2025 Author: Howard Calhoun | [email protected]. Last modified: 2025-01-24 13:10
The welding arc itself is an electric discharge that exists for a long time. It is located between electrodes under voltage, located in a mixture of gases and vapors. The main characteristics of the welding arc are temperature and rather high, as well as high current density.
General Description
Arc occurs between the electrode and the metal workpiece being worked on. The formation of this discharge occurs due to the fact that an electrical breakdown of the air gap occurs. When such an effect occurs, the ionization of gas molecules occurs, not only its temperature rises, but also its electrical conductivity, the gas itself passes into the plasma state. The welding process, or rather the burning of the arc, is accompanied by such effects as the release of a large amount of heat and light energy. It is because of the sharp change in these two parameters in the direction of their large increase that the process of melting of the metal occurs, since in a local place the temperature increases several times. The combination of all these actions is called welding.
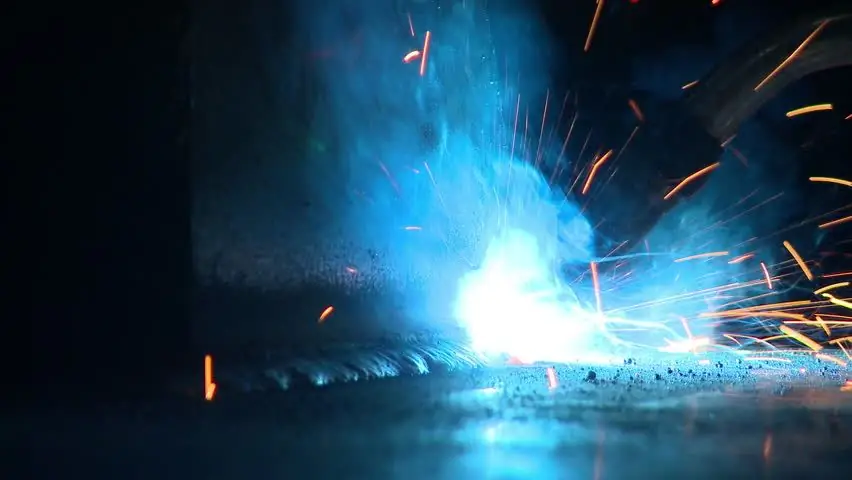
Arc properties
In order for an arc to appear, it is necessary to briefly touch the electrode to the workpiece with which to work. Thus, a short circuit occurs, due to which a welding arc appears, its temperature rises quite quickly. After touching, it is necessary to break the contact and establish an air gap. So you can choose the required arc length for further work.
If the discharge is too short, the electrode may stick to the workpiece. In this case, the melting of the metal will take place too quickly, and this will cause the formation of sagging, which is highly undesirable. As for the characteristics of an arc that is too long, it is unstable in terms of combustion. The temperature of the welding arc in the welding zone in this case will also not reach the required value. Quite often you can see a crooked arc, as well as strong instability, when working with an industrial welding machine, especially when working with parts that have large dimensions. This is often referred to as magnetic blowing.
