2025 Author: Howard Calhoun | [email protected]. Last modified: 2025-01-24 13:10
The textile industry until recently remained an industry with a high proportion of manual labor. The reason for this is the difficulty in machining the fabric.
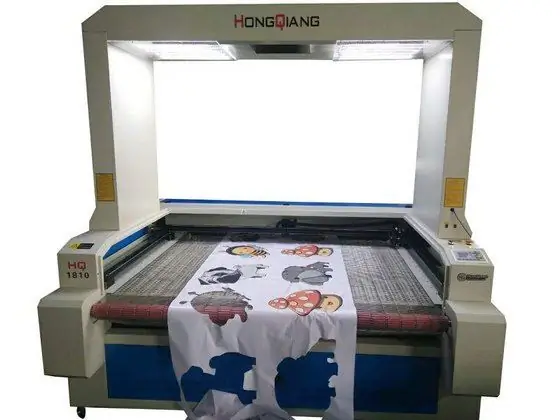
The situation has changed radically when the technology of laser cutting of fabrics has become more widespread. The thinnest seam of the cut provides a high-energy beam, and the laser machine controlled by the CNC microprocessor system can carry out figured cutting of fabric blanks and ensures high quality processing, the absolute absence of marriage and great material savings.
In addition, CNC laser fabric cutting machines are quite easy to maintain and operate - anyone can easily handle them.
And most importantly - most models of machines are quite affordable for a small business, private workshop or art studio. With a competent approach to choosing equipment for fabric processing, a business will be able to get a powerful machine base, while requiring a minimum of cash costs.
Machine Features
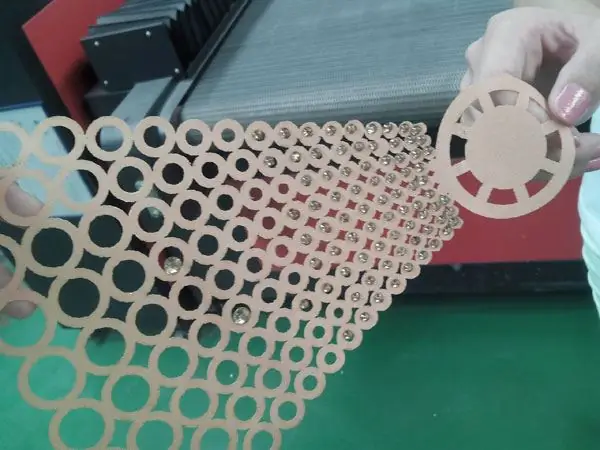
The CNC laser machine has a solid steel body with a table inside where the workpieces are placed, a tool portal that carries the head of the emitter, the laser tube that generates radiation. Stepper motors are provided for the movement of the tool portal, they are controlled by the CNC system. All machine systems are controlled by the CNC controller, it is also equipped with built-in memory, where program files are loaded for processing.
Working principle
The workpiece to be processed is spread out on a working horizontal table. Its area corresponds to the maximum size of the processed workpiece. It can be placed on the table both manually and with the help of an automatic loader. In this case, the laser machine is able to work with fabric in rolls, which will greatly simplify the technological process.
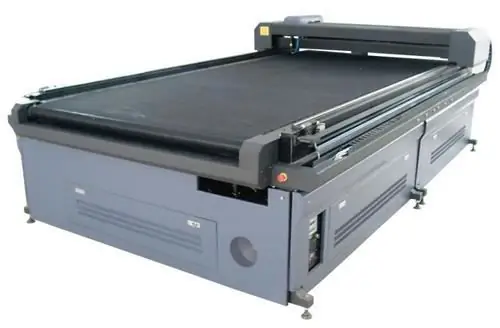
The machine starts to work after the workpiece is placed and the control program is loaded. Moving above the plane of the tissue, the laser head delivers a pulse at a given point with a power that will be sufficient for through cutting of the tissue. Since the laser acts on the tissue for a fairly short time, the adjacent layers are not affected by through burning - this allows you to achieve fineness and accuracy of the cut edges. Machines, thanks to this feature, can produce laser cutting of leather and fabrics, including synthetic and complex in texture.
According to the processing route, the laser head moves on the tissuecontinuously. This allows you to repeat the software sketch exactly.
Versatility is the strongest advantage of fabric laser cutting equipment. The machine can be instantly reconfigured for the production of products of various types, and there will be no difference whether it is a mass batch or a single product. All copies of manufactured products are identical and of high quality.
