2025 Author: Howard Calhoun | [email protected]. Last modified: 2025-01-24 13:10
The use of aluminum as a structural material has been around for a very long time. However, it was distinguished only by its low specific gravity, good ductility and high corrosion resistance. The strength and hardness of this material were extremely low. The problem was partially eliminated by Soviet scientists, who added magnesium to the composition. Thus, AMG alloys were obtained for the first time.
General Description
Today, there are several varieties of this type of alloy. All of them differ from each other in their characteristics and scope. For example, you can consider the properties of the second and third categories, that is, AMg-2 and AMg-3. The composition of the AMG alloy in this case is supplemented with elements such as Si and Mn. Corrosion resistance also remained at a high level, good weldability appeared when using such types of welding as spot, roller, gas. In addition, these two material groups have good cold and hot deformation.
Interval hotdeformation, for example, is in the region from 340 to 430 °C. Cooling after this type of deformation is carried out in the open air. It is also worth adding that AMG alloys of this type are not hardened by heat treatment. Profiles are often made from this material. In their manufacture, two types of annealing are used: low at a temperature of 270-300 ° C and high at a temperature of 360-420 ° C.
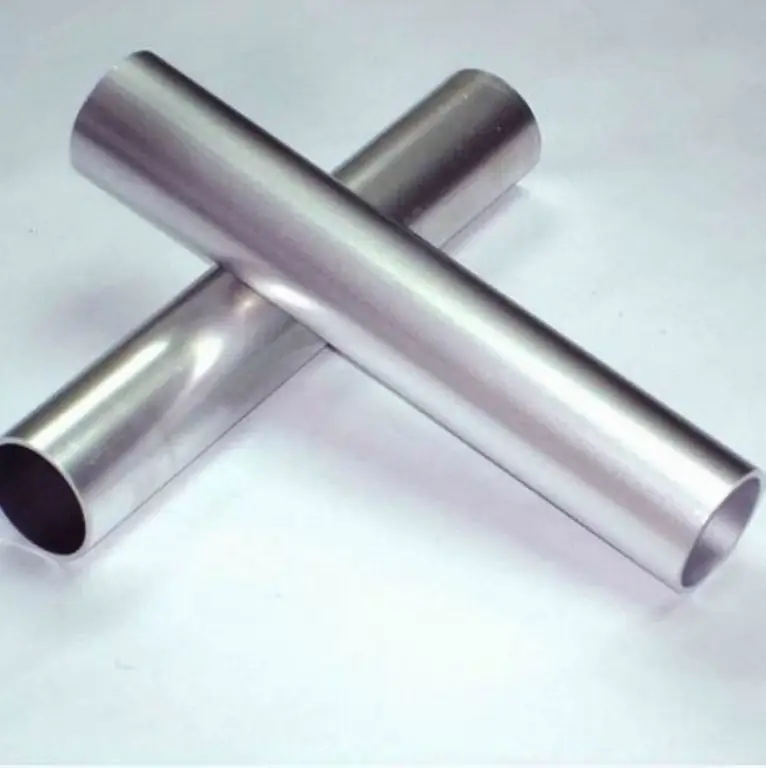
Description of AMG-6
Today, all AMG-alloys belong to the category of deformable substances. It is worth adding that the number of elements that are used for alloying, as well as mechanical properties, are regulated by GOST 4784-97. According to this document, in addition to the AMg alloy - aluminum and manganese, other chemicals are present in the composition.
