2025 Author: Howard Calhoun | [email protected]. Last modified: 2025-01-24 13:10
For several hundred years, the Russian Federation has been among the world leaders in the production of pig iron. This alloy is used in a variety of industries, is used to create artistic and decorative products. Experts say: cast iron is an integral part of human life, it is deservedly considered one of the most sought-after materials. Today we propose to talk about ferrous metallurgy, the production of iron and steel, their impact on humans. Let's turn to the chronicle of the development of the foundry business in general: historical facts and interesting information are waiting for you!
History: Copper Age
Cast iron is a metal with thousands of years of history, its roots go back to BC. In general, historians date the first evidence of the emergence of metallurgy to the 6th-5th millennium BC. Then a person still used stone to create tools, but he already came across copper nuggets. Taking nuggets for ordinary stones and processing them in the same way that was applied to any stones - just hitting each other - a person understood: these stones do not break off, but only deform, and therefore theycan be molded into almost any shape. Historians would later call this method cold forging. So copper became a substitute for stone, it became much easier to make fishhooks, spearheads and daggers, moreover, the quality of such products significantly exceeded the quality of analogues made of stone and bone. At the same time, wood processing was improved, it became possible to produce small parts. By the way, scientists have proved that in those territories where copper was actively used, the appearance of the wheel happened much earlier. This proves the fact that the development of mankind is inextricably and closely linked with the development of metallurgy.
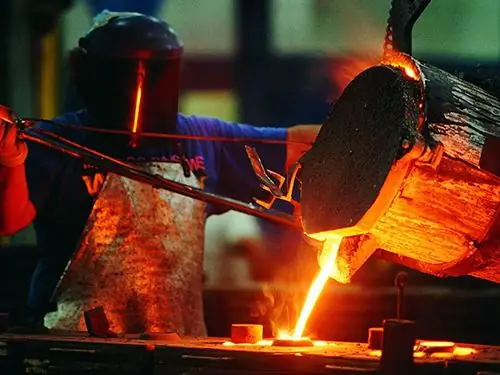
Bronze Age
When people learned how to create bronze - an alloy consisting of copper and tin, humanity entered the Bronze Age. Today, historians cannot answer the question of how exactly a person invented such an alloy. Most researchers believe that this happened by pure chance, when tin got into a container with molten copper. The fact remains that for a thousand years people fought with bronze swords and cooked in bronze pots.
Iron Age
Historians say: it was much easier to get iron than copper or tin. The thing is that it is found in the form of oxide and oxide everywhere. So why didn't people start using iron sooner? The answer is simple: the production of this metal is an incredibly complex and time-consuming process, taking place in several stages. It took more than one century of development to study this process. That's whyit is not surprising that the metallurgists of those times were considered by the people to be real sorcerers, burning magical things.
First mention of cast iron
The country in which iron production began is today considered China. Historians say that this happened around the fifth century BC. In the Celestial Empire, coins, household utensils and various weapons made from cast iron were extremely popular. Many cast-iron castings have survived to our times, for example, a magnificent cast-iron lion, which is 6 meters high and 5 meters long. Scientists have proven that this statue was cast in one time, which undoubtedly testifies to the great skill of the first Chinese metallurgists.
Interesting fact: around the world, the beginning of the production of ductile iron is considered to be the 19th century AD, although it is reliably known that in China swords were made from it even before the birth of Christ!
The origin of production in Russia
When did iron production start in Russia? Archaeological excavations carried out on the territory of large cities of the Golden Horde prove that the emergence and development of this production in Russia began back in the days of the Tatar-Mongol yoke! The proximity of the Mongol kingdom to China played a certain role in this.