Selection criteria
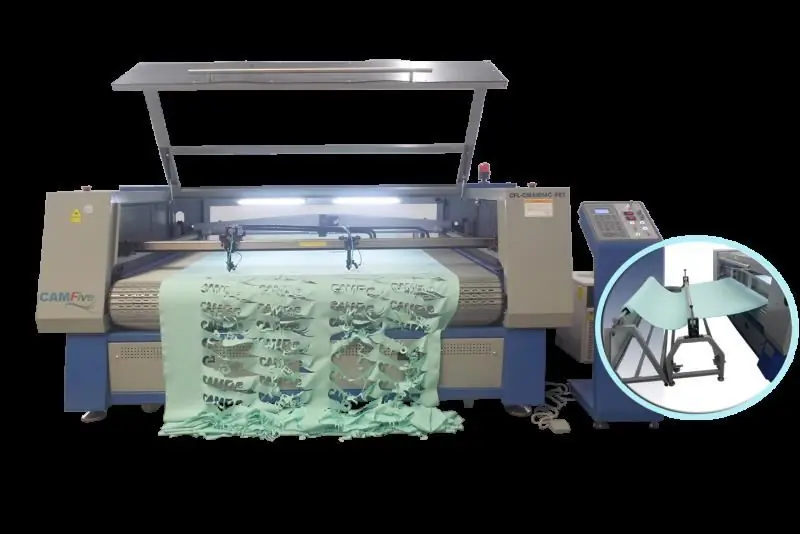
To work productively on fabric cutting equipment, it is worth adhering to some selection criteria when purchasing. If everything is done correctly, production will go with a bang.
First criterion - area
The first and most important criterion is the area of the desktop. Of course, for each production, an individual size of the working surface will suit.
The counterbalance to this requirement is the price, because the larger the size of the machine, the higher its cost. However, a larger format machine is more versatile if the need arises to quickly expand production.
Second criterion - power
The second criterion is the power of the laser tube. Of course, very high power is not required to cut the fabric (even a weak machine can handle thick fabric and burn through). However, high processing speed can be achieved with sufficient power.
Third criterion - fabric autoload
Working with a roll blank will help get rid of two processes at once: preliminary cutting and manual loading of the fabric. In the basic configuration, not everythe model of the laser machine has a mechanical autoload. In addition, this mechanism may not be required if the work is done with small batches or individual orders.
Fourth criterion: hood scheme
One of the advantages of laser cutting fabric is that there is no solid waste. Only the gaseous residue is obtained in the process of "irradiation" of the tissue. The laser machine for gas removal is equipped with a regular exhaust. Also, when choosing equipment, it should be taken into account that a number of machine models have exhaust systems with flexible performance.
Fifth criterion - manufacturer and service
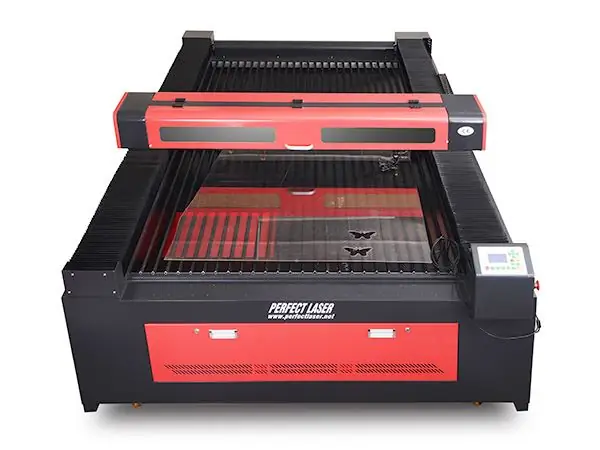