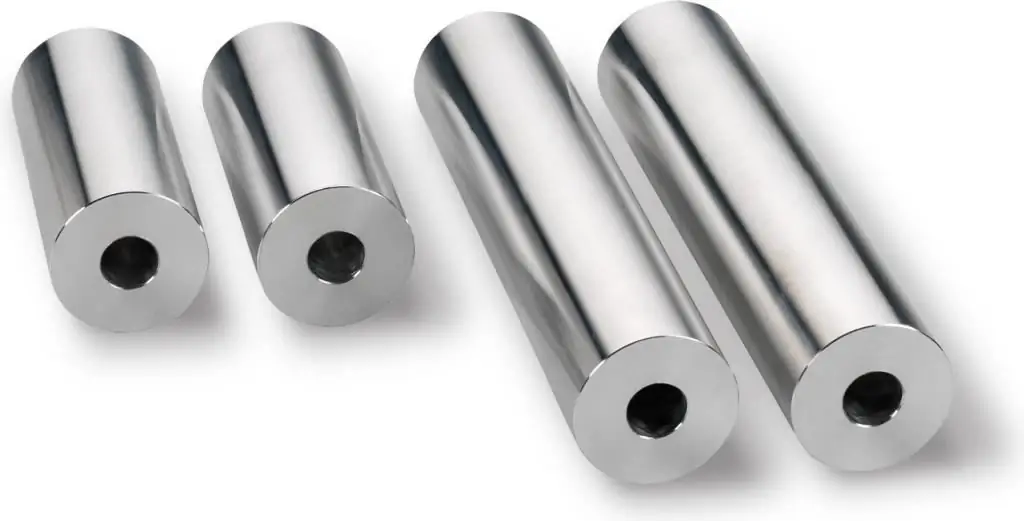
Chemical composition
It is worth considering the chemical composition of AMg-6, as it is considered the best among all similar materials.
- Naturally, the first element in the list is magnesium in an amount from 5.8% to 6.8%. This element is the main hardener of aluminum. If only 1% magnesium of the total mass of aluminum is added to the composition, then an increase in strength by about 35 MPa can be achieved without compromising ductility. However, it should be noted that magnesium reduces the natural resistance to corrosion. This becomes especially noticeable if its amount begins to exceed 6%, and the part made of aluminum alloy AMg-6 is under static load.
- Manganese is also added toamount from 0.5 to 0.8%. This is necessary for grinding the grain size of aluminum, which will positively affect the mechanical properties. In addition, this element significantly reduces the risk of segregation - an uneven distribution of the chemical composition over the aluminum surface.
- Introduced 0.06% titanium to improve processing properties. Most of all, this concerns the weldability of the material. Titanium is able to reduce the structure of the alloy to a finer grain, as well as reduce the tendency to form cracks. All this leads to the fact that the strength of welds in the material of the alloy AMg-6 increases greatly.
- Sodium in the amount of 0.01%. Here it must be said that this element is not added to the composition on purpose, since this is highly undesirable, it appears in it due to the melting of cryolite-containing fluxes. The melting point of sodium is only 96 ° C, which is much lower than that of aluminum itself. Because of this, it can be said that the characteristics of this type of AMG alloy are complemented by increased red brittleness due to sodium.
- Copper in the amount of 0.01%. This substance belongs to the category of harmful impurities for aluminum. The presence of copper significantly reduces the corrosion resistance of this material. In addition, it degrades the ductility of the alloy. However, it is worth adding here that even a small amount of copper significantly increases mechanical performance, that is, strength and hardness.
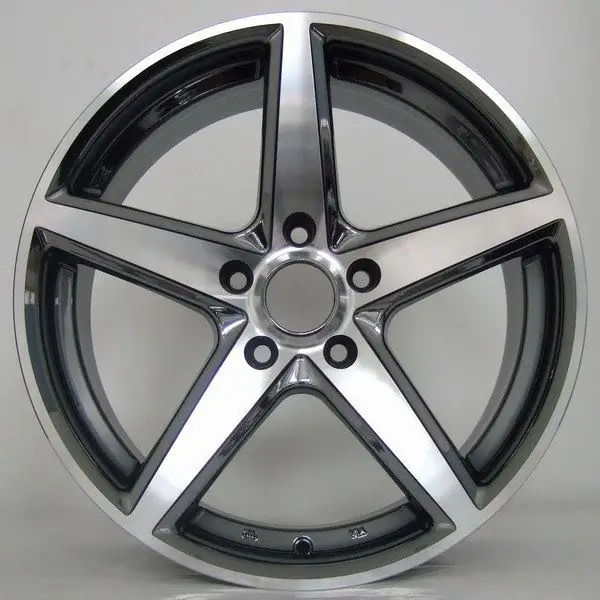
Disadvantages of AMG-6
Despite all the additions, this alloy still has some drawbacks.