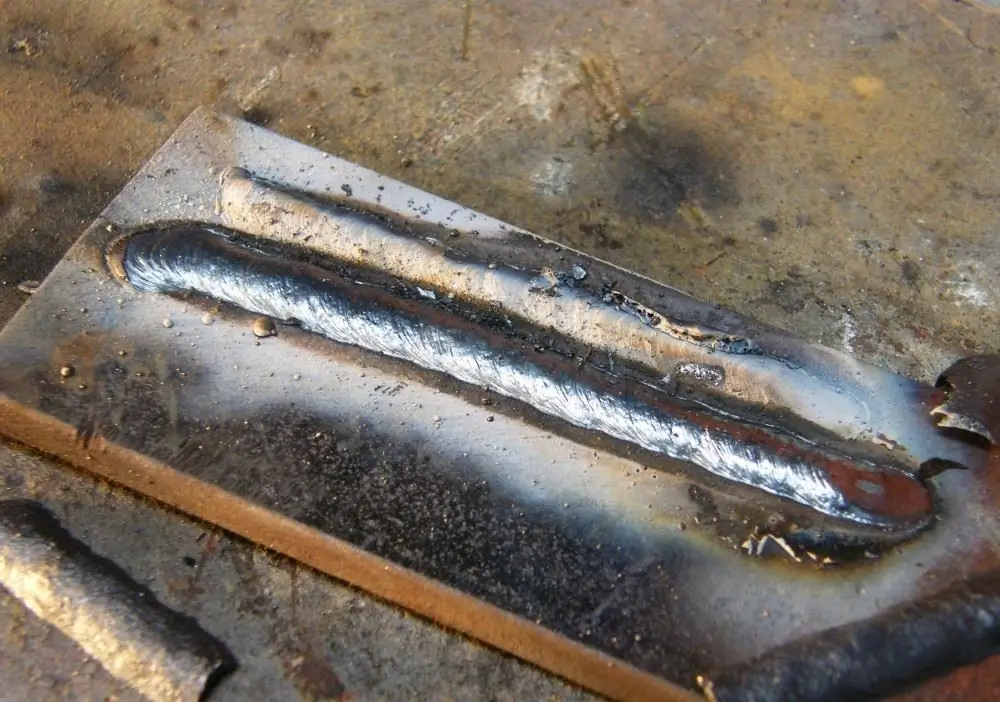
Magnetic blast
The essence of this method is that the welding current of the arc is able to create a small magnetic field, which may well interact with the magnetic field that is created by the current flowing through the element being processed. In other words, the deflection of the arc occurs due to the fact that some magnetic forces appear. This process is called blowing because the deflection of the arc withside looks like it is due to a strong wind. There are no real ways to get rid of this phenomenon. To minimize the influence of this effect, a shortened arc can be used, and the electrode itself must be located at a certain angle.
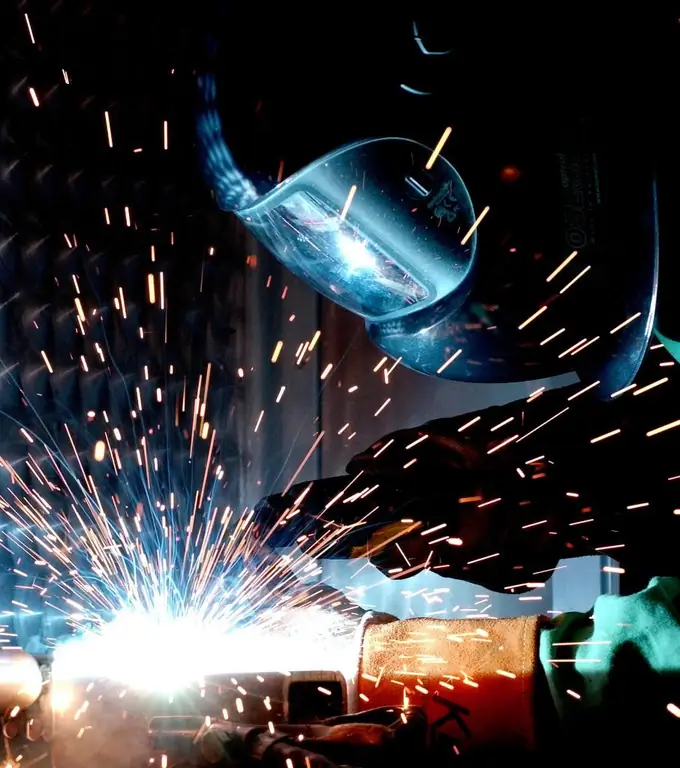
Arc structure
Currently, welding is a process that has been analyzed in sufficient detail. Because of this, it is known that there are three regions of arc burning. Those areas that are adjacent to the anode and cathode, respectively, the anode and cathode area. Naturally, the temperature of the welding arc in manual arc welding will also differ in these zones. There is a third section, which is located between the anode and cathode. This place is called the pillar of the arc. The temperature required to melt steel is approximately 1300-1500 degrees Celsius. The temperature of the welding arc column can reach 7000 degrees Celsius. Although it is fair to note here that it is not completely transferred to the metal, however, this value is enough to successfully melt the material.
There are several conditions that must be created to ensure a stable arc. A stable current with a strength of about 10 A is required. With this value, a stable arc with a voltage of 15 to 40 V can be maintained. It is worth noting that the current value of 10 A is minimal, the maximum can reach 1000 A. in the anode and cathode. A voltage drop also occurs in an arc discharge. After thecertain experiments, it was found that if consumable electrode welding is carried out, then the greatest drop will be in the cathode zone. In this case, the temperature distribution in the welding arc also changes, and the largest gradient falls on the same area.
