2025 Author: Howard Calhoun | [email protected]. Last modified: 2025-01-24 13:10
Glass is one of the most popular materials in demand for various spheres of life. It is used in construction and finishing works, works of applied and high art are made from it, and used in the space industry. This is one of the available, simple in composition materials. The most common type that we most often encounter and use products from it is silicate glass.
What is this?
Beads found during excavations in Egypt are considered the oldest piece of glass, scientists believe that the find is more than five thousand years old. Since then, the composition of the glass has changed little. The main element of the material is quartz sand (Si02) - silicate. Soda, potash, limestone and a few other elements are added to it.
In industry, to obtain a glass mass, oxides of basic substances are mixed and melted in a furnace. The melting point depends on additives that change the properties of the glass. The resulting mass is molded in several ways: by making sheet glass, by giving it various shapes (dishes, shades for chandeliers, glass for clocks, etc.), by making blanks for subsequent piece processing by glassblowers, and much more.
BLomonosov M. V., Kitaygorodsky N. I. made a significant contribution to the development of glassmaking, Mendeleev D. I. and others were interested in the practical side of the issue. It is easy to define the material "silicate glass". What it is? A material having an amorphous-crystalline structure of the structure, obtained by melting mixed oxides with subsequent cooling.
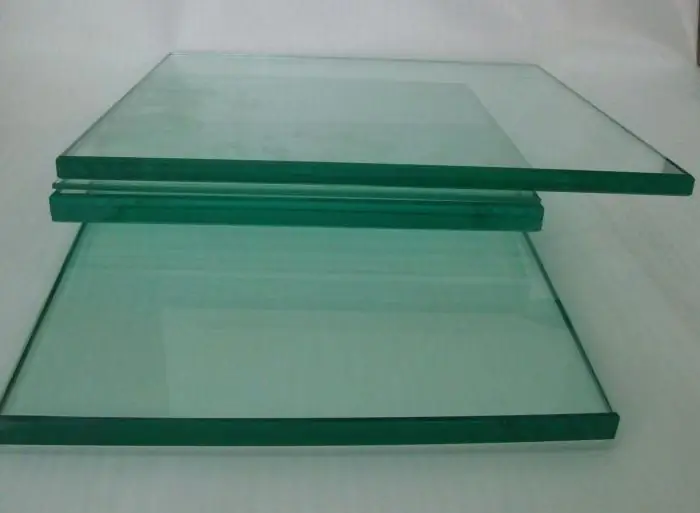
Glass making
The main element for the production of glass is quartz sand, to which at least five ingredients are added in proportions. Depending on the further purposes of using the obtained material, additives are made to the main recipe: oxidizing agents, silencing agents, decolorizers, dyes, accelerators, and so on. Metal oxides are used as dyes. For example, copper will color a mass of glass red, iron will give a blue or yellow tint, cob alt oxides will give a blue color, and colloidal silver will give a yellow tint.
The prepared dry mixture is loaded into a glass melting furnace, where the raw material is melted at a temperature of 1200-1600°C, the process takes from 12 to 96 hours. Glass production is completed by the rapid cooling process, only under this condition the glass mass will receive all the required qualities: transparency, mechanical resistance and additional properties laid down in the process of mixing oxides.
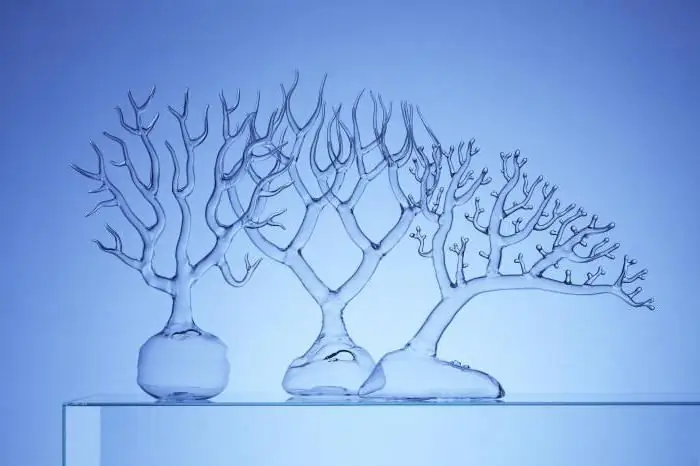
Types of silicate glass
Material production is an energy-intensive process, and is handled by the silicate industry. Glass production in the industry takes place intunnel type furnaces with continuous maintenance of the set temperature. Dry mix is loaded from one end of the kiln, finished material is unloaded at the exit.