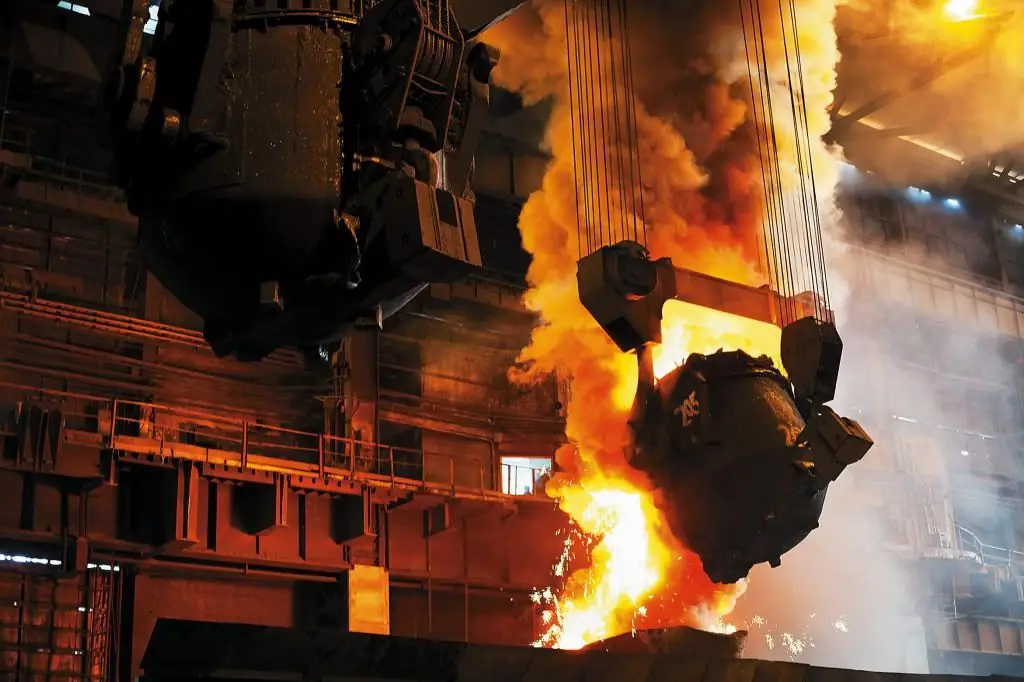
Practically in all the Tatar-Mongolian cities lived Rusichi, who had their own workshops and trading stalls here. They not only adopted the knowledge of local masters, but also shared their own. After the Horde fell, technology continued to develop and improve. Already inIn the 16th century, under Vasily the Third and Ivan the Terrible, the production of foundry iron began to be actively used in artillery, mainly cannonballs and small cannons were made from it. At the same time, historians say, cast iron was also used in the casting of bells. The main production took place in cities such as Moscow and Tula. It is worth noting that until the 17th century, Europe did not know such technologies, and therefore Russian factories could actively export various tools and cores made of cast iron to European countries.
Active development
During the time of the Petrine era, the active development of the production of iron and steel began. The tsar understood that an increase in metallurgical capacities would lead Russia to development. To implement incredible plans, Peter I had everything necessary: both materials and production technologies. It was under this king that active construction of factories began in Siberia, in the Urals. During the entire reign of Peter the Great, the production of iron and steel was increased by 770 times, 16 large metallurgical plants appeared in Russia. Development continued after the death of the emperor, at the end of the 18th century there were more than a hundred factories on the territory of the Russian Empire, the country became a world leader in this field. Along with the development of the industry, the metal application industries also developed. Now not only weapons were made of cast iron, but also dishes, monuments, gates and fences.
It is worth noting that domestic blast furnaces used for iron production were recognized as the best in the world. They were characterized by the highest productivity even at minimal cost. In XIXcentury, foundries were separated from blast furnaces, which made it possible not only to specialize the process, but also to mechanize it. It was during this period that pipe foundries and workshops producing malleable iron castings appeared.
