2025 Author: Howard Calhoun | [email protected]. Last modified: 2025-01-24 13:10
Deciphering CNC (abbreviations) literally means numerical control. In a broader sense, abbreviation refers to a complex set of machine control with an automatic cycle of cutting parts. Highly skilled workers are required to maintain such systems.
What does the concept include?
CNC decoding is now known to you. This equipment includes several parts:
- electric - these are control and automation systems;
- mechanical - these are pneumatic and hydraulic systems;
- external design is design and usability.
CNC is gradually replacing manual methods.
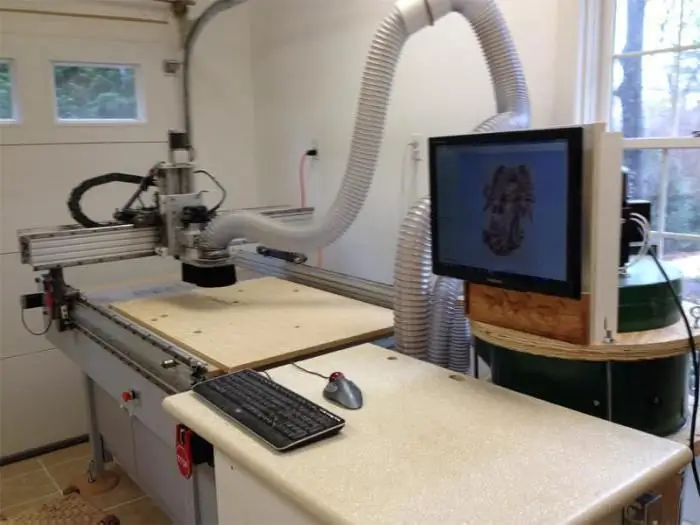
There are still enterprises in the country where CNC decoding is required for every employee. However, progress is also moving deeper. Program-controlled machines are being introduced into production even to perform the simplest operations.
CNC machines are profitable in those industries where there is a mass production of the same type of products. These systems are chosen by customers to perform high-precision manipulations that a person can handle.with great difficulty.
The principle of operation of equipment with program control
CNC decoding includes two parts:
- Numerical control. All operations are based on machine code counts. The state of the axes is monitored by removing code pulses.
- Program control involves the conversion of given commands into machine-readable code through applications. The human-machine interface is presented in a visual form.
For one type of parts, the program is compiled only once and stored on external media or in built-in storage, if memory allows. If necessary, the machine code is transferred to RAM, and the automatic cycle starts again. CNC systems are good on any equipment with multiple coordinate axes.
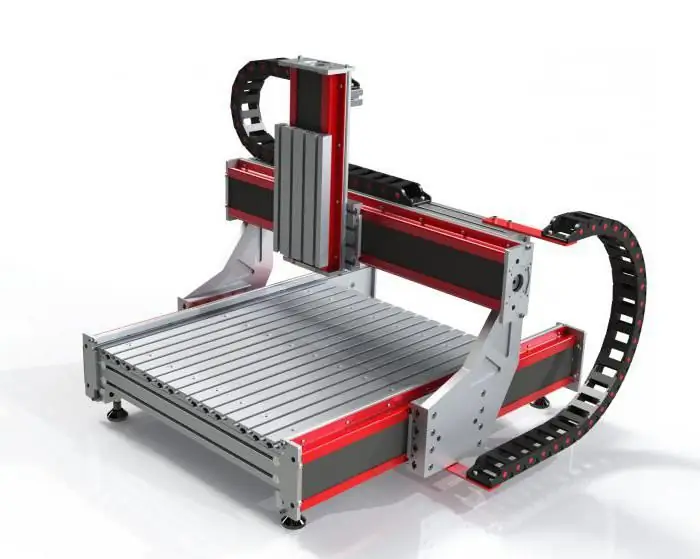
There is an ideal solution for every production. It is important to take into account all the basic requirements for equipment. We list just a few of them: the load on the tool, the intensity and speed of processing, the number of axes and the possibility of upgrading the machine in the future.
Furniture manufacturing
Where we are talking about the production of wooden products from MDF boards, a CNC milling machine is suitable. For the consumer, the quality of the product has become important, which can only be achieved with the help of machine processing with a high number of products. The smoothness and accuracy of the resulting patterns are amazing, and at the same time, machine processing makes the furniture more accessible.
The simplest operations were previously created usingrelay logic. But volumetric images are available only to owners of CNC systems. The processing speed can be doubled due to the use of double-sided turning, when several technological operations are performed simultaneously. The leaders in the production of controllers that can cope with such tasks are electronics manufacturers:
- "Fanuc";
- Siemens;
- "Heindenhain":
- "Aries".
To implement the simplest machine is obtained on the basis of a conventional desktop computer. But for the movement of the axes, a control board is still required. The cost of such solutions is low compared to the profits brought by factory automation.
The principle of working with multi-axis systems
The CNC router must receive a specific command to perform any action. Most control programs are written in so-called G-codes. These are standard simple movements hardwired into the controller's memory.