- Yield strength of the alloylow enough. In order to somehow avoid or reduce the effect of this drawback, up to 0.8% zinc can be added to the composition or the surface can be hardened.
- Another significant disadvantage is the inability to harden under the influence of heat treatment. All alloys below 8% magnesium cannot be hardened.
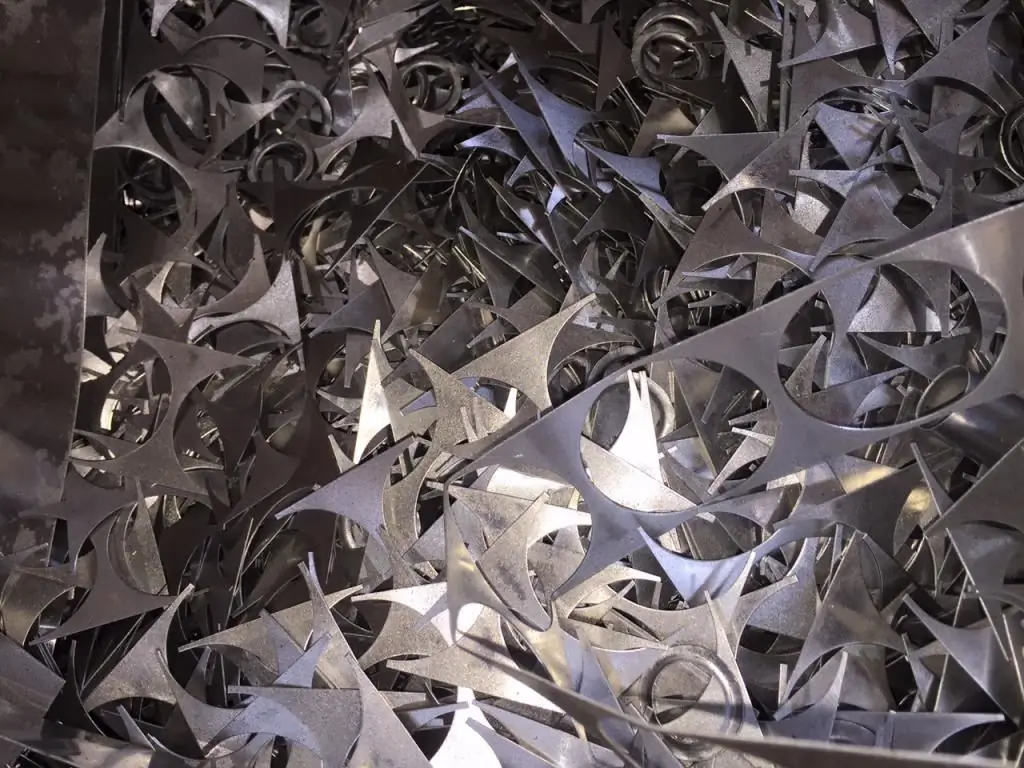
Positive qualities of aluminum alloys
The introduction of various chemical elements has led to the fact that certain characteristics have been significantly improved.
- Mechanical properties have been brought to a satisfactory level. After annealing, the tensile strength is 340 MPa, the same as that of conventional steels. Hardness was also significantly improved. Alloy AMg-6 has the highest index among others.
- Retained a low share. This means that the use of elements from this alloy is still very relevant, especially in those designs where there are strict requirements for the mass of the object.
- Corrosion resistance. If earlier it was high enough, then the alloy becomes completely invulnerable to the effects of atmospheric air, water, as well as a group of weak acids and alkalis. However, to obtain all these qualities, annealing must be carried out and only at a low temperature.
- The vibration resistance of the aluminum-magnesium alloy was quite high and amounted to 130 MPa.
- High technology. This means that the weldability of the alloy belongs to the first category, that is, the density andthe strength of the weld is almost equal to the solid material. In addition, the ductility is very high, and the compressive elongation was 20%.
