2025 Author: Howard Calhoun | [email protected]. Last modified: 2025-01-24 13:10
An integral part of freight rail transportation is sorting work, within which trains are assembled for shipment in one direction or another. The stations at which the redistribution of goods is carried out are called sorting stations. In their work, they use many special devices, the main of which is a sorting hill. Let's find out what it is and how it works.
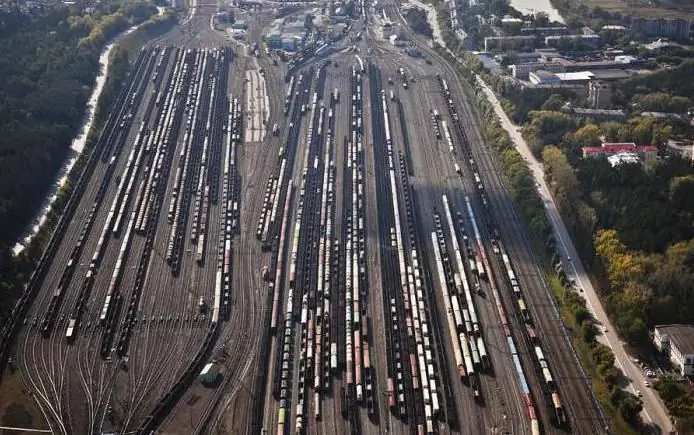
General characteristics
A hump is a structure located on the territory of a railway station and designed to form or disband freight trains. In fact, it is an embankment on which railway tracks are laid. The design consists of three main sections: the sliding part, the hump and the lower part. The train moves up the hill with the help of a locomotive. Then, under the influence of gravity, each wagon independently rolls to its destination along the lowering part, which is located on a slope. Betweenwagons or cuts (several connected wagons) rolling down the hill form an interval sufficient to transfer the switches in accordance with the train formation plan. The rolling speed of the wagons is controlled by brake positions, which are equipped with wagon retarders.
Basic concepts
The top of the hill is called its highest point. Usually its height is from 3.5 to 4.5 meters. Here, wagons or cuts are sent to the subhill tracks according to their destinations. The height of the hill is the difference between its top and the calculated point of the most unfavorable for rolling downhill path. The height is calculated in such a way as to ensure the passage of a wagon with poor driving characteristics under adverse natural conditions to the design point, which is taken with a margin at a distance of 50 m from the end of the braking position of the most difficult path. The hump of the hill is called its pass part, from which the wagon or cutter starts its independent movement down.
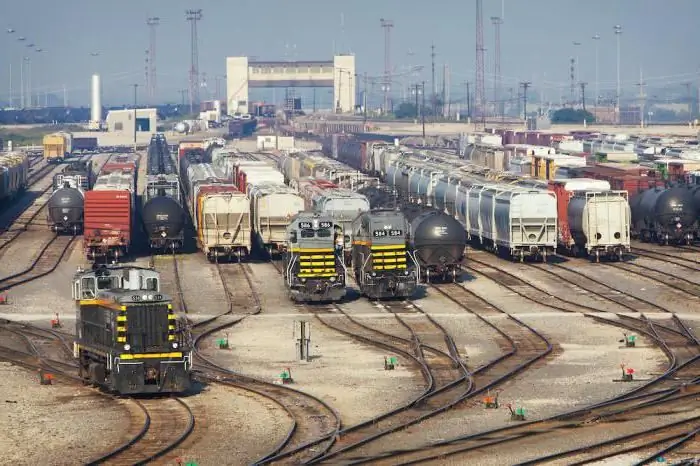
The sliding part is the area between the last turnouts of the foothill mouth of the receiving park and the top of the hill. This zone, as a rule, is equipped with an anti-slope for the convenience of uncoupling the cars and stopping them. The descent part, respectively, is called the area between the top of the hill and the beginning of the marshalling yard. At the same time, the section of the path with the greatest steepness is called high-speed.
Types of humps
Hump complexes can be either one-sided or two-sided. The latter are usually used on especially largesorting yards, with a large amount of work in both directions. Previously, slides were built only in areas with a natural slope of the earth. Many of these slides are still in operation today. Later they began to build slides with an artificial slope.
