2025 Author: Howard Calhoun | [email protected]. Last modified: 2025-01-24 13:10
In order to proceed to the consideration of pig iron, it is necessary to understand the general composition of this product and its qualities. So, cast iron is called an alloy, which consists of a material such as iron, carbon and several other impurities.
General description of cast iron
Depending on the impurities used to melt cast iron, its properties also change. However, there are some features that should be supported in any case. One of them is the mass fraction of carbon in the composition. This parameter must be at least 2.14%. If the carbon content is lower, then it is no longer cast iron, but steel. It is important to understand here that, as such, ordinary cast iron is not produced. In the process of obtaining this material, two types of additives are always added at the end of the operation, according to which the separation into foundry or pig iron takes place. One of the features of this raw material also lies in the fact that the temperature required for its melting is 250-300 degrees higher than for steel. To melt this substance, a temperature of 1200 °C is required.
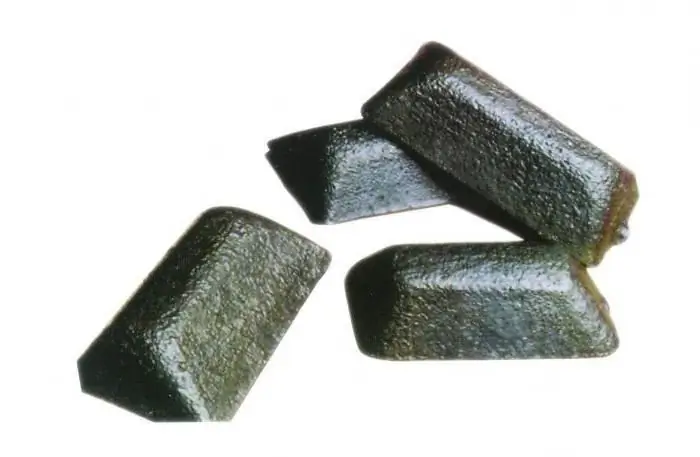
How to receivecast iron?
Here it is immediately worth noting that the production of pig iron or ordinary - these are almost identical processes, and therefore it makes no sense to describe both. Consider only the general technology of melting.
So, to get this substance, you need to spend a lot of resources. The main working raw materials are coke and water. In order to be able to smelt a ton of pig iron, you need to take about 550 kg of coke or about 900 liters of water. It is impossible to determine exactly the amount of ore that will be spent on processing for each batch, since its consumption depends entirely on the percentage of iron. However, it is unprofitable to use absolutely any ore, if you look from the point of view of the economy. For this reason, raw materials are used that contain from 70% iron in their composition and more. It is also important to note that before smelting, the ore is enriched, and only after it enters the blast furnace, it is in them that the process of producing iron takes place. Electric furnaces smelt only 2% of the total amount of material.
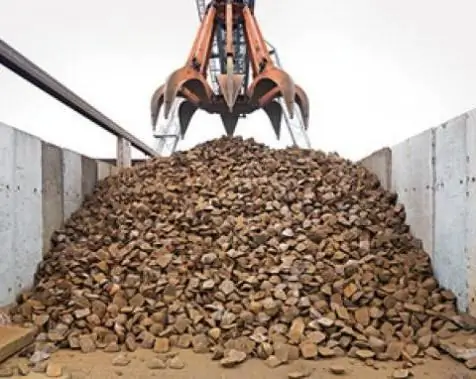
First stage
The whole smelting process is divided into several interconnected stages.
The procedure begins with the fact that ore is loaded into the furnace of the furnace, which contains magnetic iron ore. In addition, an ore containing hydrous iron oxide or a s alt thereof can be used. Together with the loading of the working mineral, coking coals are also loaded into the furnace. Their main task is to maintain high temperatures. In order to melt the ore faster andget access to the iron, flux is sent to the furnace. A substance that is a catalyst promotes faster decay of ore.
It is important to note here that before loading into the furnace, the ore usually goes through a process of crushing, washing, drying. All these steps contribute to the removal of excess impurities, as well as an increase in the speed of melting.