Due to the wide application in various industries, silicate glass can be divided into types:
- Quartz without impurities of oxides of sodium, potassium is alkali-free glass. It has high resistance to heat and excellent electrical properties. Of the shortcomings - difficult to process.
- Soda, potassium, sodium-potassium - alkaline glass. The most common type of material suitable for general use. It is used to make glass for an aquarium, window glass, dishes and more.
- Alkaline with a high content of heavy metal oxides. For example, the addition of lead is necessary to obtain crystal, optical glass.
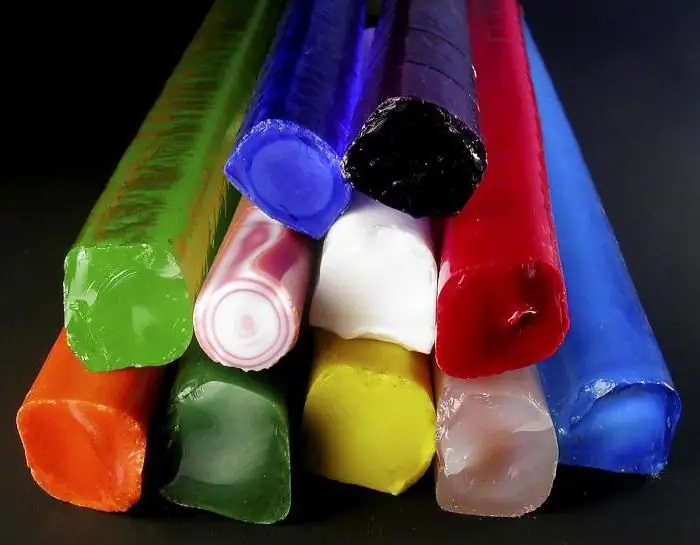
Multipurpose use
Silicate glass has a number of properties that allow it to be used in a wide range. Each of its qualities can be enhanced, in connection with which additional opportunities open up. For example, amalgam-coated glass serves as a mirror and can also be used as a solar panel under certain conditions.
The hygienic and practical properties of glassware are undeniable. The material does not have porosity, which means that pathogenic bacteria do not multiply in it, it is easy to clean, resistant to any food products. Heat-resistant dishes from it are multi-tasking: you can bake at a high temperature in the oven or put infreezer without any damage.
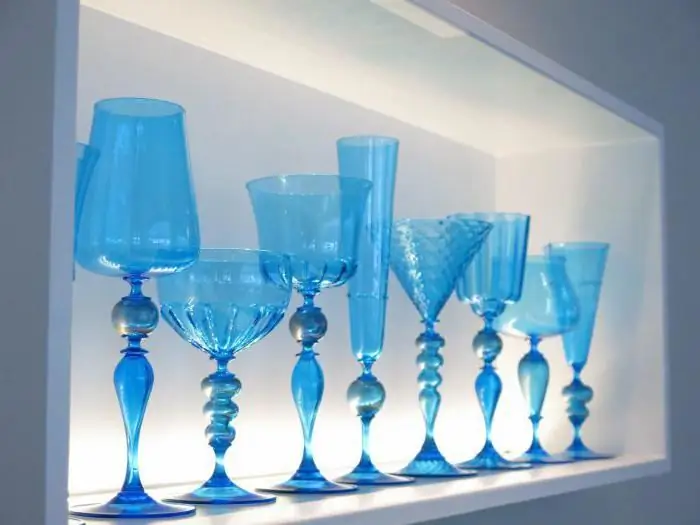
Layer and thickness
The material has a different thickness, which determines its capabilities. Sheet, 2 mm thick, suitable for windows. Glass for an aquarium is used at least 5 mm, depending on the volume of water poured into the tank. However, aquarists are increasingly coming to the conclusion that the use of an acrylic analogue is much more convenient, especially if a capacity of 500 liters or more is required.
The use of laminated material (triplex) expands the possibilities: the fabric glued with a polymer film is practically indestructible, it is safe, because it does not crumble. It is practically impossible to break two silicate glasses with a thickness of 10 mm with a film layer with a hammer. Triplex is used to make transparent bridges, cladding of building facades, pool fencing, etc.
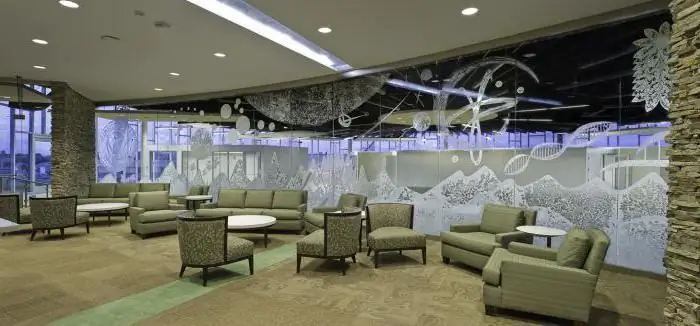
Properties
The use of silicate-based materials finds its place in construction. They are used not only for the manufacture of windows, but also as additional protection and a binder. So, foundation blocks are treated with liquid glass, which makes them resistant to moisture, fungus, temperature fluctuations, etc.