The methods used for braking cars may also differ. It all depends on the point at which the sorting hill is located. Stations that were built near transport hubs ended up within the city over time. Such sorting complexes are subject to special requirements. We are talking about the silent operation of retarders and turnout drives, special rules for the dissolution and limited access to the territory of the station.
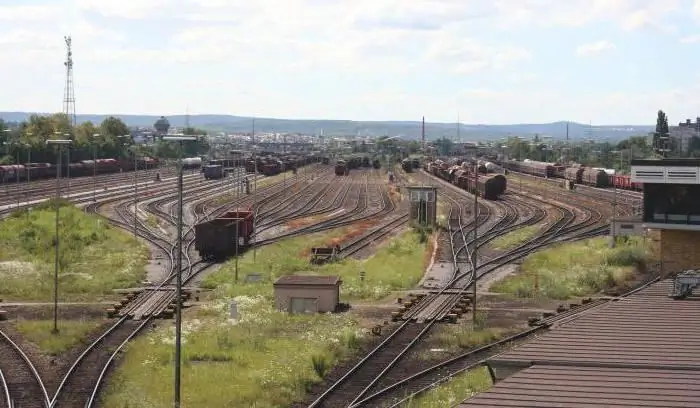
Types of marshalling yards
The marshalling yard can be the same length as the other yards in the station, or shortened. Shortened parks are most common in America, where favorable terrain and long distances between stations make it possible to form especially long trains. Shortened trains, assembled in one marshalling yard, are connected on the departure routes with other semi-trains. At the same time, there are cases when it is more expedient to design long marshalling yards. It all depends on the specific region.
Latest generation marshalling yards provide local control of elements such as in/out park switches and signalers, with the ability to check all necessary closures and dependencies. Less common is the centralized management of the railway, marshallingstation in particular.
Braking cuts in the hump zone
The first braking of the cutter takes place in the hump zone to form following intervals. It is carried out by one or two TP (brake positions). The next braking is targeted, takes place in the park area, when the car reaches its destination.
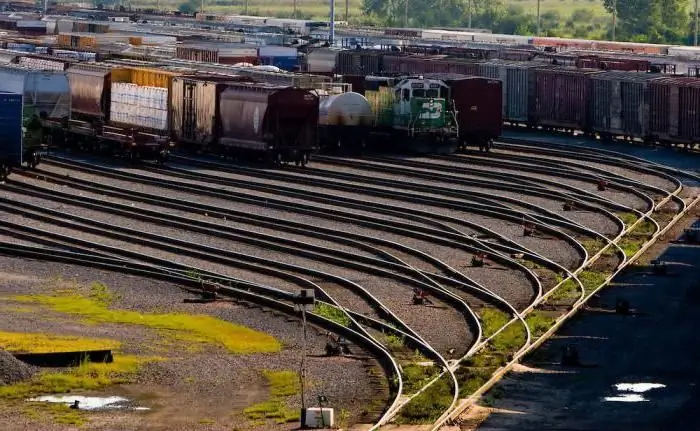
In addition to the pincer-shaped pressure retarders known at the stations of Russian Railways, other braking systems are also used. For example, at stations located near residential areas, rubber-coated rails are used to dampen the speed of trains. The friction force arising from the movement of a metal wheel on a rubber coating is regulated by a retarder. The most promising are the braking positions of the hump, equipped with permanent magnets. They are most effective at high haul speeds (over 20 km/h).
Braking cuts in the park area
In park areas for braking cars or cuts, a certain number of point retarders are installed, which provide quasi-continuous speed control. The most recognized at the moment are the point hydraulic piston models of retarders. They are activated when the wheel flange runs over the retarder piston mounted on the rail neck. If the rolling speed is exceeded (registered using a special sensor), the excess kinetic energy is extinguished when the piston moves down.
In Europe, widea hydraulic spiral moderator has also become widespread. As the car passes over it, the wheel flange comes into contact with the helical projection of the cylinder, which makes a revolution, taking some of the energy from the wheel. The resistance that the car retarder will provide depends on how much the speed of the car exceeds the norm.