After forming the "image" of the machine according to the above criteria, you can choose a specific model that is offered on the market. Products from different manufacturers fluctuate in cost - especially Chinese technology has tempting offers. However, it is best to give preference to a manufacturer that can provide a guarantee and has a well-developed service network. Otherwise, there is a risk of getting an inoperable cheap fabric laser cutting machine.
Recommended:
Jute fabric: description with photo, structure, fabric composition and application
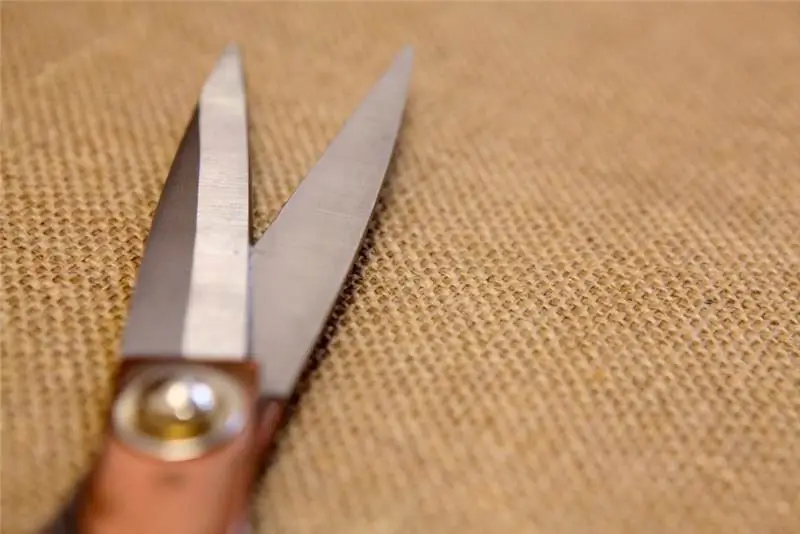
Jute fabric is widely used to make a variety of products. In most cases, such material is, of course, used for sewing packaging bags. But jute can also be made, for example, water filters, various kinds of decorative crafts, screens, etc
Cutting mode for milling. Types of cutters, calculation of cutting speed
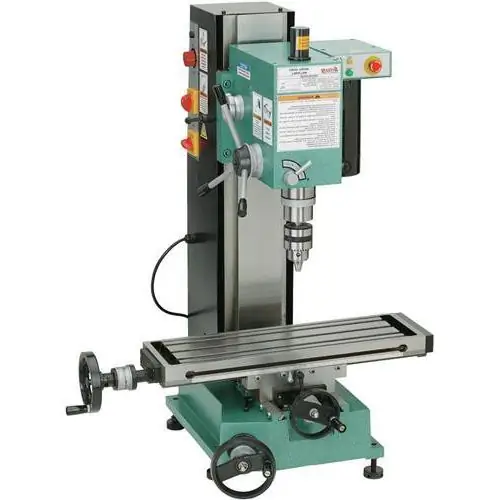
One of the ways to finish materials is milling. It is used for processing metal and non-metal workpieces. The workflow is controlled by cutting data
Laser engraving on plastic: types of plastic, choice of pattern, necessary laser equipment and patterning technology
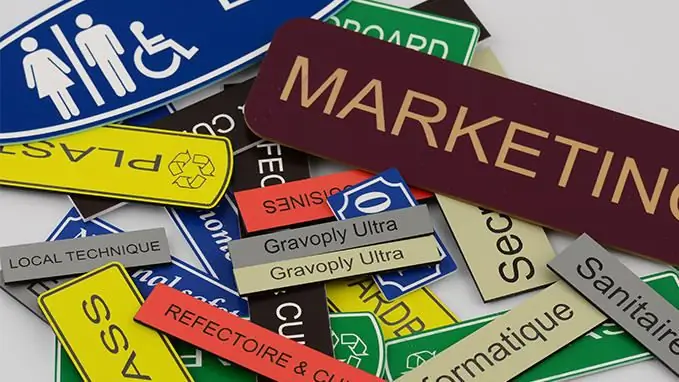
What types of plastic are used when applying laser engraving. Designs suitable for engraving and their types. How to edit and prepare photos for laser engraving. Necessary equipment for work, principles of its operation
Metal cutting machine. Plasma metal cutting machine
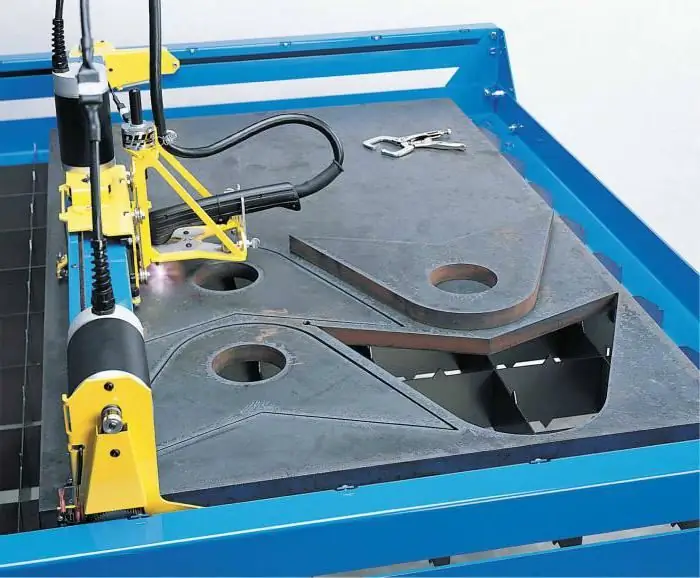
The article is devoted to the apparatus for cutting metal. The technology of plasma cutting, as well as the device and features of the equipment are considered
Cutting conditions for turning: description, features of choice and technology
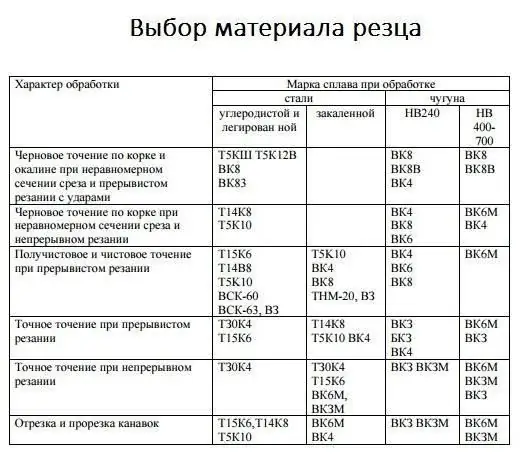
In order to turn an ordinary blank into a suitable part for a mechanism, turning, milling, grinding and other machines are used. If milling is necessary for the manufacture of more complex parts, for example, gears, cutting splines, then turning is used to manufacture simpler parts and give them the necessary shape (cone, cylinder, sphere)