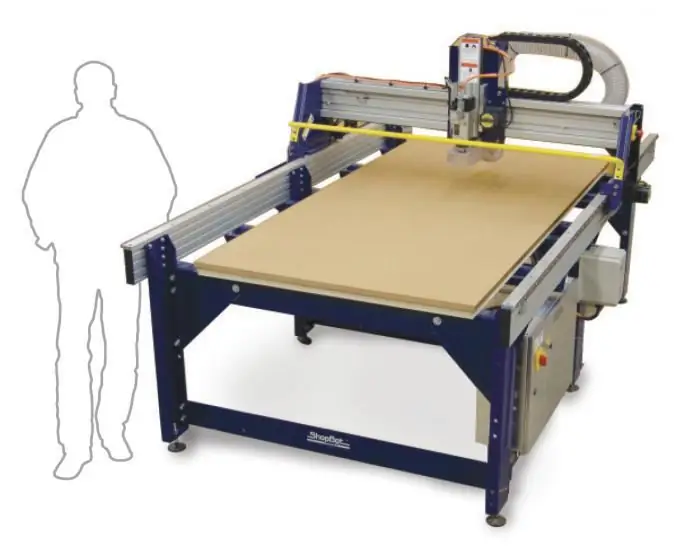
In simple terms, to control the machine, the operator selects the direction, the final path, the speed of the tool, as well as the speed of the spindle assembly. For the production of most parts, this is enough. But in addition to commands, it is required to enter the parameters of tool wear, the offset of the starting point of processing, the type of cutter, the travel errors of the screw pair.
The sequence of control actions is strictly regulated by machine tool manufacturers. Each manufacturer lays down his own characteristics in the operation of the machine, with whichyou will have to familiarize yourself before performing even the simplest cut.
Equipment sequence
The general principle of operation of machine tools with numerical control is the same. Remembering all the steps is not difficult, and once you learn how to start the automatic cycle, you can easily manage the rest of the machines. To understand human commands, a machine must read bit data. Standard applications for machine tools are used to translate into a view understandable to the controller.
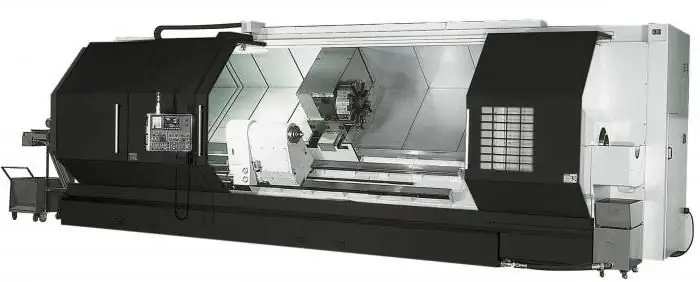
The finished model, created according to certain rules, is loaded into a PC and converted into zeros and ones. Further, the received commands are tested on the machine without movement of the axes. If everything goes well, debugging with the part begins. The corrected data depends on the type of material being processed, the complexity of the contours being performed, the condition of the tool.
Recommended:
Ion implantation: concept, principle of operation, methods, purpose and application
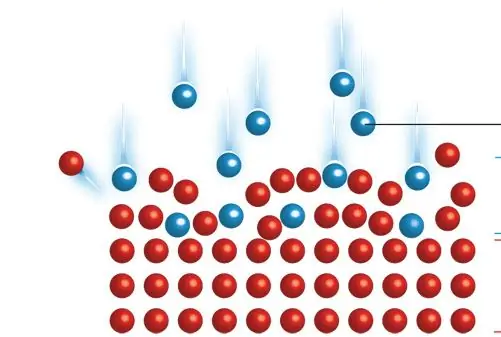