Curved translucent or matte material is used in everyday life, furniture doors, shower cabins, building facades and so on are made from it.
Silicate glass has the following properties:
- Transparency.
- Reflective.
- Sustainable.
- Heat resistant.
- Resistant to aggressive chemical environments.
- Resistant to natural aggressive environments.
- Durability.
- Low thermal conductivity.
Additional qualities, such as resistance to stress and mechanical damage, are given to the material by hardening. The essence of the process is rapid heating and the same rapid cooling in a short period of time. Strength increases by 4-5 times. It is used to make watch glass, door leafs, furniture, interior partitions.
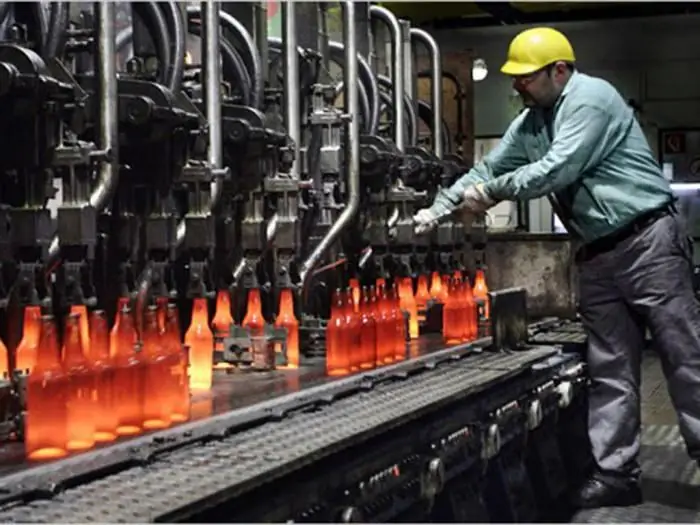
Manufacture of products
Silicate glassware and household items are produced in several main ways:
- Pressing. The viscous mass is poured into a fixed mold, after which certain parameters are set using the movable part of the mold (punch). The mold on the inner surface may have a pattern that is transferred to the outer part of the product during the stamping process.
- Blowing out. Differs in mechanical and manual. The wall thickness of the product varies from 1 mm to 10 mm. Vases, bottles, wine glasses, glasses are made in this way. Hand blowing is an art. Master glassblowers create unique works by combining transparent and colored masses, including metal, natural raw materials, gold and so on in the body of the work. There are no identical hand-blown products.
- Casting. It is mainly used for making figurines, figurines. In industry, by casting, opticalglass.
- Multi-stage articulation. Parts produced by two technologies are used: blowing and pressing. For example, the glass container is blown and the stem is pressed, the finished parts are connected.
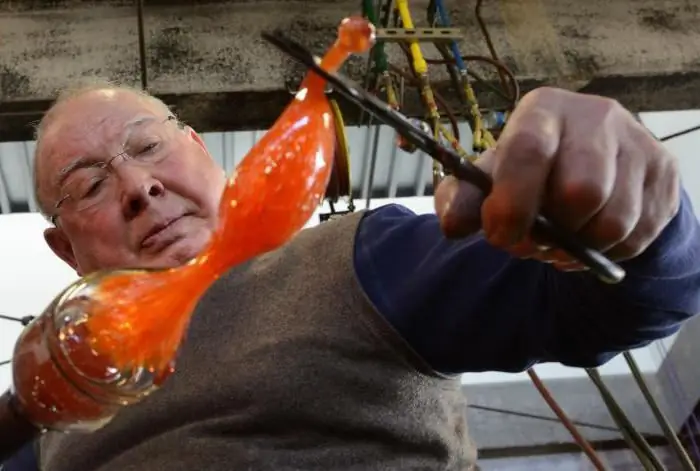
Decorative treatment
Silicate glass is a fertile material for many types of decoration. Distinguish between hot and cold design.
Hot foods include:
- Coloring in bulk with metal oxides.
- Mixing a mass of different colors with further shaping (Venetian glass with stains).
- Crackeling. The mass is molded into a product, cooled sharply, as a result of which surface cracks appear, and the product is melted to fix it.
- Fusing.