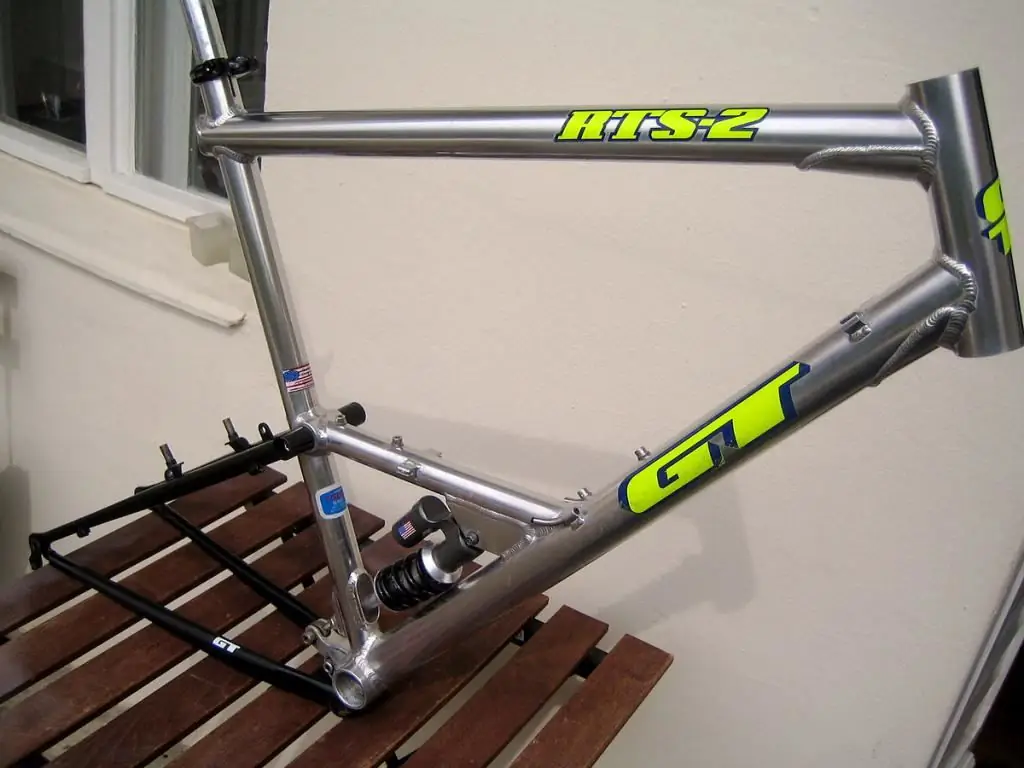
Material application
It was the AMg-6 alloy that became the most common. It is supplied to the building materials market in the form of bars, channels, sheets, corners with a variety of dimensions. These parts are most widely used when it is necessary to create a welded structure with a limitation on the mass of the object. This material can also be successfully used to produce both internal and external skins for a wide variety of motor vehicles. In addition, tanks can be made from it, which are suitable for transporting oil, for example.
Recommended:
Steel 09G2S - properties and characteristics
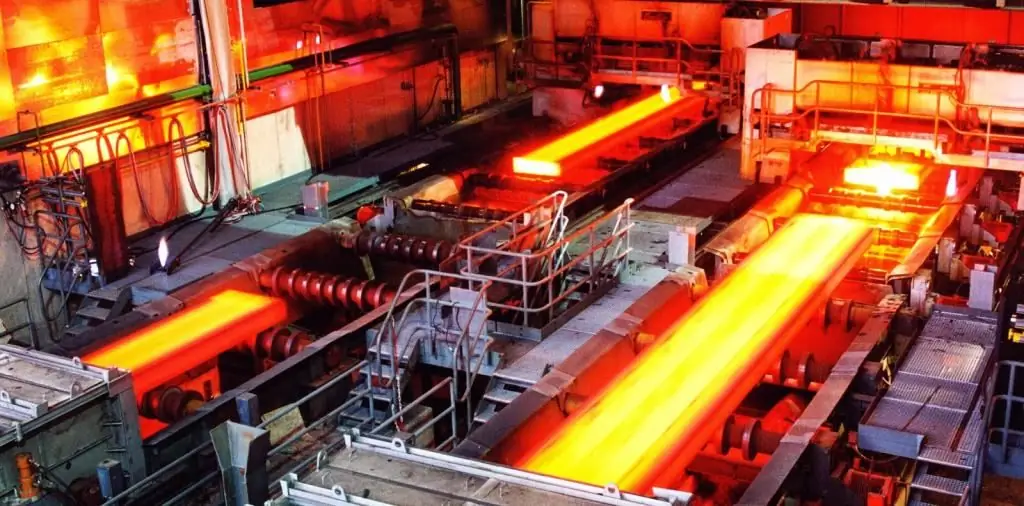
Diversity in the steel industry is often intimidating for people who need to purchase a particular grade of steel for a specific need. This problem is solved by a long and methodical study of the topic, understanding its very