2025 Author: Howard Calhoun | [email protected]. Last modified: 2025-01-24 13:10
Reserves of natural gas in the world are huge, but most of the deposits are located in hard-to-reach places, remote from industrial areas. This is not so bad - a pipeline can be laid on land or on the seabed. And for transportation across the ocean, the gas is converted into a liquid state. At the same time, the volume is reduced by almost six hundred times, which makes it possible to use not only pipelines, but also LNG tankers of a special design for gas transportation.
Liquefied gas carriers
LNG is natural gas cooled to -162°C, at which it changes from a gaseous state to a liquid state.
Most of the world's exports of liquefied gas are carried out on the intercontinental market by tankers of two types, abbreviated as CIS - liquefied petroleum gas and LNG - liquefied natural gas. Specialized vessels differ in tank design and are designed for different cargoes: LPG tankers carry liquefied propane, butane,propylene and other hydrocarbon gases, LNG tankers - methane. Sometimes these tankers are called methane carriers. The photo below shows a sectional view of the tanker.
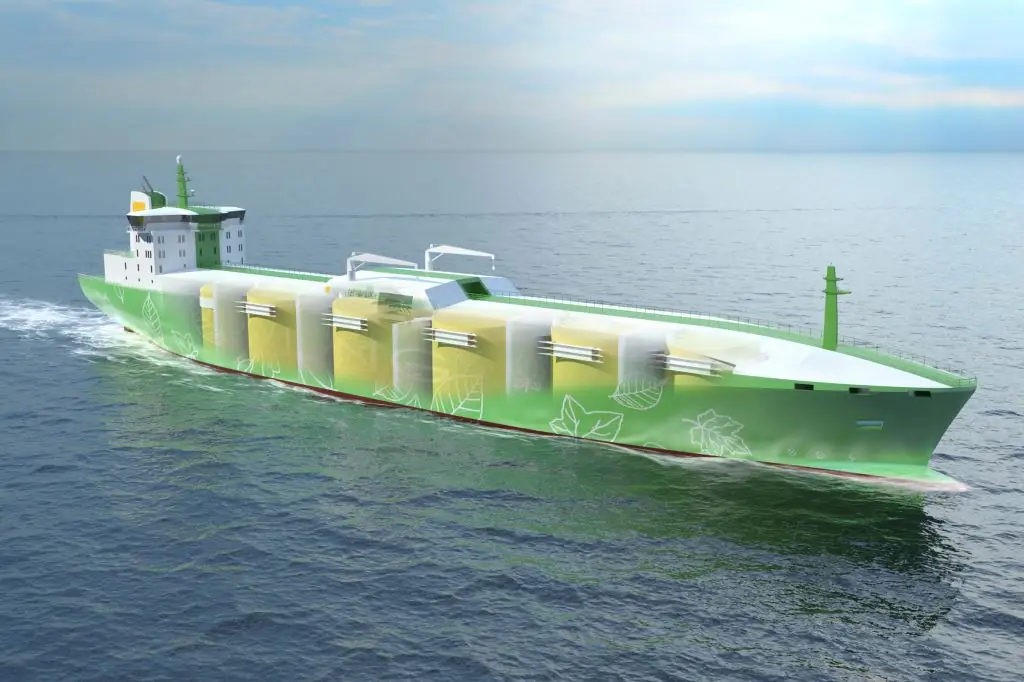
LNG tanker layout
The main components of an LPG tanker are propulsion and pumping units, a double hull for added strength, bow thrusters, LPG tanks and powerful refrigeration units to keep the gas temperature low.
As a rule, four to six isolated tanks are placed in the ship's hull, located along the center line of the ship. The environment of the tanks is a combination of ballast tanks, cofferdams - special compartments to prevent gas leaks from tanks and voids. This placement gives the LNG carrier a double hull design.