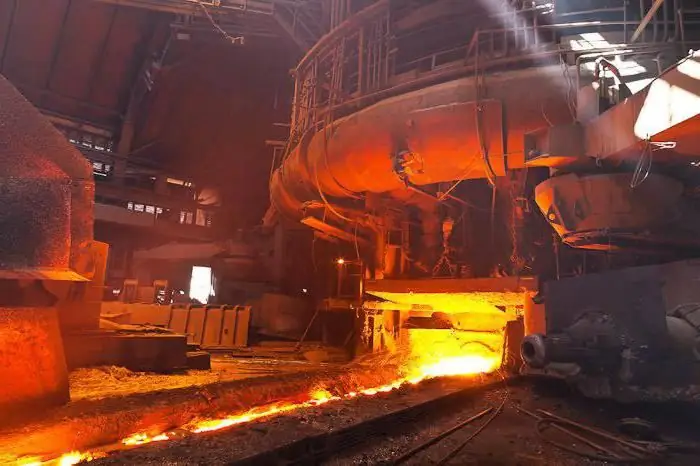
Second stage
The second stage of pig iron smelting is started when all the necessary materials have been loaded into the blast furnace. The burners are started, which heat the coke, which heats the ore. It is important to know that when heated, the coke begins to emit carbon into the air, which passes through it, reacts with oxygen and forms an oxide. This volatile substance takes an active part in the recovery processes. However, this process proceeds only as long as air remains in the furnace. The more gas inside the blast furnace, the weaker this effect, and over time it stops altogether. When this moment comes, all the gas present inside the furnace leaves to maintain a high temperature inside the unit.
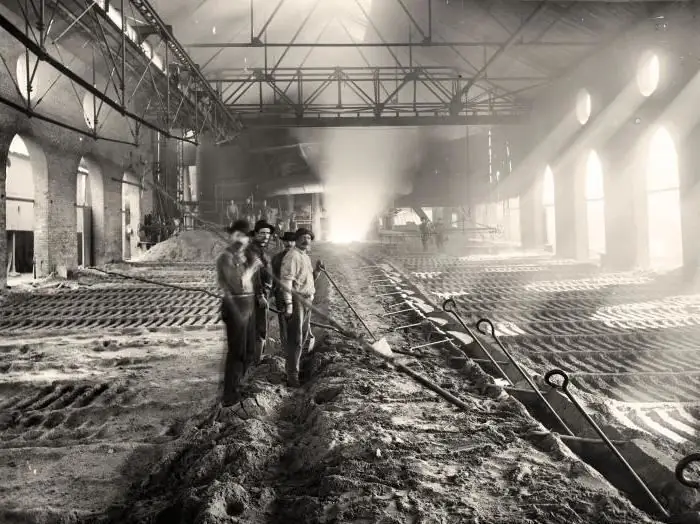
All excess carbon mixes with the molten substance, is absorbed by iron, which forms cast iron. All elements that did not melt during the melting process float to the surface, from where they are removed. After this purification process is completed, there comes a time when various additives are added to the molten raw material. What kind of cast iron will turn out as a result depends onwhat type of additives will be used.
Which pig irons?
If we consider the conversion substance in more detail, we can note several distinctive qualities. Firstly, the content of manganese and silicon in the composition is much lower, and secondly, it is used to produce steel using the oxygen-converter method. If we talk about cast iron, then it is used for the production of a wide variety of products. It is also important to note here that all material belonging to this group is divided into several types.
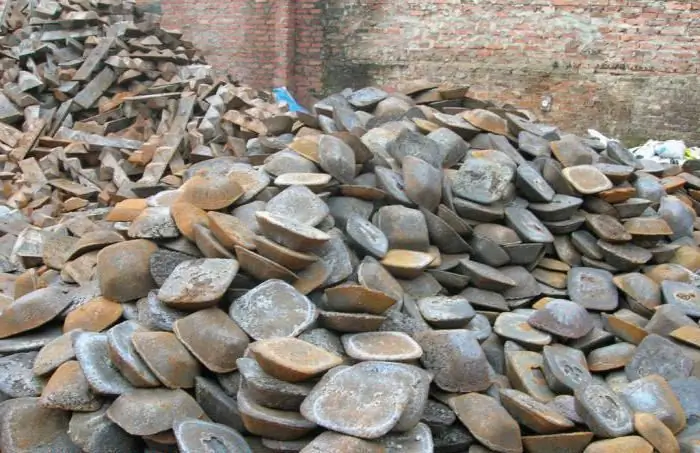
Further, you should know that, depending on its composition, pig iron is divided into classes:
- P1 and P2 are the markings of a common rework substance;
- PF1, PF2 and PF3 are phosphorous raw materials;
- PVK1, PVK2 and PVK3 are a group of high quality cast iron;
- Pig iron PL 1 and PL2 is a category of materials related to foundry production.