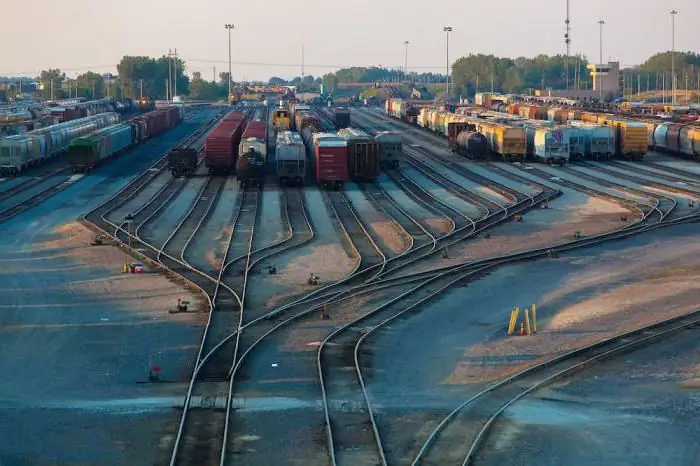
Braking at natural grade stations
In marshalling yards with a natural slope, speed control usually occurs throughout the descent, including the pre-park area. The slides of the latest generations are equipped with car-loaders, which are located directly inside the rail track and can be moved using automatically controlled cables. If necessary, the wagon evacuator can even bring the cutter to the wagons to which he is to join. Such devices are widely used at railway stations in Munich, Zurich and Rotterdam.
Besides braking devices, hump yards are also equipped with hydraulic accelerators. They are usually located in the park area and are activated if the cutter moves at a speed below the norm.
First slide systems
The first inclined track for wagon distribution was built in Dresden in 1946. At that time, another way of disbanding trains was common in Europe - with turntables. In 1858, the first semblance of a hump system was built at the Leipzig station. In the form in which the marshalling yard functions today, it was first builtin 1863 at the French station Ter Nord.
First counterslope
In 1876, at the German station Speldorf, the first sorting station was built with a counterslope on the sliding part and an intermediate platform. Previously, slides were built on a natural slope, without a counterslope. In 1891, they began to use the division of the marshalling yard into bundles (groups of tracks). Instead of brake devices, brake shoes were then used. These simple devices can still be found at stations with a natural slope.
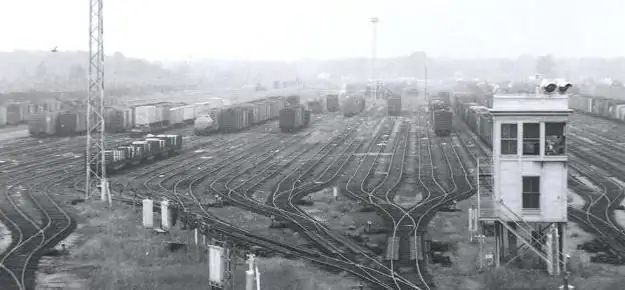
First retarder
In the twenties, centuries passed in Europe and America began to use a beam-type car retarder. In 1923, a mechanized complex of four hydraulic retarders was launched at the European station Hamm. Thanks to the mechanisms of electromechanical interlocking that appeared at about the same time, it became possible to remotely control the railway in the section of the marshalling yard. Somewhat later, the first electrical devices were created that memorize the order in which the cars passed. In accordance with the set task, they independently adjusted the switch drives of the beams.
Full automation
In 1955, the first controlled slide complex was launched at Chicago's Kirk station. By the 1970s, most major stations had fully automated hump yards. A little later, they began to use the radio channel to control locomotives, which allowed them to increase productivity.work.
Alternative options
In the second half of the twentieth century, there was a trend towards the predominance of small freight shipments. Due to the growing competition between rail and other types of freight transport, container transportation has become relevant, which allows minimizing the cost of transshipment and enjoying the advantages of each type of transport. In order to reload containers from railway wagons to road and sea transport, special sites with crane mechanisms were equipped. With the development of container shipments, many marshalling yards in Europe have transferred their functions to fleets that can reload containers from wagons not only to sea and road transport, but also to other trains.