Knowing these features, it becomes clear why it is important to choose the right polarity when welding. If you connect the electrode to the cathode, you can achieve the highest temperature of the welding arc.
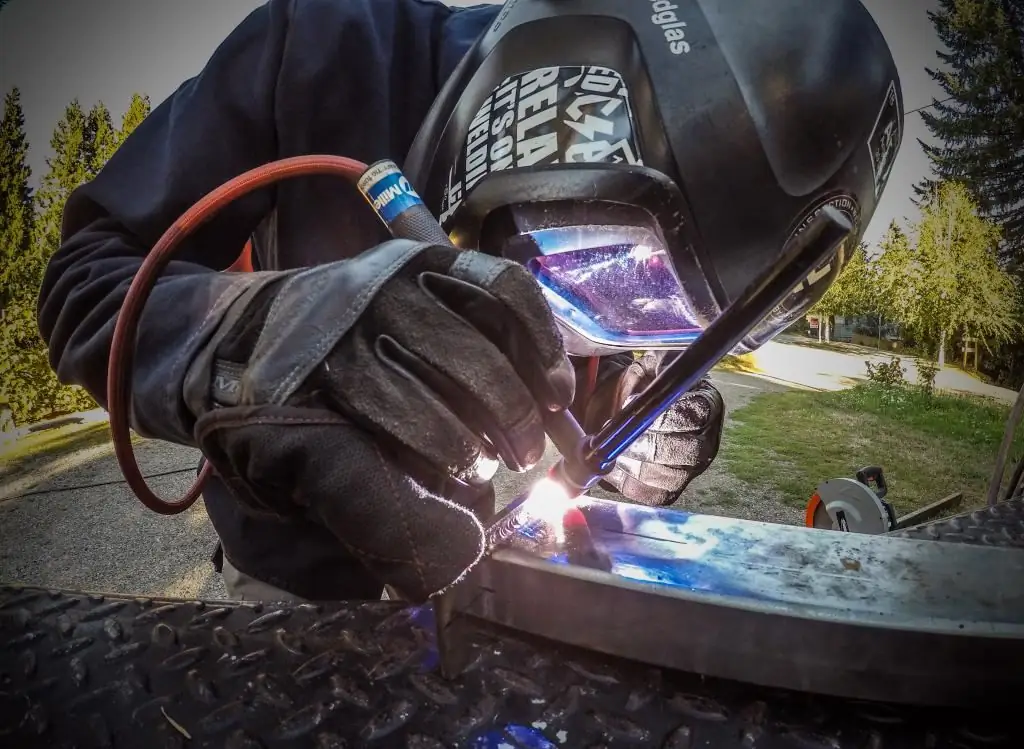
Temperature zone
Despite what kind of electrode is being welded, consumable or non-consumable, the maximum temperature will be at the column of the welding arc, from 5000 to 7000 degrees Celsius.
The area with the lowest temperature of the welding arc is shifted to one of its zones, anode or cathode. In these areas, 60 to 70% of the maximum temperature is observed.
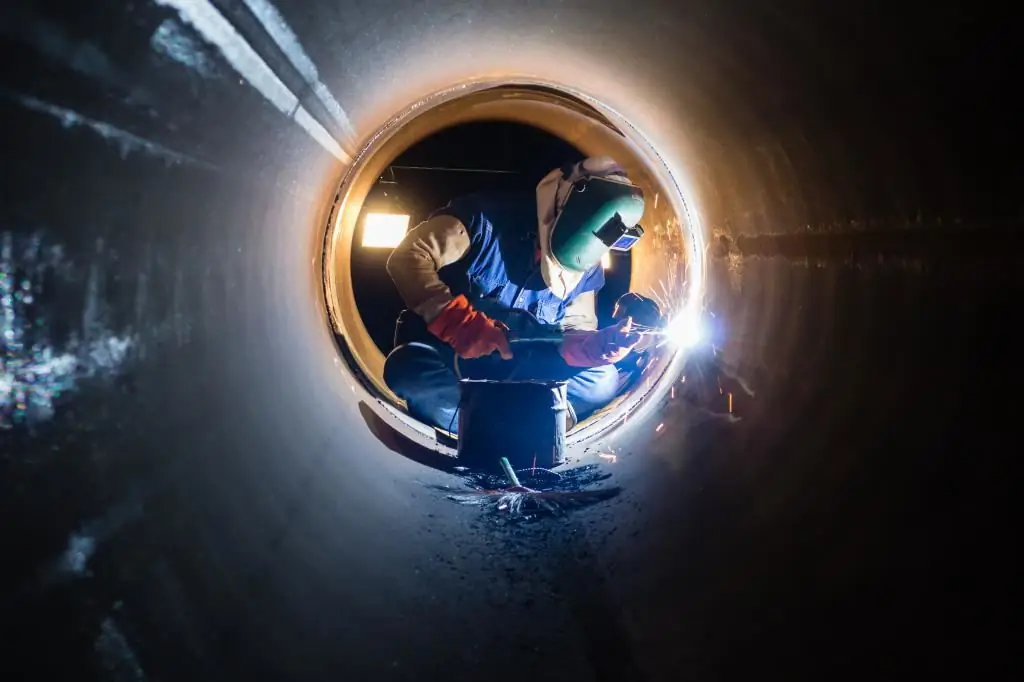
AC welding
All of the above related to the procedure for welding with direct current. However, alternating current can also be used for these purposes. As for the negative sides, there is a noticeable deterioration in stability, as well as frequent jumps in the temperature of the welding arc. Of the advantages, it stands out that simpler, and therefore cheaper equipment can be used. In addition, in the presence of