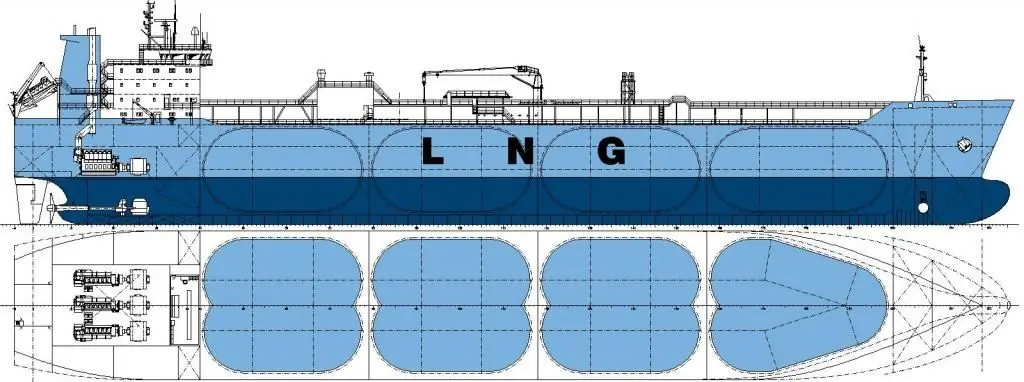
Liquefied gases are transported in tanks under pressure that is higher than atmospheric pressure, or at a temperature significantly below ambient temperature. Some tanks use both methods.
Tankers are equipped with pressure tanks of 17.5 kg/cm2. The gas is transported in cylindrical or spherical steel tanks with appropriate storage temperature. All tankers are built with a double bottom.
Gas carriers are equipped with powerful engines and are fast. The area of their rational application is long-distance, mainly transcontinental, flights, with a length of more than3000 nautical miles. Given the active evaporation of methane, the vessel must overcome this distance at high speeds.
Features of tank design
For the safe transportation of liquefied natural gas, it is required to maintain temperatures in tanks below -162 oC and high pressure. Tankers are equipped with membrane tanks with high-vacuum multilayer insulation. Membrane tanks consist of a primary metal barrier layer, an insulating layer, a liquid protective layer and a second insulating layer. The design of the tanks and the thickness of the metal hull of the tanks depend on the design operating pressure, temperature and displacement of the tanker. Under the pressure of sea water, the walls of the tank, being part of the ship, experience the same loads as the ship's hull.
Liquefied petroleum gases are also transported in spherical metal tanks well insulated to avoid leakage under high pressure.
IGC code defines three types of independent tanks used for gas transportation: A, B and C. LNG tankers are equipped with category B or C tanks, LPG tankers are category A tanks.
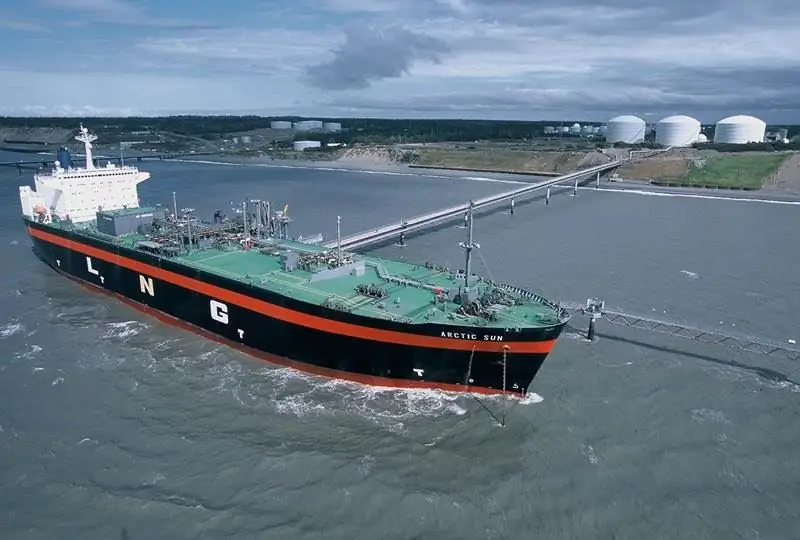
Tanker loading and unloading operations
The most dangerous operations are loading and unloading tankers. Liquefied natural gas is a cryogenic substance, the main component of which is methane. If it enters an unprepared cargo compartment with non-compliance with the temperature regime, the mixture of methane with air becomesexplosive.
The procedures for loading a tanker are strictly regulated. The cargo tank is dried with an inert gas at a certain temperature to prevent condensation of moist air inside the tank.
After drying the tanks, the hold is purged to remove the remaining inert gas, after which dry heated air is supplied to the hold under pressure.
Directly, the injection of liquefied gas is preceded by filling the reservoir with inert gas to remove air and cool the tanks. The insulating space of membrane tanks is purged with liquid nitrogen. Loading starts when the gas supply system and the tank are cooled down to a temperature close to that of the LNG.
At the port of destination, liquefied natural gas is transferred to the shore tank using a submersible cargo pump installed at the bottom of each cargo tank. During unloading, the requirements for temperature and humidity conditions of all lines are also observed in order to avoid the formation of an explosive mixture of methane with air.