- Hot forming of cords, threads with subsequent additive to the product.
- Formation of an additional edge shape during blowing. Achieved by using tools.
Cold decor forms:
- Mechanical: grinding, engraving, diamond cutting, sandblasting.
- Chemical: etching with hydrofluoric acid.
- Applied: painting, decal drawing, silk screen printing, metallization, plasma spraying, painting with luster paints.
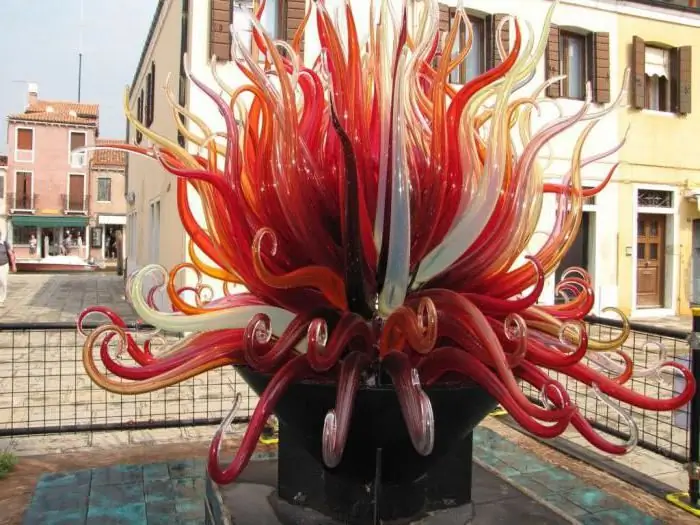
Other types of glass
Modern technologies have made it possible to give silicate glass additional qualities. Of these, the most interesting and sought after are:
Smart glass: the type of material that changestheir properties under the influence of external conditions. For example, under the influence of electric current, the product becomes dull, when the circuit is disconnected, it returns to a transparent state.
Fiberglass (fiberglass): obtained by drawing material into thin (measured in microns) threads. They create a fairly flexible material. Used for the production of fiber optics, insulating materials, etc.
Clarified glass: ordinary silicate glass has a greenish or grayish tint that is clearly visible when viewed through the cut. As a result, the canvas turns out to be slightly colored. To avoid this effect, brighteners are added during the manufacturing process to neutralize unwanted color. It differs from ordinary material in increased light transmission, transfer of colors without color change.
Recommended:
How to make glass? Glass production technology. glass products
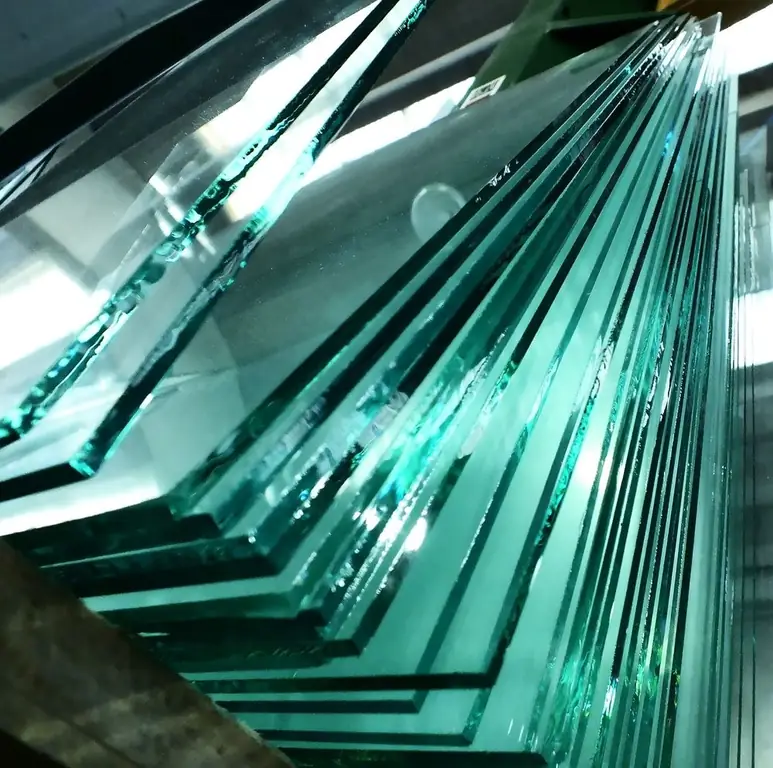