a variable component, such an effect as magnetic blowing practically disappears. The last difference is that there is no need to choose polarity, sinceas with alternating current, the change occurs automatically at a frequency of about 50 times per second.
It can be added that when using manual equipment, in addition to the high temperature of the welding arc in the manual arc method, infrared and ultraviolet waves will be emitted. In this case, they are emitted by a discharge. This requires maximum protective equipment for the worker.
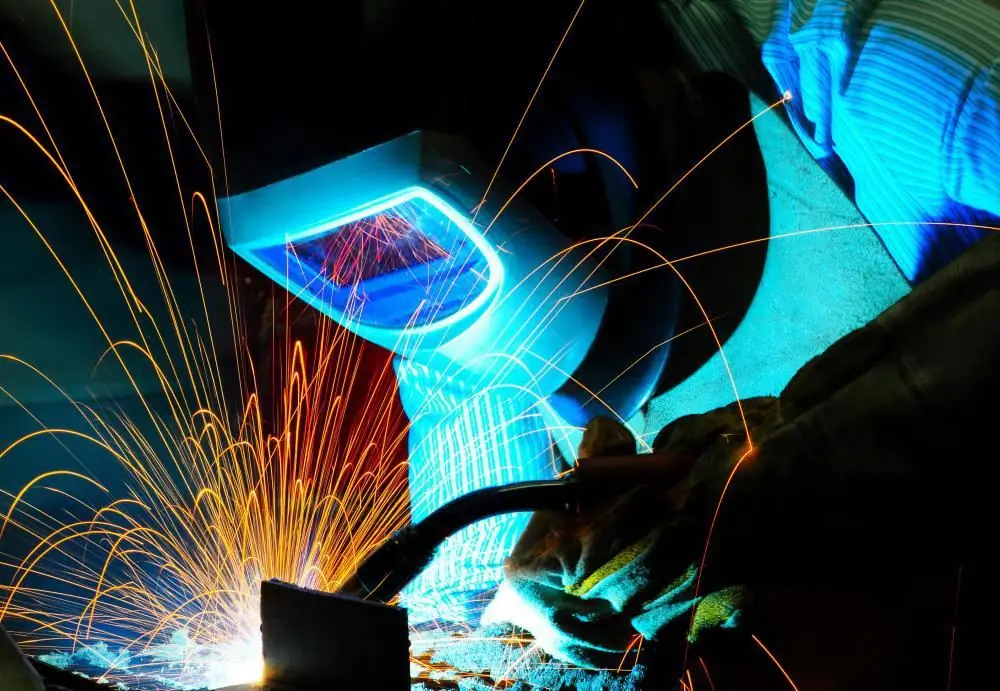
Arc burning environment
Today, there are several different technologies that can be used during welding. All of them differ in their properties, parameters and temperature of the welding arc. What are the methods?
- Open way. In this case, the discharge is burning in the atmosphere.
- Closed way. During combustion, a sufficiently high temperature is formed, causing a strong release of gases due to the combustion of the flux. This flux is contained in the slurry used to treat welded parts.