Environmental safety
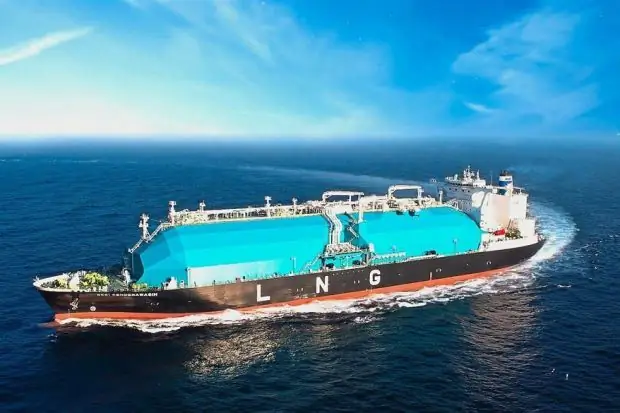
Strict safety standards are set by the International Code for the Construction and Equipment of Ships Carrying Liquefied Gases in Bulk (IGC Code). International regulations cover virtually every aspect of the safety of these vessels, as well as crew training standards.
The LNG ship safety record has an enviable history. Since 1959, when commercial LNG transportation began, there has never been a single death on board,associated with liquefied natural gas. There have been eight maritime incidents related to the accidental spill of liquefied natural gas around the world.
In June 1979, in the Strait of Gibr altar, the tanker El Paso Kaiser crashed into the rocks at a speed of 19 knots with a load of 99,500 m3. The vessel sustained heavy bottom damage along the entire length of the cargo spaces, but the membrane tanks were not damaged and no liquefied natural gas was spilled.
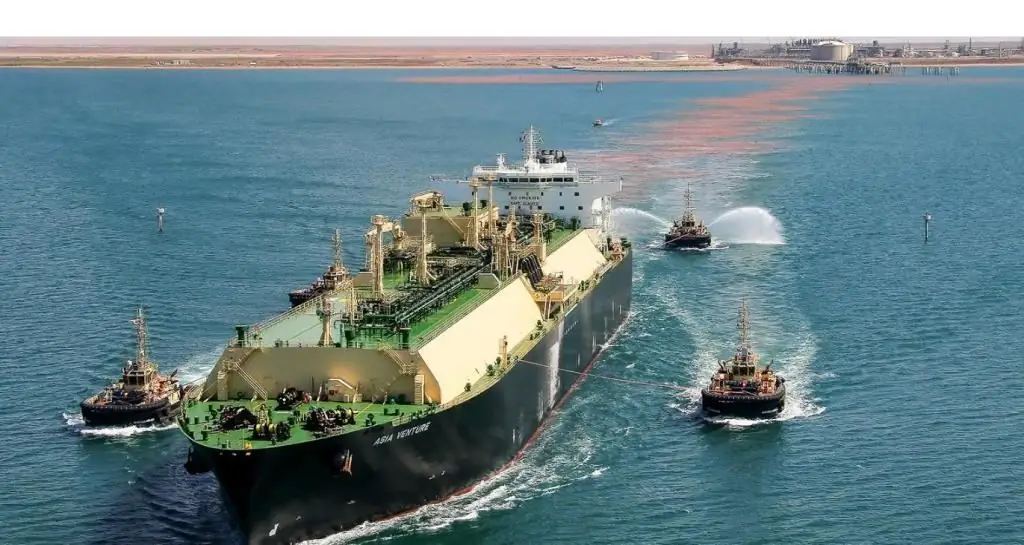
Navigation of tankers through the straits
Straits are the most dangerous place for navigation, therefore, for the construction of terminals for the production and reception of liquefied gas, they choose places on the outskirts of continents, avoiding difficult transport routes and tankers entering inland seas.
At one time, Ukraine announced its intention to build a terminal for receiving liquefied natural gas in the Odessa region in order to diversify the sources of gas supplies to the country. Ankara immediately reacted to this.
The constant transit of liquefied natural gas dangerous goods through the Dardanelles and the Bosphorus on LNG tankers can cause serious environmental damage. These straits are among the most dangerous in the world: the Bosphorus is in third place, the Dardanelles is in fifth place. In the event of a major accident, the consequences for the Sea of Marmara and densely populated Istanbul could be catastrophic.
International LNG Market
A fleet of specialized vessels links LNG production and regasification facilities around the world to create a safe, reliable and efficient networktransportation of liquefied natural gas. Methane carrier ships are equipped with state-of-the-art leak detection technology, emergency shutdown systems, advanced radar and positioning systems, and other technologies designed to ensure the safe and reliable transport of gas.