Glass is familiar to everyone. But the process of making it is extremely exciting. Each stage is important and affects the quality of the final product. The basis is sand, soda, lime. The process is almost entirely automated. Surprisingly, glass can even be made at home
Silicate industry - and the house, and the roof, and dishes
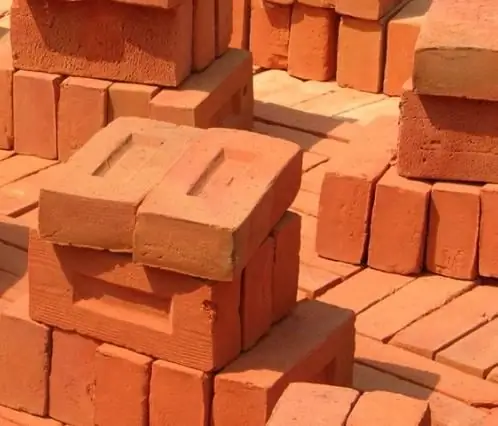
Like mushrooms after the rain, grandiose skyscrapers began to grow in many cities of the world, which are bright design solutions that organically combine concrete and glass. It is the building materials that are so in demand at the present time that the silicate industry produces
Glass sandblasting: glass processing description, equipment, application, photo
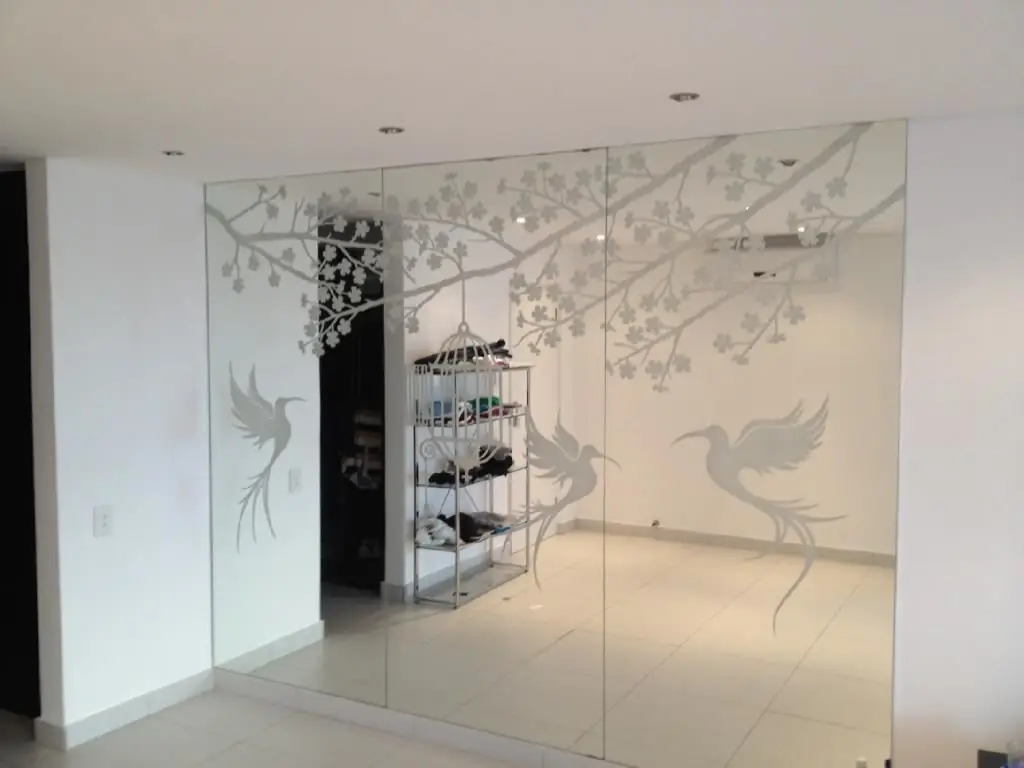
Among the numerous variations of interior decoration, sandblasting of a glass or mirror surface occupies a special place. This technology involves exposing the canvas to sand or other abrasive with a jet of compressed air released under high pressure. As a result, the surface changes and becomes matte, rough, velvety or painted with patterns. In the article we will consider what is sandblasting glass
Potassium silicate and liquid glass - what do they have in common?
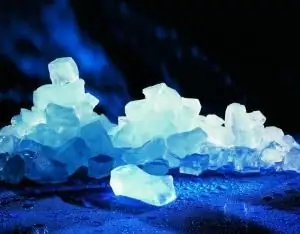
Liquid glass, stationery glue are materials that are well known to us, since they are widely used in everyday life. But most often our information about them is very limited, and meanwhile, learning about soluble potassium silicate, which serves as the basis for their manufacture, is not only interesting, but also useful
Grinding car glass. How to grind glass

The article is devoted to glass grinding. The grinding procedure, its tasks, technique, materials, etc. are considered