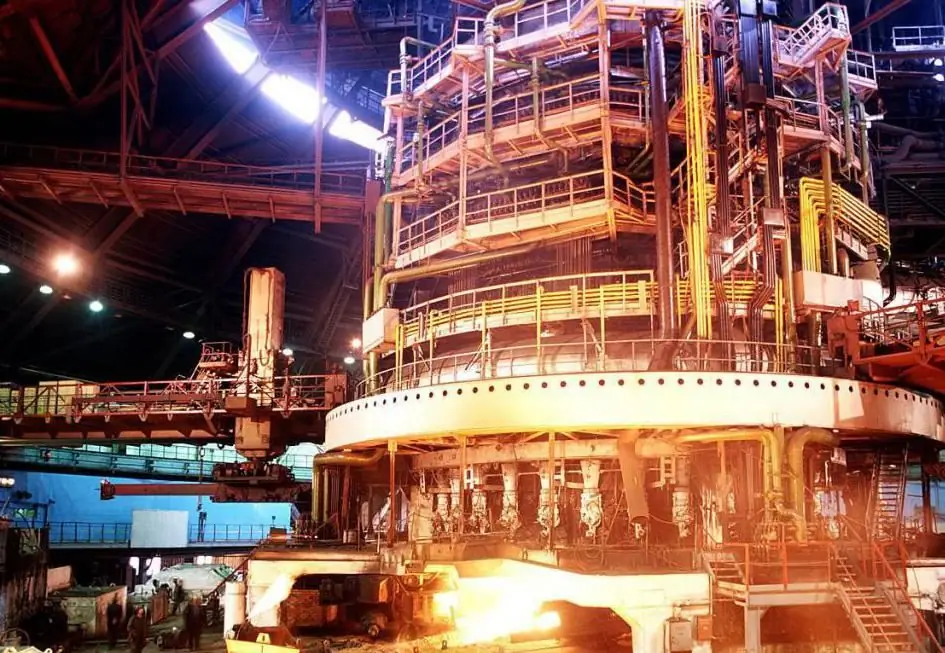
Russia is the world leader
In the 20th century, Russia did not slow down and remained the leader in iron casting. In the USSR, the volume of cast iron accounted for about 75% of the total amount of metal casting. It was the number one raw material, its main consumers were the defense industry and agriculture. It was from cast iron that specialists made parts and various units for equipment. It should be noted that even today Russia retains a leading position in terms of production and use of cast iron. It is used to make not only large-sized products, but also such delicate work as gate elements, jewelry, furnace casting and souvenirs!
Iron production: necessary equipment
Let's start with a definition. Cast iron is usually called an alloy of iron with carbon, and carbon here should be at least 2%. So how does the iron production process work? First of all, this requires a huge blast furnace. Its dimensions are amazing: the height of such a furnace is 30 m, and the inner diameter is 12 m. The widest part of the furnace is called steaming, the lower one, through which hot air enters the furnace, is a hearth, the upper one is a shaft. By the way, on the upper part there is a special hole - a top, which is closed with a special shutter. The principle of operation of a blast furnace is countercurrent: from below into itair is supplied, and materials are supplied from above. Materials needed to make iron include flux (no slag can form without it), coke (necessary for heating water, melting it and reducing it) and ore (which is actually the main raw material).
For production you will also need:
- carts;
- transporters;
- bunkers;
- special faucet, etc.