Liquefied natural gas now accounts for more than 35% of international natural gas trade, with ever-increasing demand.
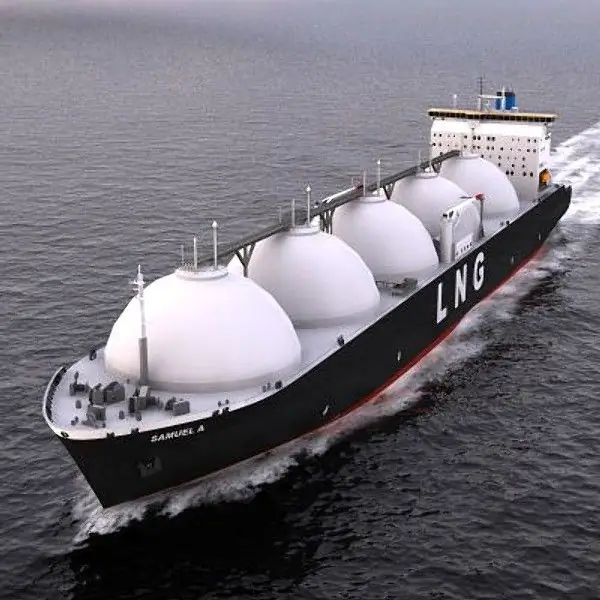
Some statistics
Today, the LNG industry worldwide includes:
- 25 LNG terminals and 89 LNG plants operate in 18 countries on five continents. Qatar is the world leader in LPG production, ahead of Indonesia, Malaysia, Australia and Trinidad and Tobago.
- 93 receiving terminals and regasification plants in 26 countries on four continents. Japan, Korea and Spain are the leading LPG importers.
- About 550 liquefied natural gas tankers are currently in operation worldwide.
Leader in the construction of LNG tankers
Historically, about two-thirds of the world's methane tanker fleet was built by the South Koreans, 22% by the Japanese, 7% by the Chinese, and the rest by France, Spain and the United States. South Korea's success is tied to innovation and price. South Korean builders built the first icebreaking-class methane tankers. They also built the largest LNG tankers of the Q-Flex and Q-Max class with a deadweight of 210,000 and 260,000cubic meters for the Qatari gas transmission company "Nakilat". A distinctive feature of class Q ships is the placement of a natural gas liquefaction plant directly on board the giant ship. The ship is 345 meters long and 53.8 meters wide.
Yamal LNG Project
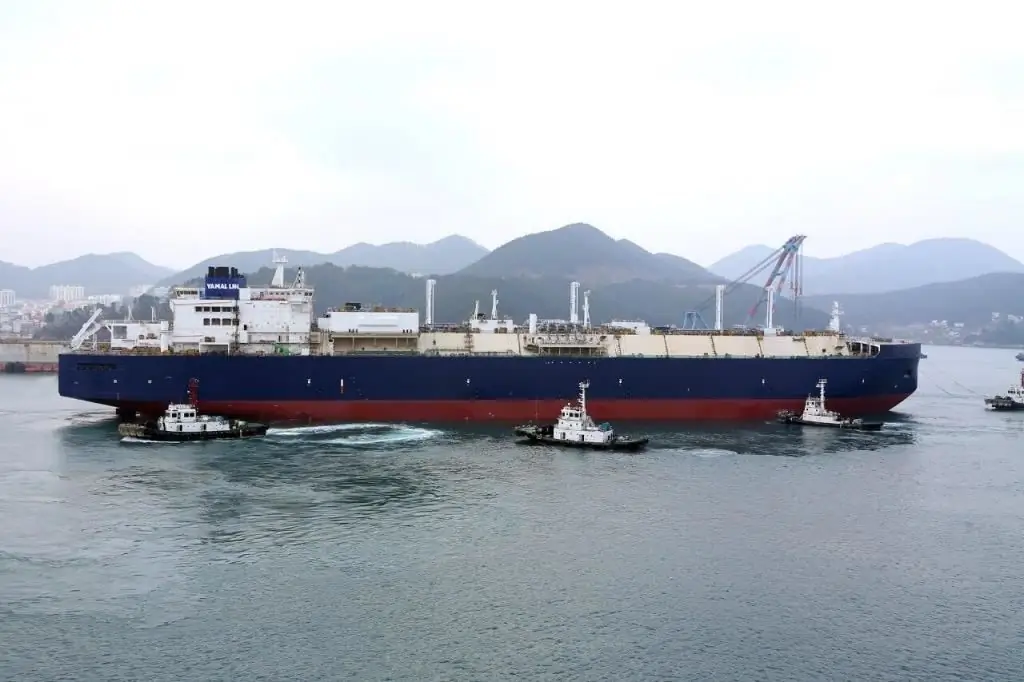
On September 29, 2014, a solemn ceremony was held to lay down a tanker ordered by the Russian shipping company Modern Commercial Fleet, which specializes in the transportation of energy carriers, to transport liquefied natural gas under the Yamal LNG project. These are unique vessels of the Arc7 ice class with the maximum possible dimensions for approaching the port of Sabetta on the Yamal Peninsula.