Ion implantation is a low-temperature process by which the components of a single element are accelerated into the solid surface of a wafer, thereby changing its physical, chemical or electrical properties. This method is used in the production of semiconductor devices and in metal finishing, as well as in materials science research
Classification of engines. Types of engines, their purpose, device and principle of operation
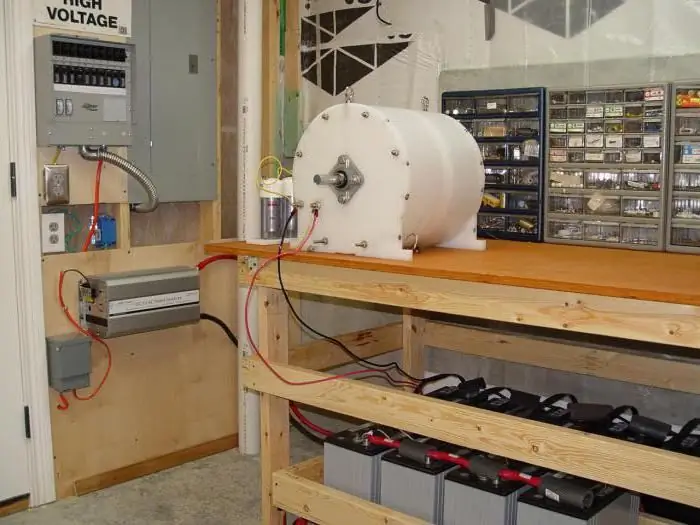
Nowadays, most vehicles are powered by an engine. The classification of this device is huge and includes a large number of different types of engines
Thermal imaging control of electrical equipment: concept, principle of operation, types and classification of thermal imagers, features of application and verification
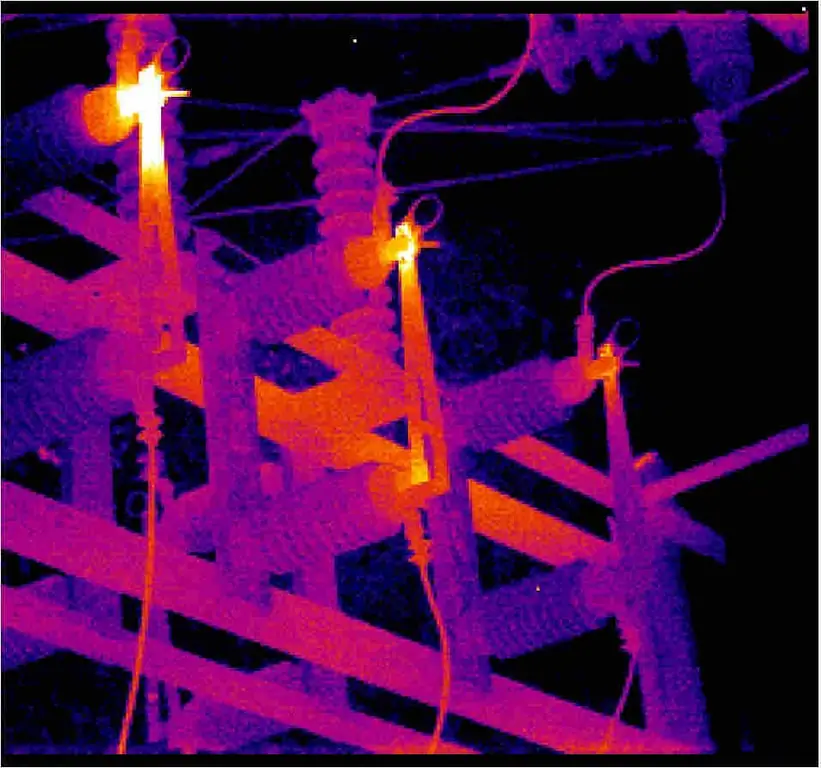
Thermal imaging control of electrical equipment is an effective way to identify defects in power equipment that are detected without shutting down the electrical installation. In places of poor contact, the temperature rises, which is the basis of the methodology
Electric locomotive 2ES6: history of creation, description with photo, main characteristics, principle of operation, features of operation and repair
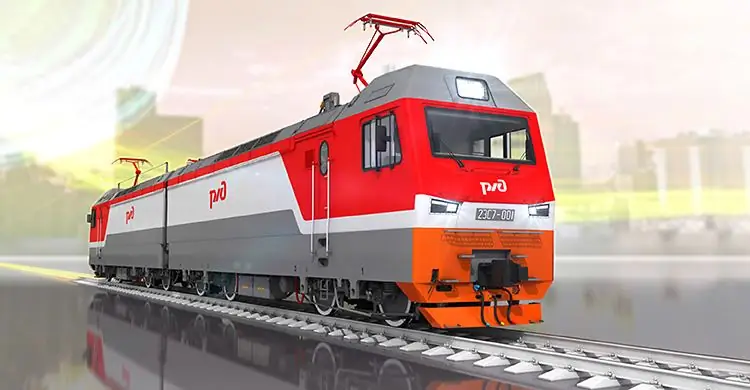
Today, communication between different cities, passenger transportation, delivery of goods is carried out in a variety of ways. One of these ways was the railroad. Electric locomotive 2ES6 is one of the types of transport that is currently actively used
Gas piston power plant: the principle of operation. Operation and maintenance of gas piston power plants
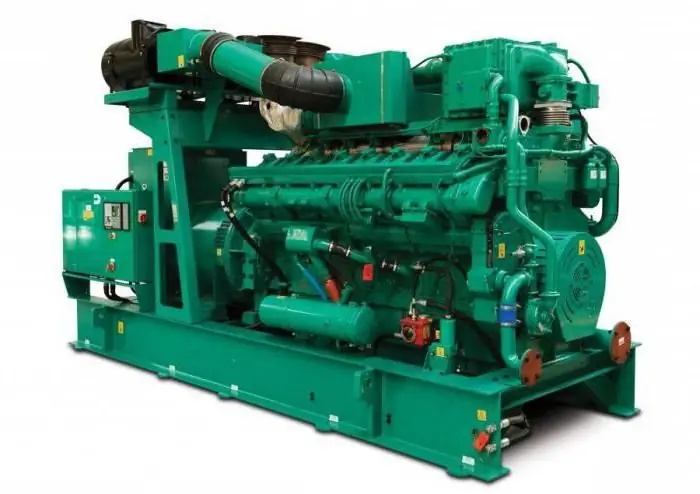
Gas piston power plant is used as a main or backup source of energy. The device requires access to any type of combustible gas to operate. Many GPES models can additionally generate heat for heating and cold for ventilation systems, warehouses, industrial facilities