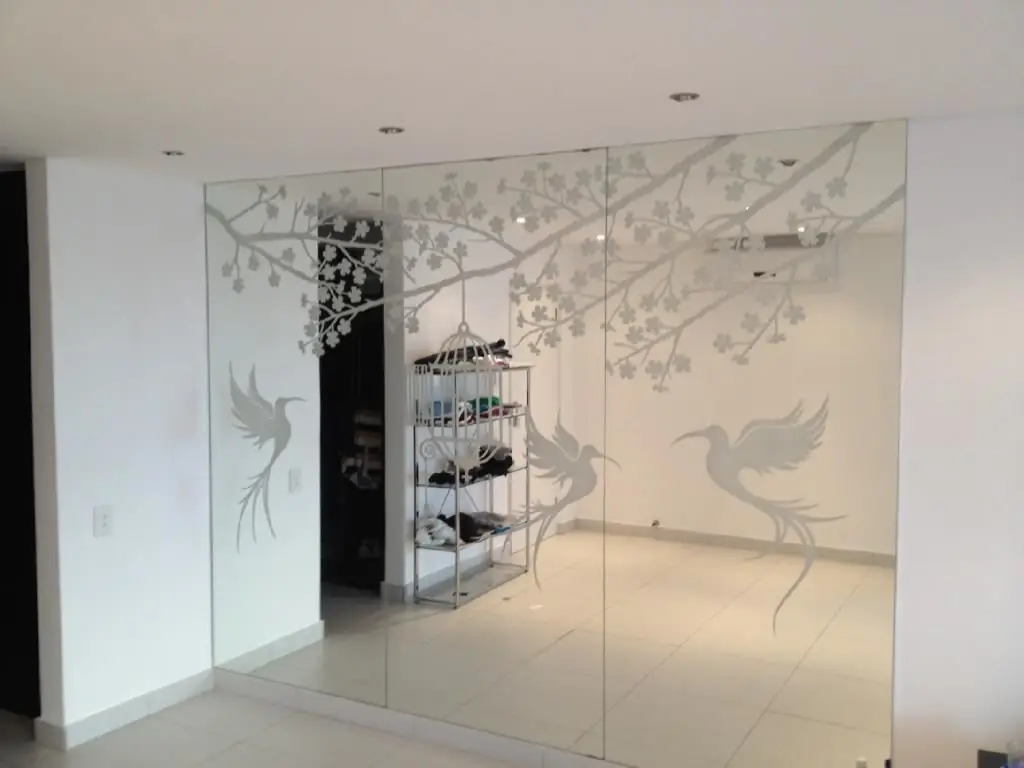
Among the numerous variations of interior decoration, sandblasting of a glass or mirror surface occupies a special place. This technology involves exposing the canvas to sand or other abrasive with a jet of compressed air released under high pressure. As a result, the surface changes and becomes matte, rough, velvety or painted with patterns. In the article we will consider what is sandblasting glass
Meat: processing. Equipment for meat and poultry processing. Production, storage and processing of meat
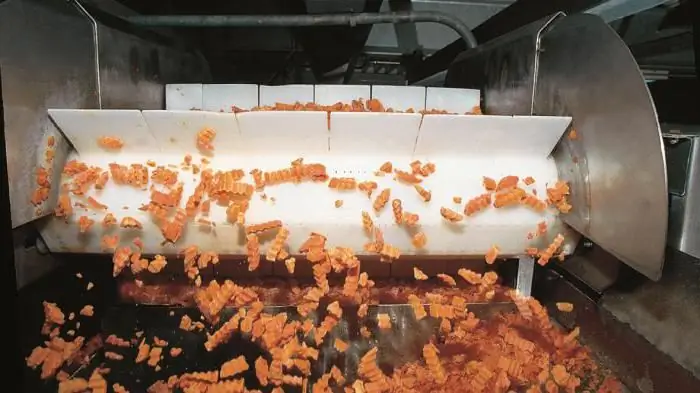
Information of state statistics show that the volume of meat, milk and poultry consumed by the population has significantly decreased in recent years. This is caused not only by the pricing policy of manufacturers, but also by the banal shortage of these products, the required volumes of which simply do not have time to produce. But meat, the processing of which is an extremely profitable business, is very important for human he alth
What is tempered glass: features of production, processing and applications
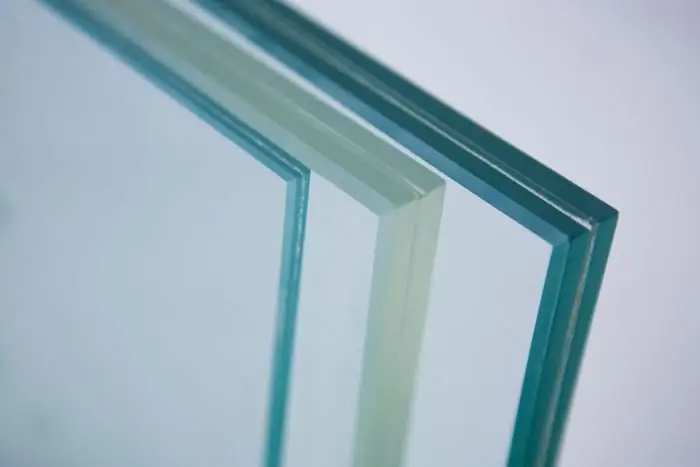
How is tempered glass different from regular glass? A description of the production process and the specifics of processing will help to find the answer to this question. Methods for determining tempered glass and possible options for cutting it without the use of special equipment
Titanium processing: initial properties of the material, difficulties and types of processing, principle of operation, techniques and recommendations of specialists

Today, people are processing a wide variety of materials. Titanium processing stands out among the most problematic types of work. The metal has excellent qualities, but because of them, most of the problems arise