Designed to transport gas from the South Tambeyskoye field from the Arctic to Europe and Asia and navigate in the harsh climatic conditions of the Arctic, Yamal LNG tankers are double-acting vessels by design: the bow is for navigation in open water, and the stern is for navigation in difficult ice conditions.
Currently, five such ships have been built. Lead ship Christophe de Margerie. Owned by Sovcomflot.
In its very first commercial voyage, an LNG tanker from Russia set a historical record: for the first time in the history of shipping, a merchant vessel passed the Northern Sea Route without an icebreaker escort.
Recommended:
Liquefied natural gas (LNG): production, storage, transportation
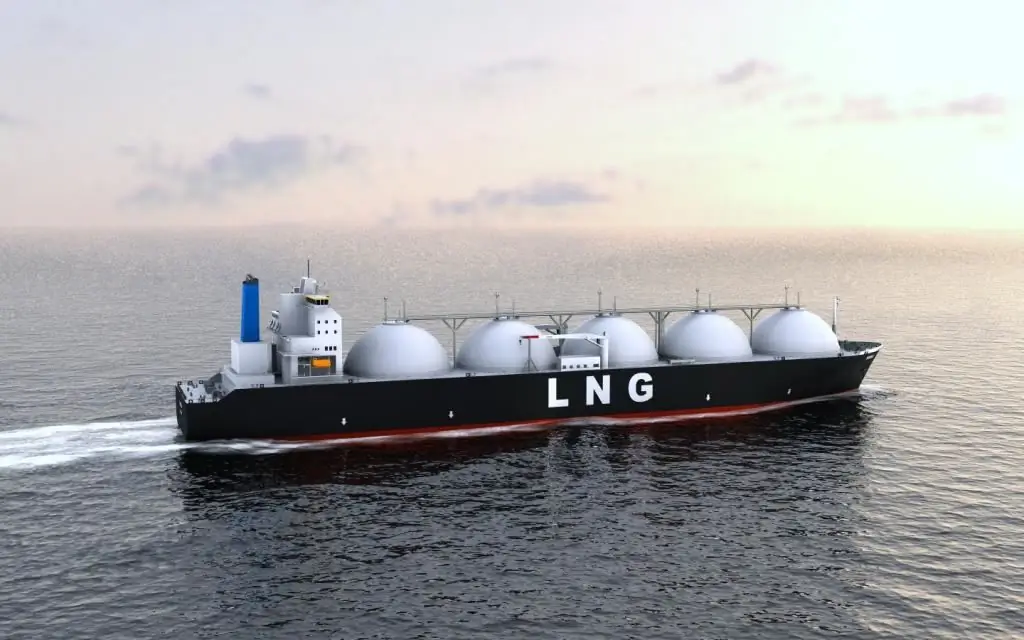
If we rank modern marine vessels in terms of aesthetics and design, then cruise ships will not win at all. Snow-white liquefied gas tankers will win, striking with their size, variety and unique designs. Liquefied natural gas production is no joke. This is big world politics
Gas production. Gas production methods. Gas production in Russia
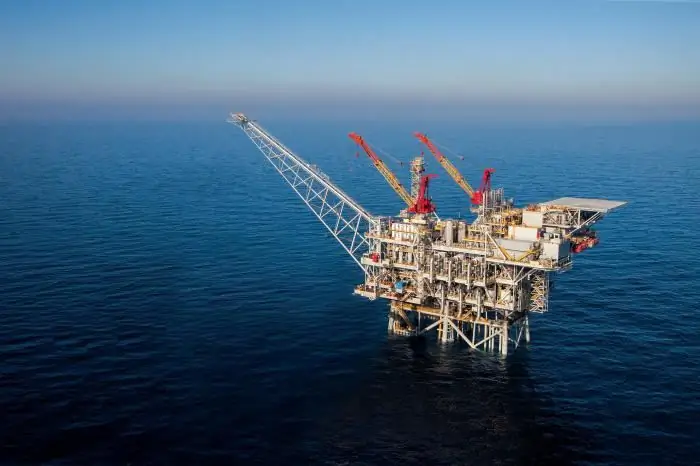
Natural gas is formed by mixing various gases in the earth's crust. In most cases, the depth of occurrence ranges from several hundred meters to a couple of kilometers. It is worth noting that gas can form at high temperatures and pressures. In this case, there is no access of oxygen to the place. To date, gas production has been implemented in several ways, each of which we will consider in this article. But let's talk about everything in order