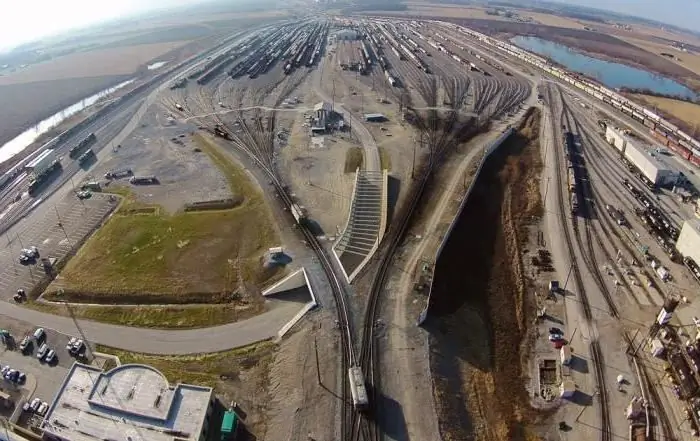
MSR 32 Complex
Siemens has developed a special MSR 32 complex for the construction and modernization of railway sorting yards. Depending on the type and capacity of the required hump, as well as its profile and local conditions, it creates a model that is tested using electronic computers. The model shows where it is most appropriate to place speed sensors, weights, cut gauges, brake positions and other elements of the marshalling yard.
The system adapts to any customer requirements thanks to its modular design. It is implemented in slides with different profiles, braking concepts and processing capacities. For example, in Zurich, a slide equipped with the MSR 32 system handles 330wagons per hour. The locomotive is controlled by radio. In Vienna, a similar split point has a capacity of 320 wagons per hour. The locomotive of this slide is radio-controlled. The system provides a continuous exchange of information with dispatch centers on all slides. The hump operator only has to make sure that everything works as it should. The first station in the former USSR where Siemens installed its technology was the Vaidotai station in Lithuania. Gradually, MSR 32 technology is spreading around the world. They are also being tested at the stations of Russian Railways OJSC.
Recommended:
Waste sorting complex: equipment for sorting and processing household waste
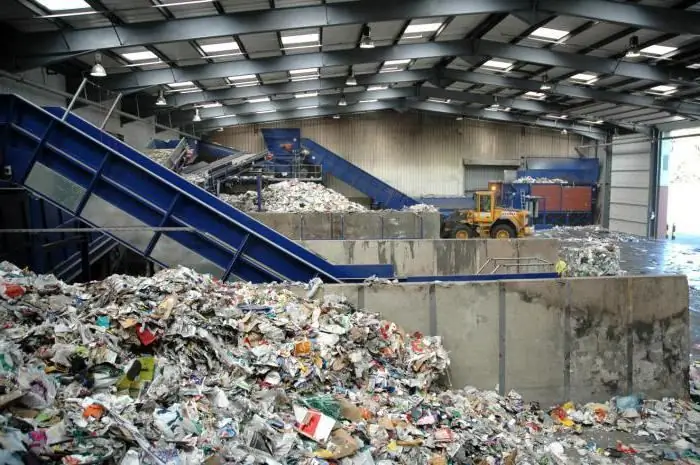
The article is devoted to waste sorting complexes. The features of this equipment, the technological steps performed, etc. are considered
Railway station. RZD: map. Railway stations and nodes