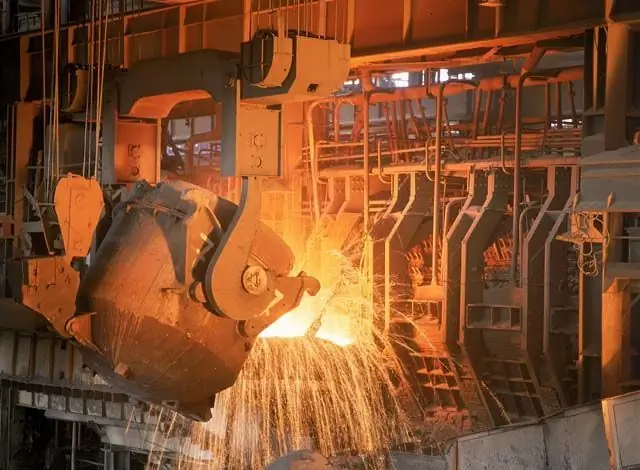
Raw materials
Introduction to alloys, the production of iron and steel begins at school - this topic is provided for in the work program in chemistry. The textbooks discuss the composition of iron ore: it is the ore substance itself, that is, iron carbonates, silicates and oxides, and waste rock, consisting of dolomite, sandstone, limestone and quartzite. It should be noted that different ore may contain different amounts of ore substance. It is by this criterion that ore is divided into poor and rich. The first is sent for enrichment, and the second can be immediately used in production.
In order to produce a ton of pig iron, you will need: three tons of ore, a ton of coke, twenty tons of water. The amount of flux depends on the type of ore.
Types of iron ores
Before we move on to get acquainted with the process of iron production, we offer information about the types of iron ores. It could be:
- Brown iron ore. It is characterized by the content of 25-50% iron in the form of so-called aqueous oxides. Waste rock is clayey.
- Hematite(it is also called red iron ore). This is an anhydrous oxide, the content of harmful impurities is minimal here. Iron here is about 45-55%.
- Magnetic iron ore. The iron content here is about 30-37%. The waste rock is a silica mass.
- Siderite (its second name is spar iron ore) is extremely easily oxidized, turning into brown limestone.
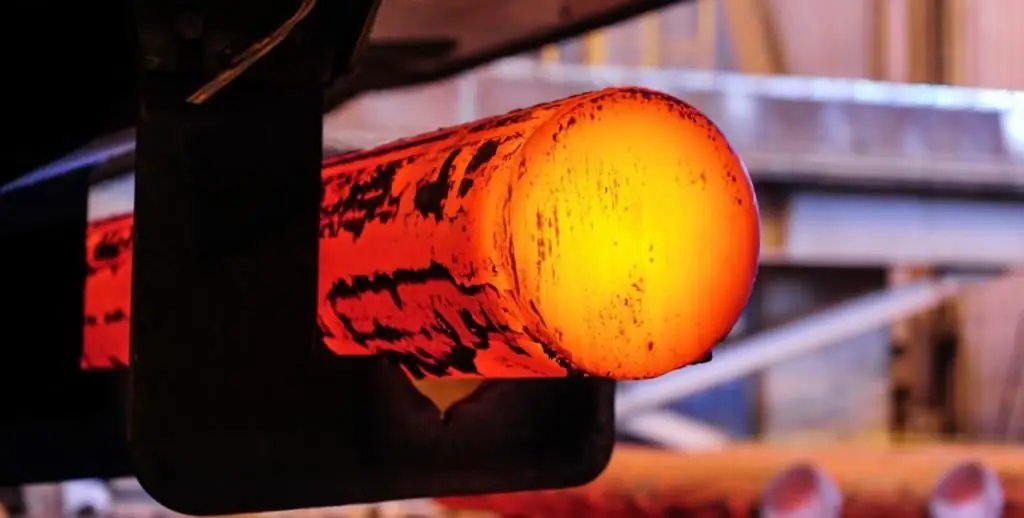
Production technology
The technology of iron production consists of several stages. It all starts with the preparation of the ore: it is sorted by chemical composition and, of course, by size. Large raw materials are crushed, and small particles or ore dust are agglomerated. At the same stage, the beneficiation of poor ores also takes place. In addition, during the preparation process, a significant part of the waste rock is removed, respectively, the iron content increases. The next stage of iron production technology is fuel preparation. It all starts with coke. During this stage, the coke is screened - all unnecessary fines are removed from it, which can lead to fuel loss. The next stage of blast-furnace iron production is the preparation of fluxes. Pluses are crushed, a trifle is sifted out of it. After this procedure, all materials are loaded into the furnace. Then the blast-furnace production of pig iron begins directly: the furnace is filled with coke, an agglomerator is added (this is the name of ore sintered with flux), and coke is added again.