- Method using protective volatile substances. In this case, gas is supplied to the welding zone, which is usually presented in the form of argon, helium or carbon dioxide.
The presence of this method is justified by the fact that it helps to avoid active oxidation of the material, which can occur during welding, when the metal is exposed to oxygen. It is worth adding that, to some extent, the temperature distribution in the welding arc goes in such a way that a maximum value is created in the central part, creating a small own microclimate. In this case, it formsa small area of high pressure. Such an area is capable of obstructing the flow of air in some way.
Using a flux allows you to get rid of oxygen in the welding area even more effectively. If gases are used for protection, then this defect can be eliminated almost completely.
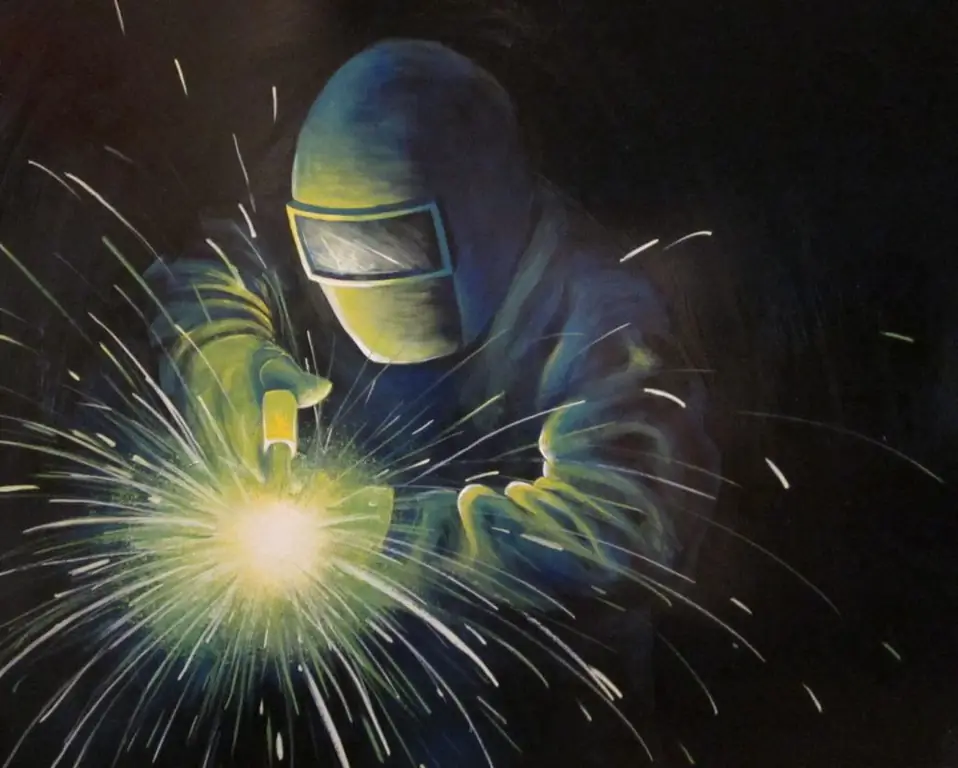
Classification by duration
There is a classification of welding arc discharges according to their duration. Some processes are carried out when the arc is in a mode such as pulsed. Such devices carry out welding with short flashes. For a short period of time, while flashing occurs, the temperature of the welding arc has time to increase to such a value that is enough to produce a local melting of the metal. Welding occurs very precisely and only in the place where the workpiece device touches.
However, the vast majority of welding tools use a continuous arc. During this process, the electrode is continuously moved along the edges to be joined.
There are areas called weld pools. In such areas, the temperature of the arc is significantly increased, and it follows the electrode. After the electrode passes the site, the weld pool leaves after it, due to which the site begins to cool rather quickly. When cooled, a process called crystallization occurs. As a result, a welding seam occurs.
Post temperature
It is worth analyzing the arc column and its temperature in a little more detail. The fact is that this parameter significantly depends on several parameters. First, the material from which the electrode is made strongly affects. The composition of the gas in the arc also plays an important role. Secondly, the magnitude of the current also has a significant effect, since with its increase, for example, the temperature of the arc will also increase, and vice versa. Thirdly, the type of electrode coating as well as the polarity are quite important.