essence. However, there is a way to cut a little. This article contains all the most important and useful information regarding steel 09G2S. Reading this article will not take much time, and the knowledge gained will help you choose the right material
Steel 20: GOST, characteristics, properties and applications
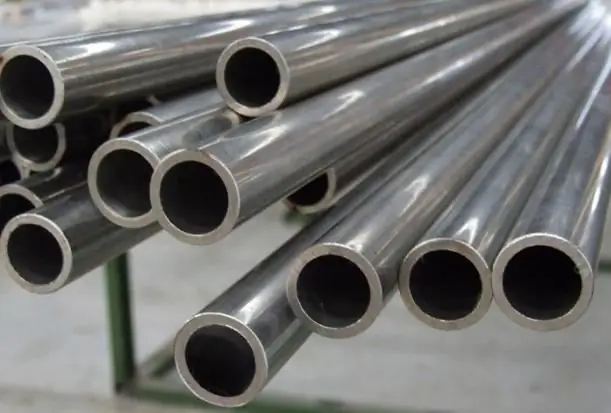
Structural steel is the most demanded in the gas and oil industry, housing and communal services, at the household level. Versatile features, low cost and proven reliability and practicality are of great interest to manufacturers
Green marble: characteristics of properties and application
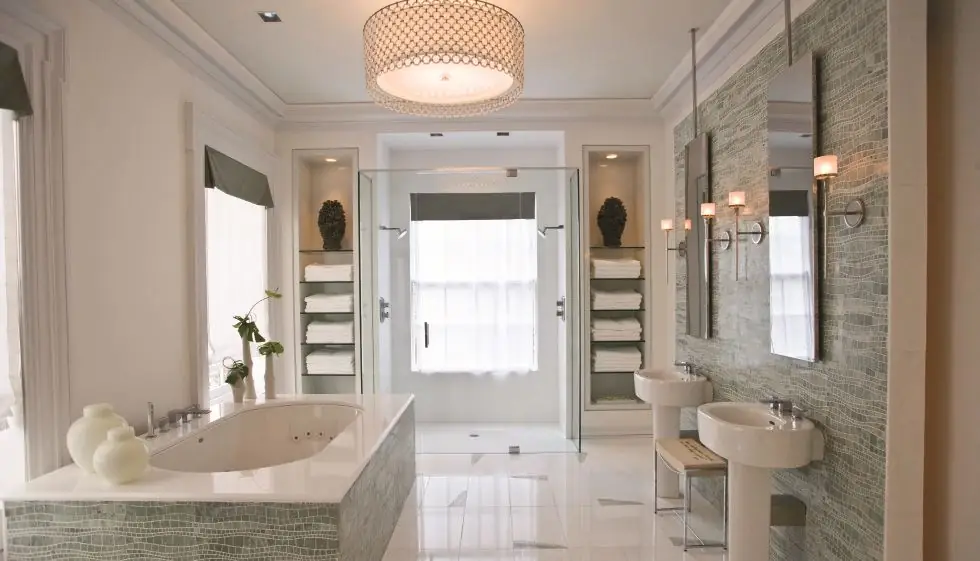
Today, green marble is widely used in construction and decoration. They veneer buildings, walls and floors of premises, create mosaic compositions and decorative ornaments, make tabletops and window sills, flowerpots. When decorating parks and gardens, fountains, gazebos, and stair railings are covered with such marble. It is used to create monuments, tombstones, monuments