For an example, we can consider the content of these substances in raw materials with an average quality index. The content of Si is from 0.2 to 0.9%, Mn is from 0.5 to 1.5%, P is not more than 0.3%, S is not more than 0.06%.
Features of the chemical composition
If we consider the chemical composition required by the specifications, we should note an important feature. The main purpose of pig iron is to be melted into steel, and therefore the requirements for its quality and composition are determined by steelmaking processes.
One of the weaknesses of this technological process wasthat he is not able to cope with such an impurity as sulfur. And since the main difference between cast iron and steel is carbon content, it becomes clear that the main task that must be performed is the removal of carbon from the composition. In order to achieve this goal, it is necessary that the chemical composition allows the oxidation process to take place. It is through the oxidation of carbon that it is removed from pig iron.
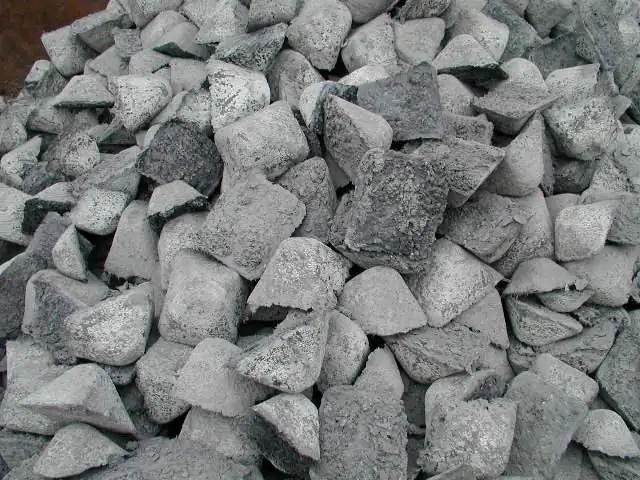
However, here it is necessary to understand that when carbon is oxidized, other impurities will also be affected - silicon, manganese, and to a lesser extent - iron. The substances obtained during this process are called oxides, after which they are transferred to the slag discharge. The end product of such an industry is ferruginous slag - these are wastes with a high iron content, which significantly complicate the removal of sulfur from the composition. For this reason, the mass fraction of element S should be minimal in the composition of pig iron.
Recycling in other devices
Depending on the method by which cast iron was processed into steel, different specifications for the composition will be presented.
Using an oxygen converter device, you can get rid of such impurities as phosphorus. The higher the mass fraction of this element, the higher the cold brittleness of raw materials (cracking at low temperatures).
If we take, for example, open-hearth furnaces, then they can melt cast iron into steel of almost any kind. However, it is important to monitor the quantitative content of phosphorus and silicon. Howthe higher the mass fraction of these elements, the more expensive the rework process will be. In addition, the time required to complete the work greatly increases. For this reason, their content in the composition of the material should not exceed the average values according to the technical documentation. It should be noted that the content of manganese in pig iron is not limited. This is due to the fact that it contributes to the processes associated with the removal of sulfur.
Pig iron is characterized by the fact that the silicon content in it is higher - up to 1.2%.
State standard
As is the case with other industrial materials, cast iron must be manufactured according to strict rules, described in the state standard. For pig iron, GOST 805-95 establishes all the technical conditions according to which it must be created. The quantitative content of all chemical elements in each of the groups is regulated.