Arc Elasticity
During welding, it is necessary to closely monitor the length of the arc also because such a parameter as elasticity depends on it. In order to obtain a high-quality and durable weld as a result, it is necessary that the arc burns stably and uninterruptedly. The elasticity of the welded arc is a characteristic that describes the uninterrupted combustion. Sufficient elasticity is seen if it is possible to maintain the stability of the welding process while increasing the length of the arc itself. The elasticity of the welding arc is directly proportional to such characteristics as the current strength used for welding.
Recommended:
Temperature standards at the workplace. What to do if the temperature at the workplace is above normal
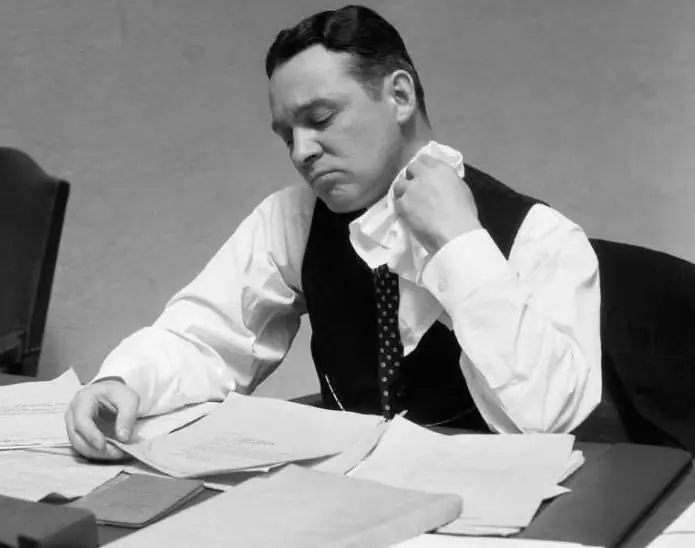
What external factors affect employee performance? Such a question, of course, should be asked by any leader who wants to take care of his subordinates and increase monthly revenue
The official currency of Morocco. Country currency. Its origin and appearance
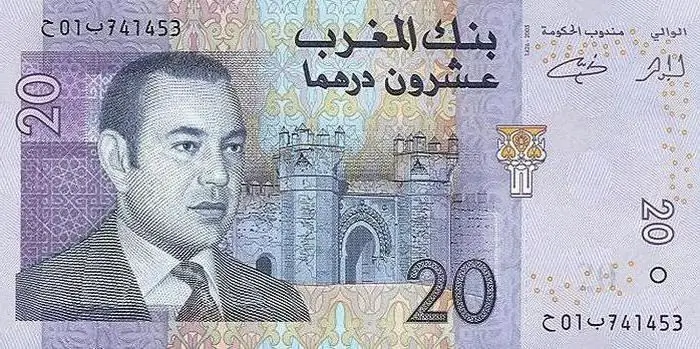
The official currency of Morocco. Country currency. Its origin and appearance. Where and how to change currency. Moroccan dirham to US dollar exchange rate
