2025 Author: Howard Calhoun | [email protected]. Last modified: 2025-01-24 13:10
Compressor plant is equipment that is used to produce compressed gases. Stations of this type are used in enterprises for the operation of pneumatic tools.
There are many models with cooling systems. It is also worth noting that the modifications differ in performance. Some stations are designed to work with nitrogen. Compressors are used in different types.
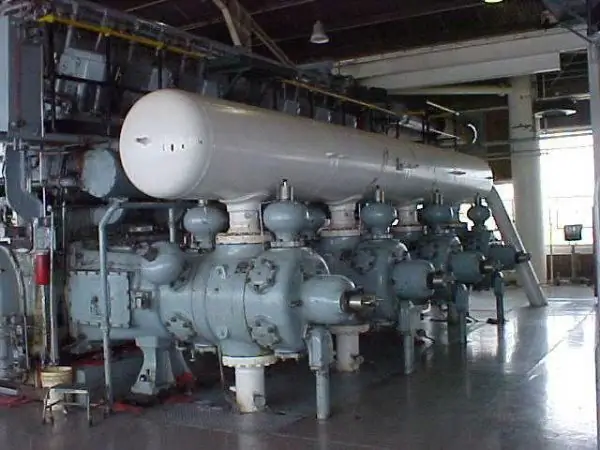
Main advantages of models
Among the advantages of the models, it is worth noting low energy consumption. It is also important to mention the environmental friendliness of the devices. Stations are capable to work with various pneumatic tools. Many models are equipped with gas analysis systems.
Device flaws
Among the shortcomings of the devices, it is necessary to mention the large dimensions. Models are not allowed to be used at sub-zero temperatures. It is also worth noting that the stations are constantly in need of maintenance. This requires a specialized compressor unit operator. Jobs may not be found in all cities.
Operating instructions
Installation of the compressor unit is carried out in compliance withfire safety rules. Separators are refueled to use the station. The tank in this case is filled with water. Before turning on the model, refrigerators are checked, the waste oil compartment is opened. The pipe is connected through the pump. The collector at the station needs to be cleaned, the intake tank checked. Instructions for compressor units for models may differ.
Modification types
Separate gas and air compressor units. Their installation rules are very different. By design, you can find stationary and mobile modifications. If we consider compressors, then there are piston, rotary and screw mechanisms. They differ in power and ultimate pressure.
Gas models
Gas modifications are made with several compressors. Their power rating starts from 4 kW. Models are able to work on circulation pumps. Operation of compressor units is carried out only at positive temperature.
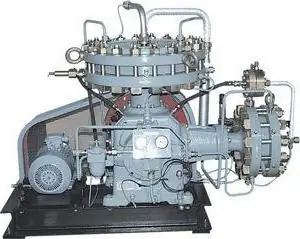
Water tanks are used in different sizes. Fans are used to cool the units. Controllers for devices are suitable for electronic type. If we talk about the benefits, it is important to note the low oil consumption. The models also have a temperature control unit. The maximum pressure at the stations starts from 3 bar. The models have good performance. If we talk about the shortcomings, then experts point to a low operating temperature. Collectors are only suitable for screw type. Models need maintenancetherefore, the compressor unit operator must ensure their operation.
Air Devices
Air units are most often used to operate pneumatic equipment. Models have very high suction power. It is also worth noting that the stations are produced with cooling systems of different classes. They don't have water tanks. Collectors are installed chamber type. Refrigerators are made only with sprinklers. Many models are very large. However, there are also mobile devices.
If we talk about the shortcomings, it is worth mentioning the release of a large amount of condensate. Models have problems with channel overheating. It is also worth noting that gas installations need frequent maintenance. Compressors are most often used of a circulating type, and the power indicator starts from 4 bar.
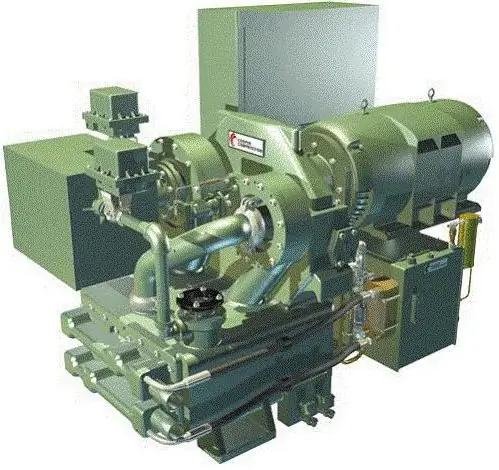
Stationary models
Stationary modifications are able to work with large cooling tanks. Separators are used with capacitive containers. Direct compressors are allowed to use different types. The average power of the installations starts from 5 kW, and the maximum pressure is 2 bar. Some devices are made with several pumps. The retraction force in this case depends on the rotor. Irrigation systems are channel-type.