The temperature required for smelting is maintained by blowing in heated air. In the combustion processcoke in the hearth produces carbon dioxide. CO2 passes through coke to become CO. Further, carbon monoxide restores the main part of the ore. In this process, the iron becomes solid, passing into that part of the furnace, the air in which is very hot. Here the iron dissolves the carbon within itself. Actually, this is how iron production in a blast furnace looks like. Liquid iron from the furnace falls into special ladles, from which it is poured into pre-prepared molds. It is possible to pour into special collections-mixers, in which the alloy will remain in liquid form for some time. Simultaneously with blast-furnace pig iron production, silicon, manganese and a number of other impurities are being reduced.
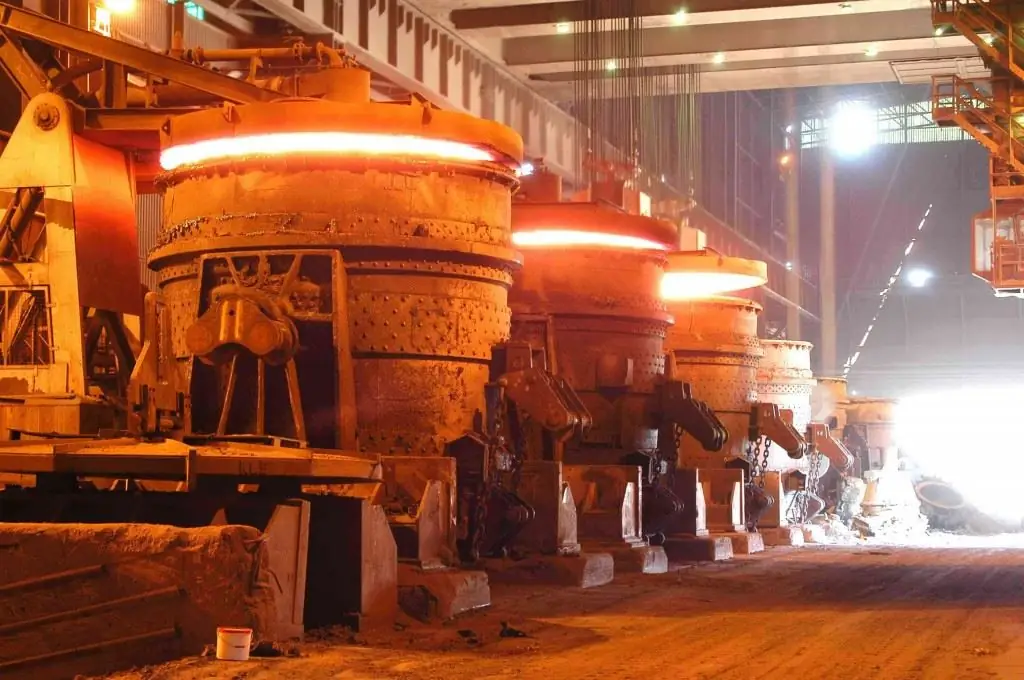
Types of cast iron
There are only two types of cast iron: white and gray. The difference between them lies in the chemical composition and the heat treatment process. Thus, white cast irons are the result of very rapid cooling, while gray cast irons are obtained as a result of slow cooling. Whites are characterized by such qualities as fragility and hardness. They are extremely difficult to cut; in the process, pieces break off from them. Therefore, white cast irons are used only as blanks for the production of other grades of cast iron. For example, as a result of firing this type, malleable cast irons are obtained. Please note: the name malleable has nothing to do with the forging process. According to historians, it appeared due to the fact that horseshoes were previously made from cast iron with such characteristics. This type is widely used inagricultural engineering and the automotive industry. The main difference between gray cast irons is ductility combined with high strength. This allows them to be used in areas such as machine tools, agriculture and the automotive industry, and domestic use.