Welding of copper and its alloys: methods, technologies and equipment
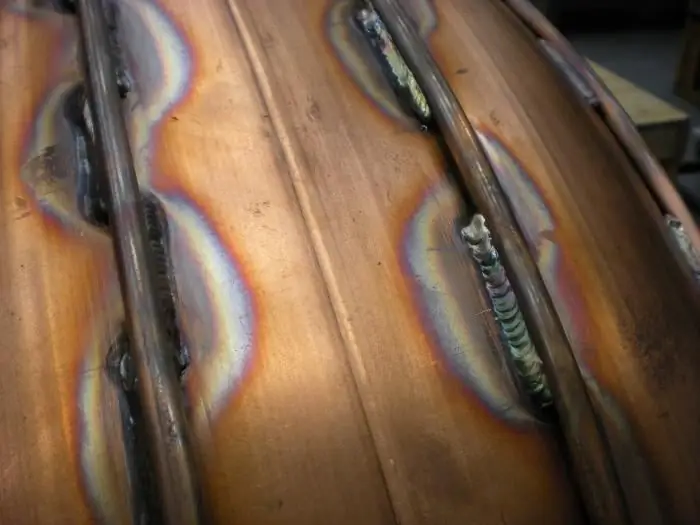
Copper and its alloys are used in various sectors of the economy. This metal is in demand due to its physicochemical properties, which also complicate the processing of its structure. In particular, the welding of copper requires the creation of special conditions, although the process is based on fairly common thermal treatment technologies
What is a gold coin: concept, appearance, year of issue and history of appearance
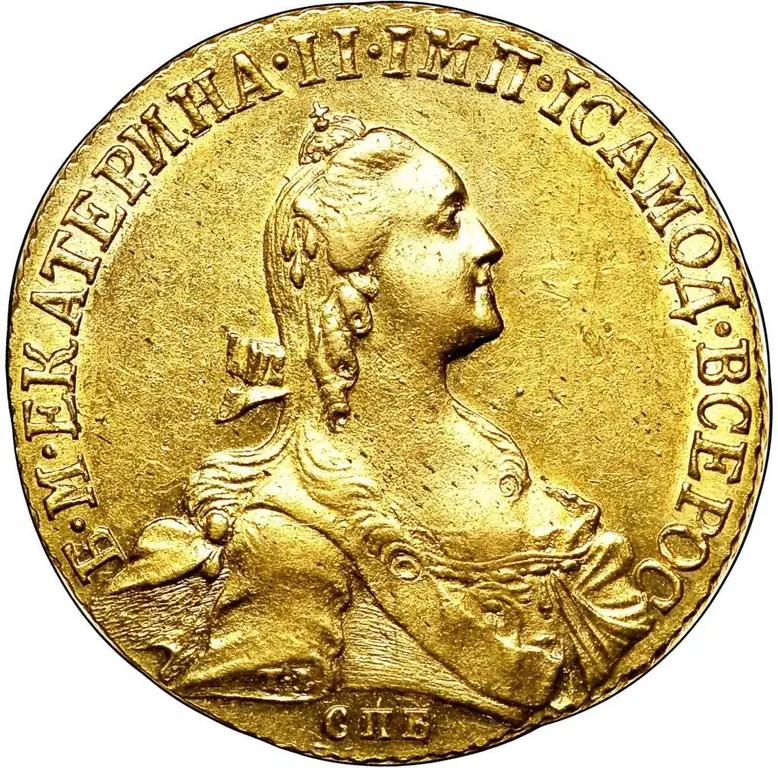
What is a gold coin? What is this word used to mean? What is the significance of this item? What is the history of this designation? How has the meaning changed? These, as well as a number of other, but similar questions, will be considered within the framework of the article
Welding arc is Description and characteristics
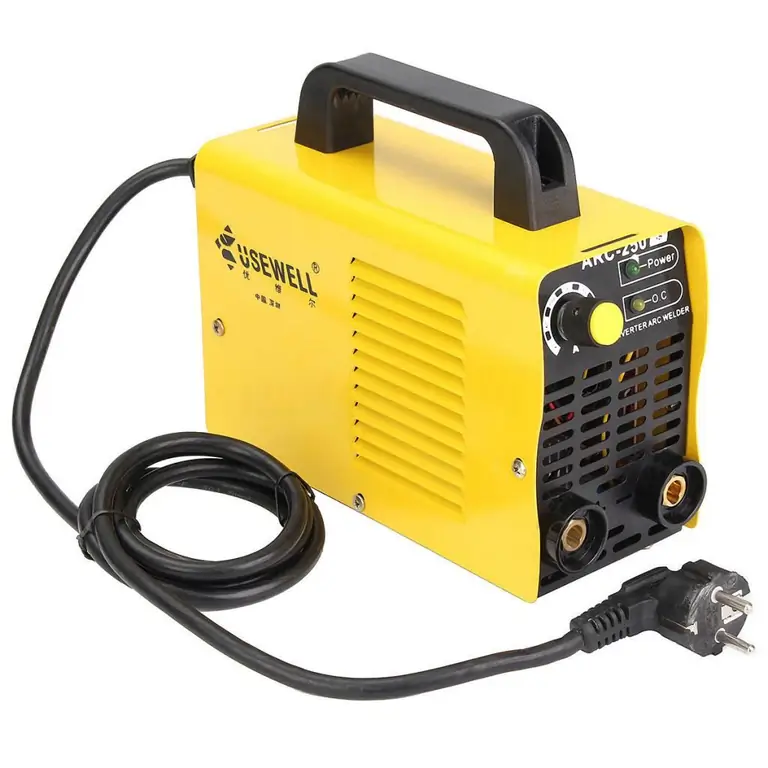
Today, welding is a process that is used very widely. With it, you can connect fairly large parts to each other. The connection itself also has good characteristics. The welding arc is the basis of the entire operation of this machine