Liquefied gas is the fuel of the future
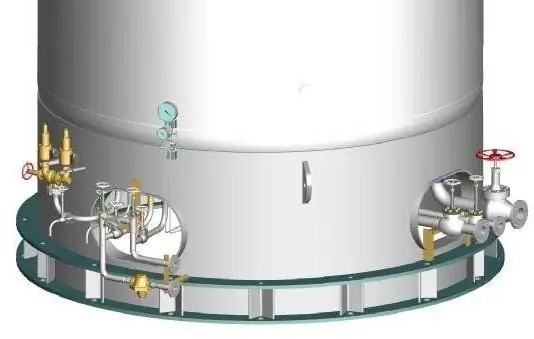
Global energy consumption is almost entirely based on the use of primary irreplaceable fossil fuels: coal, natural gas, peat, oil, and their derivatives, which are a wide range of petroleum products. Liquefied gas, considered one of the most promising and environmentally friendly fuels, can solve many of the energy and economic problems of mankind
Reviews: Yamal LNG, Russian gas company
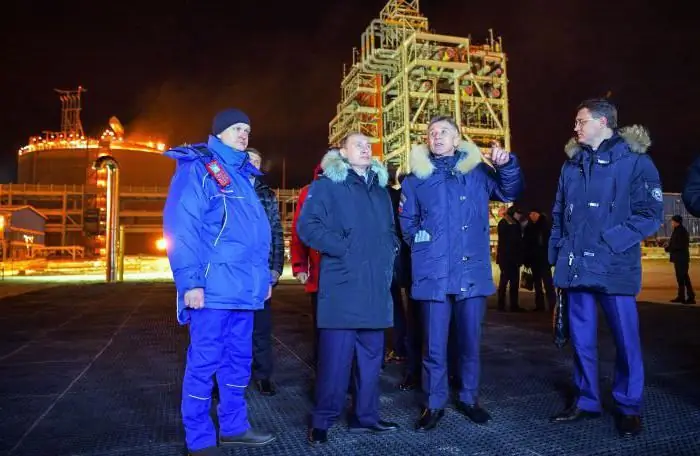
Reviews about Yamal LNG and the construction process of the complex were spoken with admiration, and now, after loading and sending the first tanker with liquefied gas to consumers, enthusiastic impressions go off scale. The Russian gas company Yamal LNG has done the impossible - cut a window from the harsh Arctic latitudes of Russia to the Asia-Pacific region and Europe
Transport taxes in Kazakhstan. How to check transport tax in Kazakhstan? Deadlines for paying transport tax in Kazakhstan
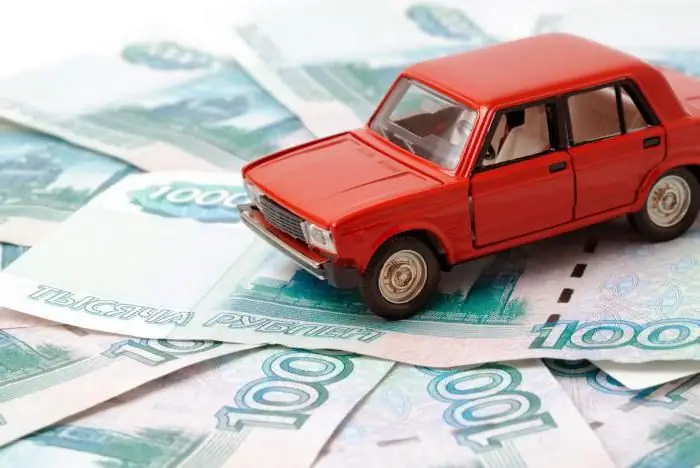
Tax liability is a huge problem for many citizens. And they are not always resolved quickly. What can be said about the transport tax in Kazakhstan? What it is? What is the procedure for paying it?