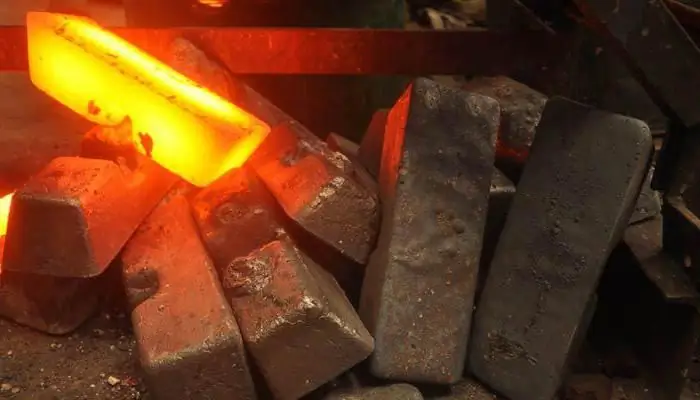
GOST technical requirements
The documentation indicates the points that must be observed in any case, and there are those that are set by the consumer under an agreement with the manufacturer.
The first category includes the following rules:
- Pig iron grades related to PL1 and PL2 must be delivered to processing sites with the obligatory indication of the mass fraction of carbon in the composition.
- If pig iron is smelted from copper-bearing ores, then the mass fraction of this element should ultimately not exceed 0.3%.
- The production of this material is carried out iningots, without pinches, with one pinch or two pinches maximum. In places of pinching, the thickness of the ingot (ingot) should not exceed 50 mm.
- The mass of a pig should not exceed such values as: 18, 30, 45, 55 kilograms.
- There should not be any slag residues on the surface of these units.
Customer Requirements
GOST 805 for pig iron also regulates several technical requirements that the consumer has the right to set when ordering from the manufacturer. These include the following items:
- Pig iron grades related to PL1 and PL2 must be produced with a mass fraction of carbon in the composition from 4 to 4.5% inclusive.
- If we consider the same grades PL1 and PL2, which will subsequently be used for the manufacture of castings from cast iron with nodular graphite, then the mass fraction of chromium in such a substance should not exceed 0.04%. Also, in the manufacture of high-quality pig iron according to GOST, for the further production of piston rings, the manganese content should be limited to 0.3%, and chromium to 0.2%.
- If there are no special requests, then ordinary recycled and high-quality material should be made with a manganese content of more than 1.5%. If pig iron of the phosphorous group is produced, then the phosphorus content is more than 2%.
- The mass fraction of silicon in grades such as PL1, PF1 and PVC1 should be more than 1.2%.
- A very important point is the sulfur content, which is allowed no more than 0.06% in types of cast iron P1, P2 and PL1, PL2.
Acceptance andquality control
The document also establishes the rules for receiving goods and quality control operations.
This material may only be accepted in batches. A batch is pig iron that belongs to the same brand, group, type and type, and also has a document that confirms the quality of the product. Most often, such papers indicate: the trademark of the enterprise that manufactured the product; name of the enterprise acting as a consumer; brand, group, class and category of cast iron, control stamp and a few more items.
If we talk about control methods, then here it is necessary to check the quality of the flakes. It is not necessary to use magnifiers for this. In order to carry out quality control concerning flakes, the method that has been agreed between the consumer of the product and the manufacturer is used. If the mass of the batch is up to 20 tons, then 10 samples of scales are taken from different places. If the mass exceeds 20 tons, then 20 samples must be taken from the surface of the cast iron.
Structural quality
It is worth adding that there is a special division of cast iron into such types as: white, gray, malleable, high-strength. The division into types is carried out depending on the structure of the material.
For example, the category of white cast iron is that batch of material in which all the carbon is in a chemically bound state, and also has the appearance of cementite. Due to the presence of this substance, the color of cast iron turns white, hence the name.
If we talk about gray cast iron, then the main distinguishing quality here is carbon,which is presented in the form of graphite with the form of curved plates or flakes. Due to the large number of these elements, the fracture of cast iron has a gray color. An alloy of iron with carbon is produced in large quantities in China, Japan, Russia, India, South Korea, Ukraine.