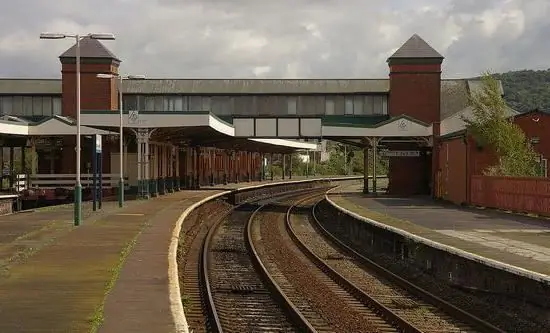
Railway stations and junctions are complex technological facilities. These elements form a single track network. Later in the article we will consider these concepts in more detail
Work permit for work in electrical installations. Rules for work in electrical installations. Work permit
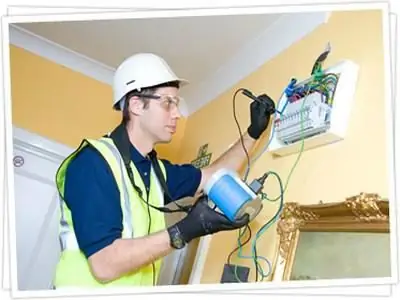
From August 2014, Law No. 328n comes into force. In accordance with it, a new edition of the "Rules on labor protection during the operation of electrical installations" is being introduced
Re-sorting of goods is a simultaneous shortage of one item of goods and a surplus of another. Accounting for sorting during inventory
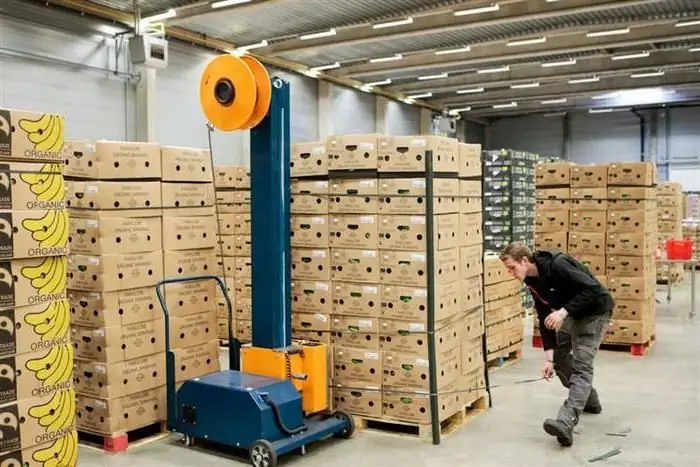
When conducting an inventory at trading enterprises, shortages, surpluses, and regrading are often revealed. With the first two phenomena, everything is more or less clear: there is either a lot of this or that product, or a little. Re-sorting of goods is a rather unpleasant and difficult situation
Welding in a shielding gas environment: work technology, process description, execution technique, necessary materials and tools, step-by-step work instructions and expert advice
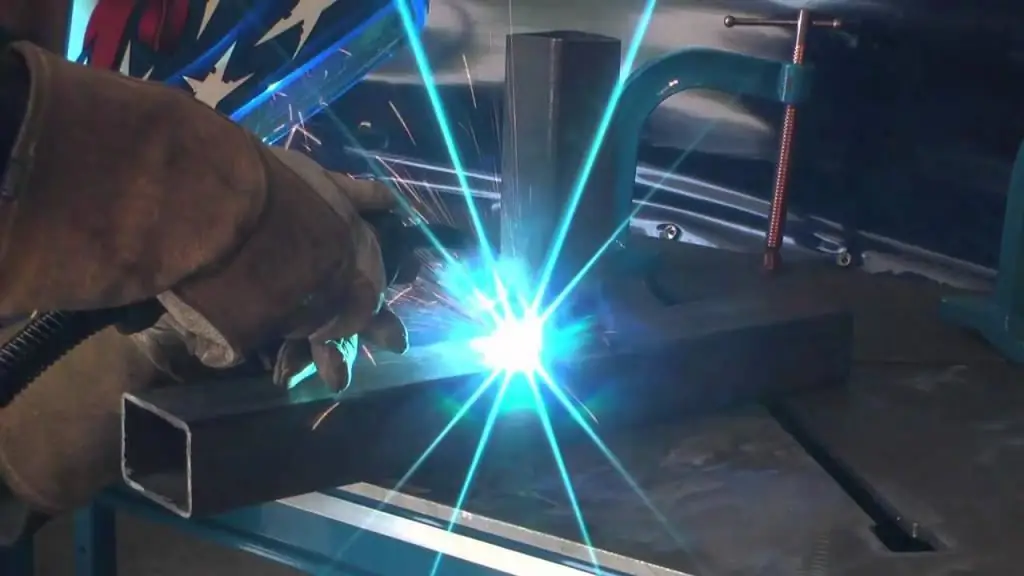
Welding technologies are used in various branches of human activity. Versatility has made welding in a protective gas environment an integral element of any production. This variety makes it easy to connect metals with a thickness of 1 mm to several centimeters in any position in space. Welding in a protective environment is gradually replacing traditional electrode welding