By the way, there are so-called half cast irons. They have intermediate properties of white and gray species. In addition, by adjusting the intensity of cooling of this alloy, it is possible to obtain a variety of castings that will differ in strength, ductility and other properties. Cast irons with special properties include:
- anti-friction, used for the manufacture of bushings, shafts, bearings;
- wear-resistant, necessary for the creation of pumping equipment, various parts for the nitrogen industry, furnace casting;
- heat-resistant, which are used in the manufacture of furnace castings, pipe systems and gas turbine engines;
- heat resistant, suitable for kiln fittings and boiler parts;
- corrosion resistant, indispensable for the manufacture of various parts in the chemical and aviation industries, which are used in aggressive environments.
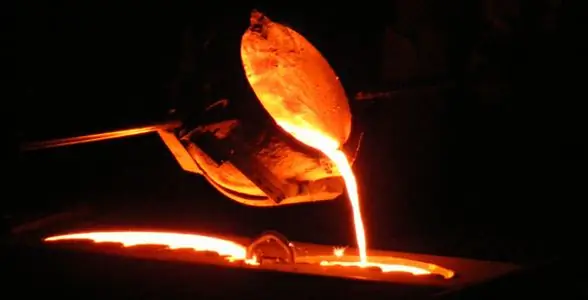
Characteristics of cast iron
The quality cast iron is characterized by the following qualities:
- excellent heat capacity;
- good corrosion resistance;
- increased heat resistance.
These and other characteristics allow the use of cast iron ineveryday life, and in heavy industry. Russian-made cast iron cookware is especially popular. Not only frying pans and pots are made from this material, there are fondue, braziers, baking dishes, stewpans and grills.
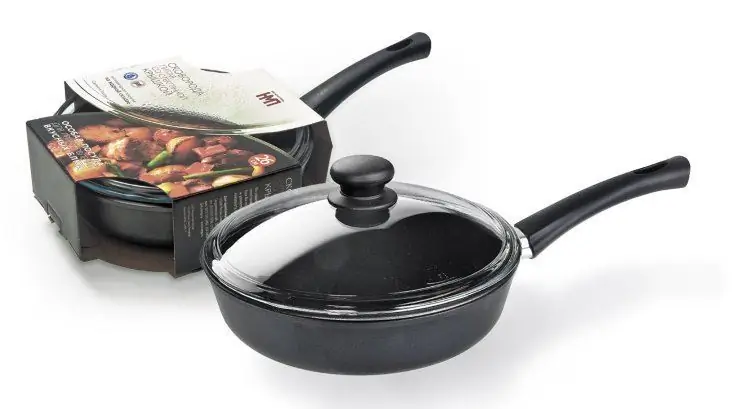
It is worth noting that dishes made of this material are equally well suited for frying pancakes, cooking stews, cereals, and for stewing pilaf. The fact is that cast iron heats up rather slowly, but it perfectly accumulates heat and distributes it evenly. Experts say: different companies are engaged in the production of cast iron cookware. All of them produce products of approximately the same quality. Of all this diversity, the products of the St. Petersburg plant "Neva" stand out. It is this plant that is one of the largest manufacturers of cast iron cookware in the Russian Federation.