Recommended:
Pig breeding at home - features, breeding and maintenance
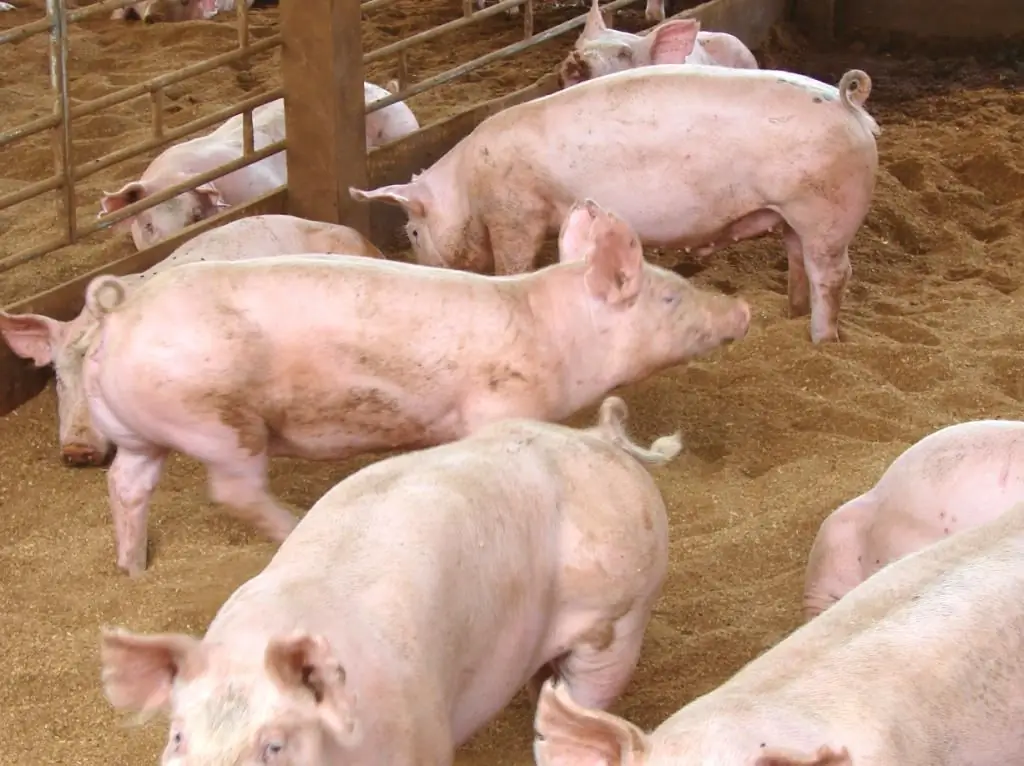
How to start pig farming at home. What is the profitability of this business. How to equip pigsties. The right choice of breed and the acquisition of piglets. What to consider when writing a business plan. Pig diseases. Getting offspring
Yorkshire pig breed: description, productivity, cultivation
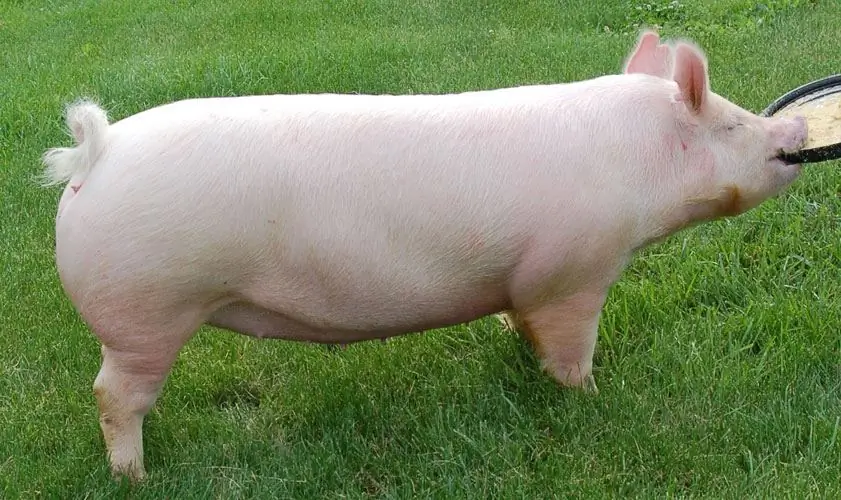
Pork is one of the most popular types of meat in most countries. It is quick to prepare, inexpensive, and the dishes from it are very tasty. Breeding pigs is a profitable business, this meat will always be in high demand. But which breed should you choose? We recommend taking a closer look at Yorkshire pigs
Pig breeding business
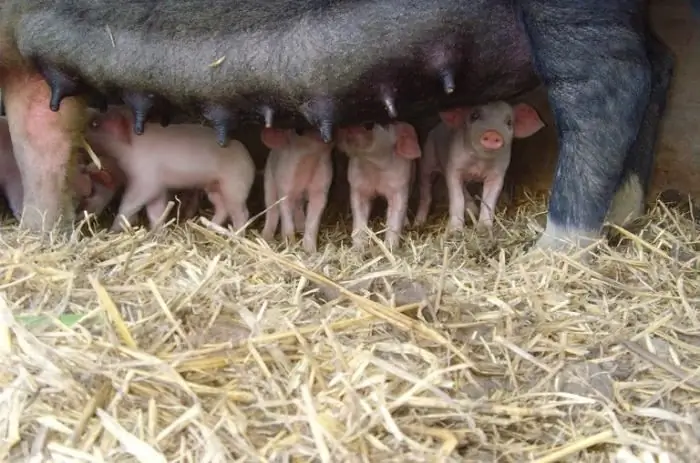