Reservoirs are most often installed at the top of structures. Refrigerators are used on one or more motors. Waste oil in this case is immediately drained throughnozzles. If we consider the advantages of modifications, it is worth noting that they stand out for their good performance and are suitable for large enterprises for pumping liquids.
Mobile devices
Mobile devices are in high demand these days. Modern devices are able to work at high temperatures. Cooling systems are most often used in the third class. Pumps for devices are suitable only for cyclone type. In this case, compressors are selected with a small capacity. Fans come in different sizes.
Separators are installed in many stations. These elements are able to withstand a pressure of not more than 2 bar. In this case, the power indicator starts from 4 kW, but in this case a lot depends on the compressor. Mobile devices are great for working with liquefied gas. However, it is worth remembering the disadvantages of models of this type. First of all, we are talking about low productivity. In this case, it is difficult to solve the problem with processed oil. You have to clean up the condensate yourself.
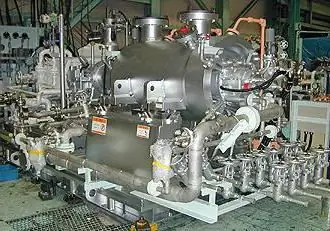
Piston Models
Piston installations (compressor) are most often made of a stationary type. They have a low power rating, but they have very simple controls. The collectors in this case are of low conductivity. For condensate, as a rule, separate tanks are installed. You can also find tanks from liquefied gases. The models use refrigerators with built-in irrigation systems. Pumps in stationscirculating type are used. A large capacity is used to store hydrocarbon gas.
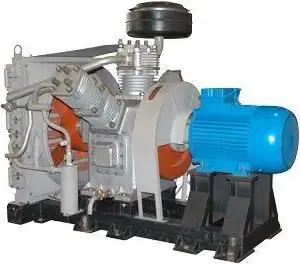
Rotational devices
Rotary installations (compressor) have a lot of advantages. They are able to work at high temperatures. Collectors are used in different capacities. Compressors are quite often used centrifugal type. There are models for two and three pumps. Purge mechanisms are most often installed at the bottom of the structure. Fans of different diameters are used to cool rotary units. The hoods in this case are located at the top of the stations.
Reservoirs are installed for used oil. What are the disadvantages of rotary devices? First of all, it is important to mention the large dimensions. There are no mobile devices among rotational models. Refrigerators are allowed to install low power. Many stations have problems with high humidity. Dry gas has to be stored in separate containers.
Screw installations
Screw stations are great for compressor equipment of different capacities. The peculiarity of the devices lies in the presence of collectors. In this case, the guides are screwed. Devices vary in performance and power.
Many models stand out with their low levels of used oil. Refrigerators are usually installed with irrigation systems. Blocks in this case are fixed at the bottom of the stations. Pumps are found both centrifugal and cyclic type. Strengthsuction depends on the size of the compressor.

Single-stage models
Single-stage units (compressor) are not capable of boasting high performance, and the power parameter for models is about 2 kW. Gas tanks are installed with refrigerators. Separate containers are provided for condensate. Pumps are used only cyclic type. The maximum pressure at the stations is approximately 5 bar. Cooling systems are used second and third class. Quite often, fans are fixed on the installations. Collectors are used with switches. A modulator is required to control the station.