Recommended:
Production technologies: concept description, development, development, functions
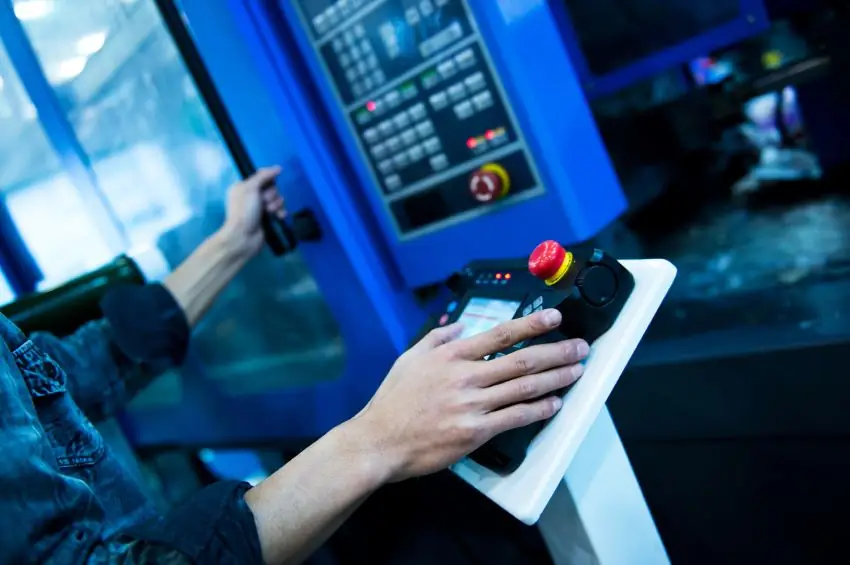
Under the term "production technologies" there are different interpretations. Often this concept is associated with a heavy production process, industry. But in fact, technology is primarily a skill, skill, methods. If we translate the word "technos" from the Greek language, additional options for interpreting this concept will open up: art and logic. Consequently, production technology is a set of methods, techniques and methods for creating a product, product
Real estate development and its role in economic development. The concept, types, principles and foundations of development
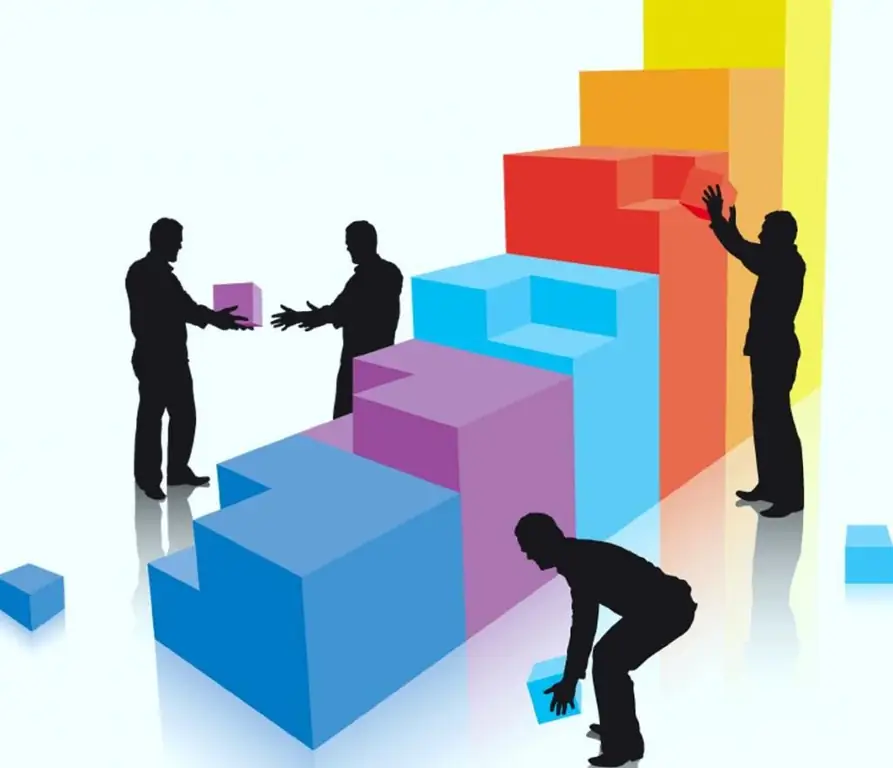
In the framework of this article, we will consider the organization of the real estate development system and its role in economic development. The basic concepts, types and principles of organization of the development system are considered. The characteristic features of the system in Russian conditions are considered