Agriculture attracts many modern entrepreneurs. Especially when it comes to breeding pigs in rural areas. This business idea has many advantages, since nature has endowed pigs with unique properties. In terms of productivity, no other type of farm animal can be compared with them
Pig iron production in Russia, development history
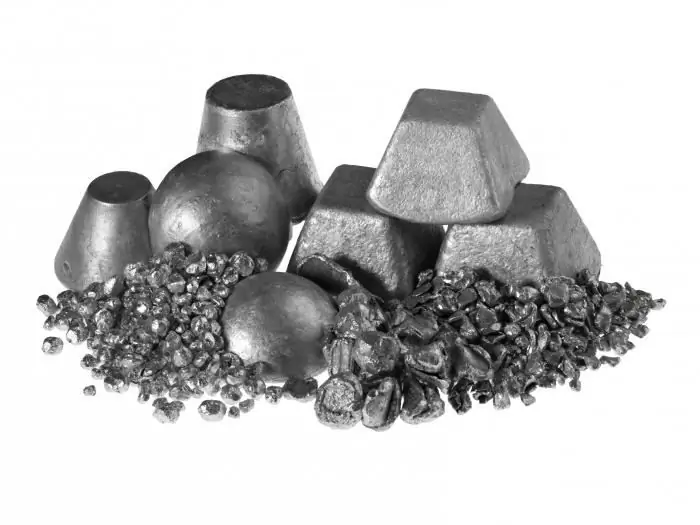
For several hundred years, the Russian Federation has been among the world leaders in the production of pig iron. This alloy is used in a variety of industries, is used to create artistic and decorative products
Pig anatomy. Similarities between human and pig DNA
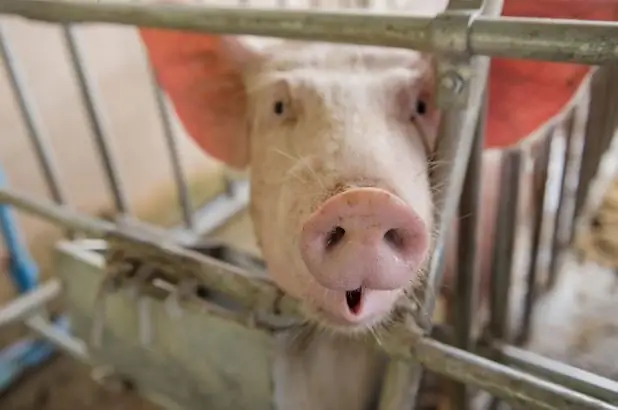
Pig anatomy has been studied quite well by scientists. Animals are hardy and unpretentious. Both the cardiovascular and nervous, reproductive and other systems are well developed in piglets