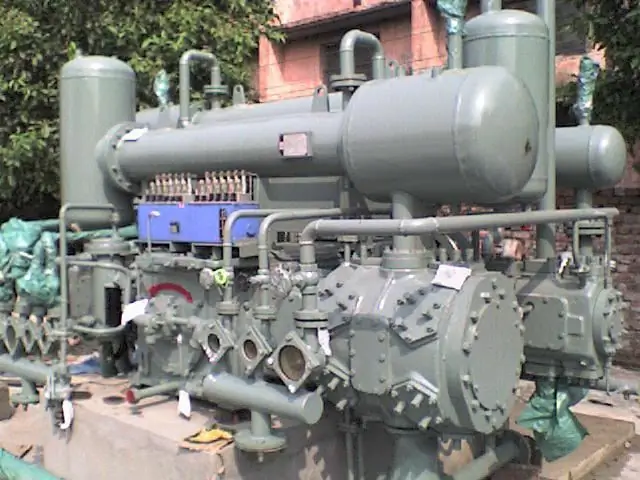
Features of two-stage devices
Two-stage units (compressor) are capable of operating in different modes. They use powerful pumps. Compressors are used for 3 and 4 kW. The maximum pressure at the stations starts from 6 kW. Collectors are installed behind the pumps. Many models are produced with several compressed gas tanks. Not large containers are used for condensate, and the pipes are connected through the central chamber. The pumps are available with and without a separator. The pressure force in the devices starts from 10 microns.
Recommended:
The organizational structure of an organization is Definition, description, characteristics, advantages and disadvantages
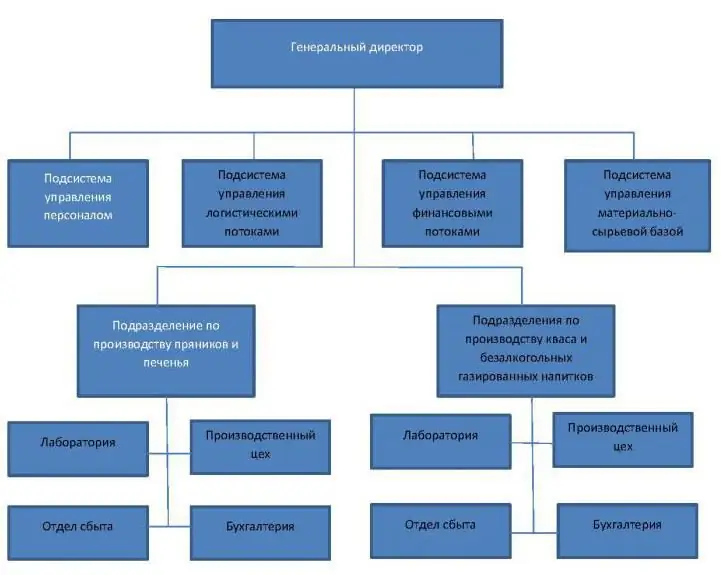
The article reveals the concept of the organizational structure of an enterprise: what it is, how and in what forms it is used in modern enterprises. The attached diagrams will help to visually illustrate the use of different types of organizational structures
On-call credit is Definition, conditions for obtaining, advantages and disadvantages
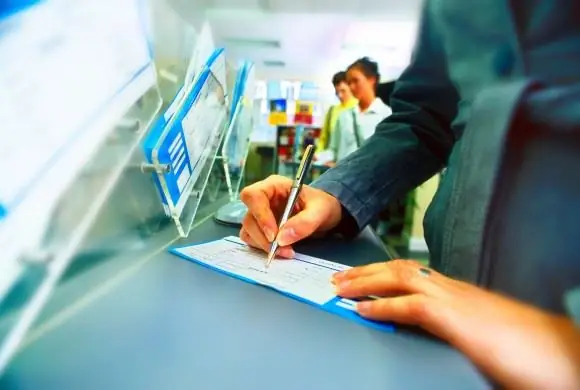
On-call loan is a type of loan in which the borrower gets the right to use funds from a specially opened account at his own discretion. The amount is limited. On-call credit is the provision of a loan by a bank with the right to demand a refund at any time