Gas production. Gas production methods. Gas production in Russia
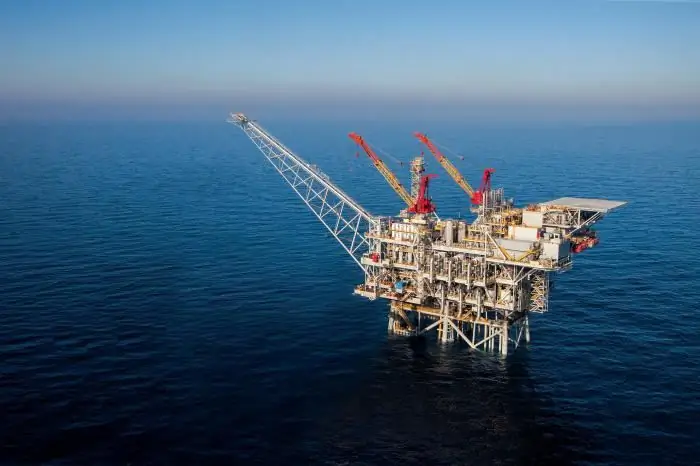
Natural gas is formed by mixing various gases in the earth's crust. In most cases, the depth of occurrence ranges from several hundred meters to a couple of kilometers. It is worth noting that gas can form at high temperatures and pressures. In this case, there is no access of oxygen to the place. To date, gas production has been implemented in several ways, each of which we will consider in this article. But let's talk about everything in order
Pig iron: specifications
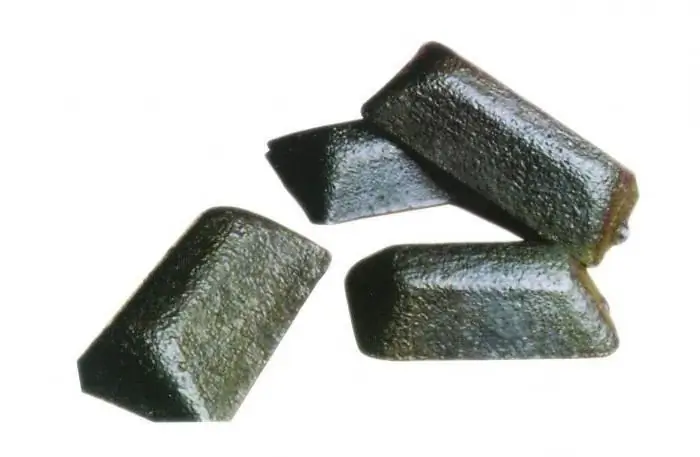
Currently, the industry uses a wide variety of products, processing which, you can get high-quality material. However, some of the substances are obtained through several processings. Pig iron is one example of an intermediate raw material
Pig anatomy. Similarities between human and pig DNA
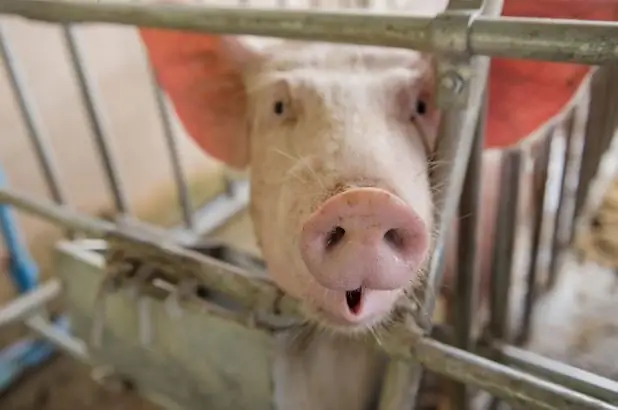
Pig anatomy has been studied quite well by scientists. Animals are hardy and unpretentious. Both the cardiovascular and nervous, reproductive and other systems are well developed in piglets