Marking of bronze: characteristics, properties and scope
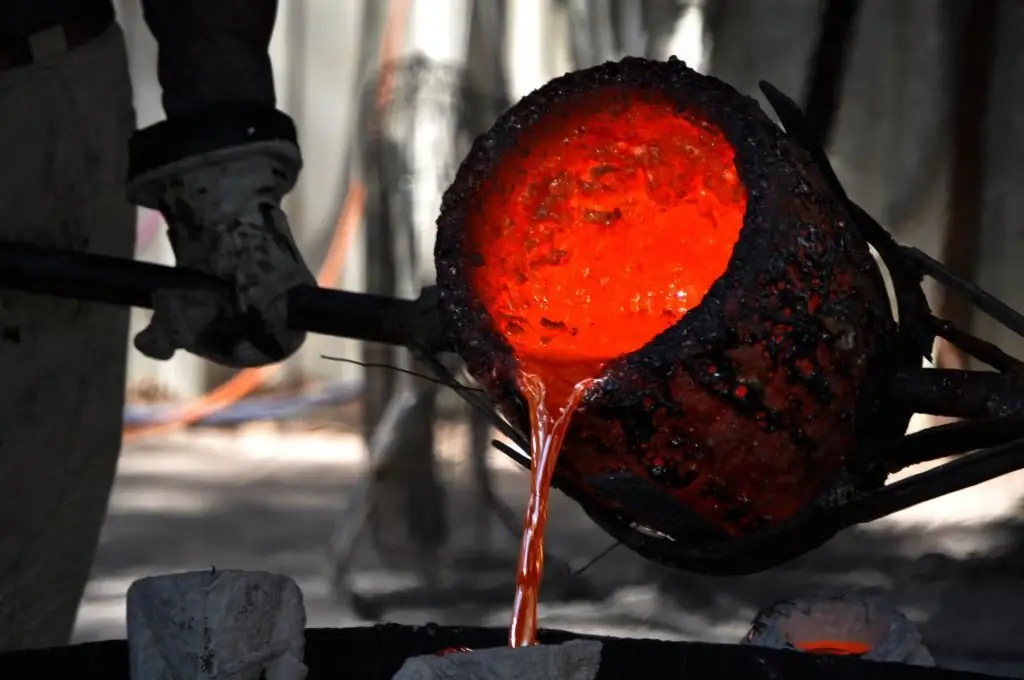
Due to its decorative features and many other properties, bronze has become popular. It is very difficult even for connoisseurs to name all the impurities and additives that are present in bronze alloys. This article will focus on bronze and its marking
Two-component polyurethane sealant: definition, creation, types and types, characteristics, properties and nuances of application
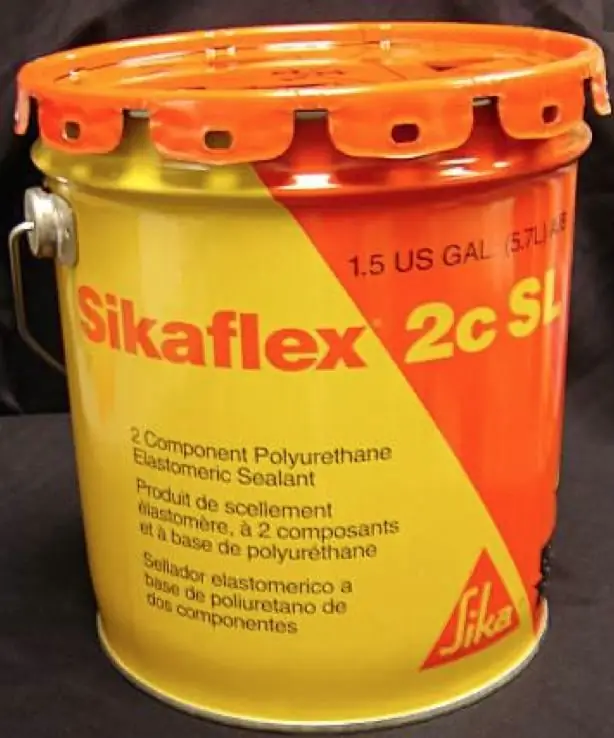
With long-term and high-quality sealing of seams and cracks, polyurethane two-component sealants have found their wide distribution. They have high deformation and elastic properties, therefore, they can be used as butt sealants in the field of repair and housing construction