What is a compressor station? Types of compressor stations. Operation of compressor stations
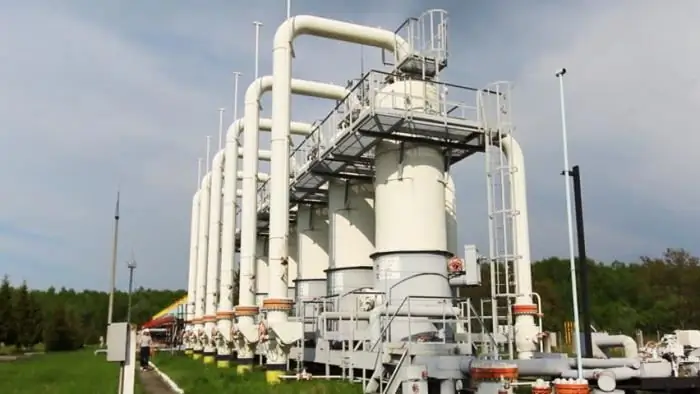
The article is devoted to compressor stations. In particular, the types of such equipment, conditions of use and features of operation are considered
Collective investments: concept, types and forms, advantages and disadvantages
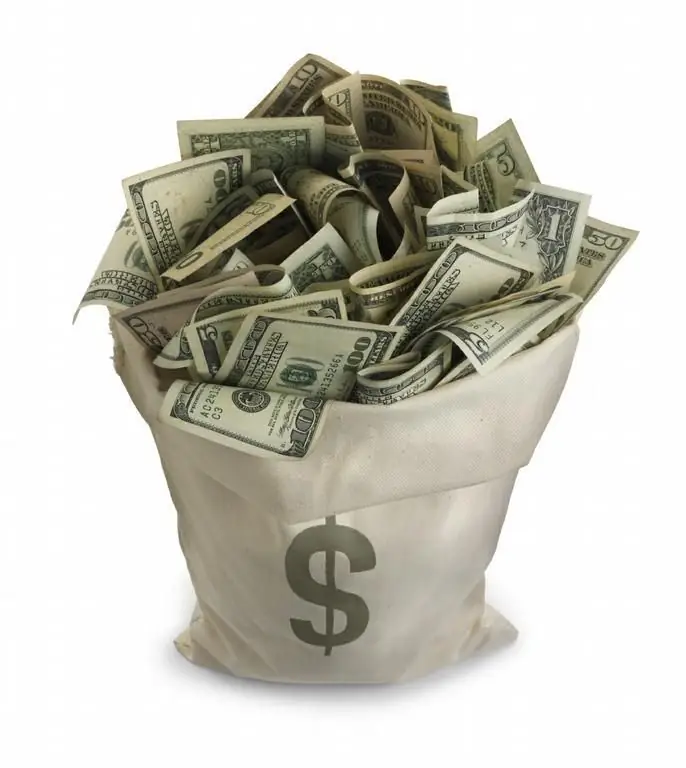
Collective investment is a type of trust management with a low entry threshold that allows small investors to invest in the stock market, real estate market, precious metals and others, making a profit from investing their money. This is an investment of the joint capital of investors, which makes it possible to earn money by significantly increasing their capital
Self-insurance is Definition, basic principles, advantages and disadvantages
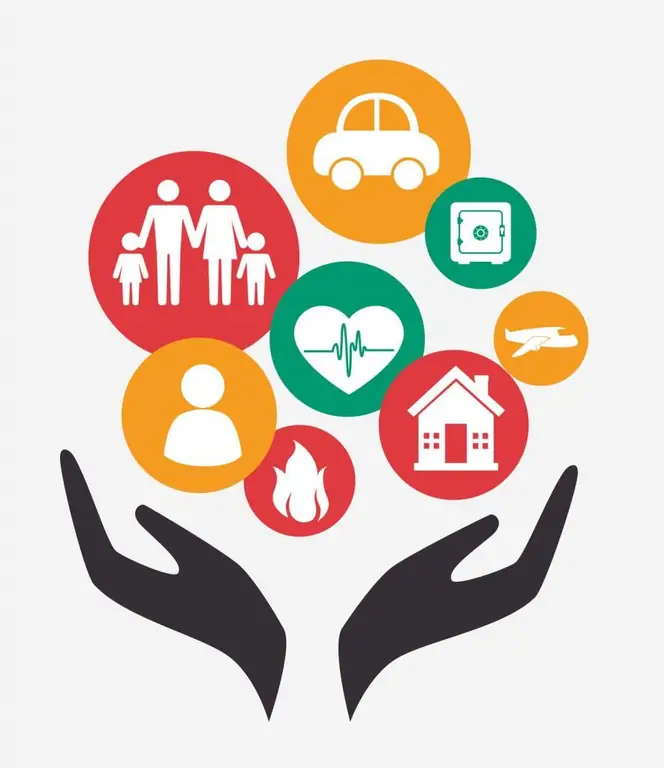
What is self-insurance? What are its features, main forms? Historical development of the phenomenon. Characteristic features of self-insurance. How are reserve funds formed? When is self-insurance necessary? Its development today: who will benefit, why is it not common on the market?