2025 Author: Howard Calhoun | [email protected]. Last modified: 2025-06-01 07:12
Copper refining is the process of refining metal through electrolysis. Electrolysis cleaning is the easiest way to achieve 99.999% purity in copper. Electrolysis improves the quality of copper as an electrical conductor. Electrical equipment often contains electrolytic copper.
What is this?
Copper refining or electrolysis uses an anode that contains impure copper. It arises from the concentration of ore. The cathode consists of pure metal (titanium or stainless steel). The electrolyte solution consists of sulfate. Therefore, it can be argued that copper refining and electrolysis are one and the same. An electric current causes copper ions from the anodes to enter the solution and deposit on the cathode. In this case, impurities either leave, or form a precipitate, or remain in solution. The cathode becomes larger than pure copper and the anode shrinks.
Electrolytic cells use an external DC source to respond to reactions that would not otherwise be spontaneous. Electrolytic reactionsused to clean plate metals on many types of substrates.
Using an electrolytic process to purify metal (copper refining, metal electrolysis):
- Because impurities can greatly reduce the conductivity of copper wires, it is necessary to clean the contaminated copper. One of the cleaning methods is electrolysis.
- When a strip of impure copper metal is used as an anode in the electrolysis of an aqueous preparation of copper sulfate, the copper is oxidized. Its oxidation proceeds more easily than the oxidation of water. Therefore, metallic copper dissolves in solution in the form of copper ions, leaving behind many impurities (less active metals).
- Copper ions formed at the anode migrate to the cathode where they are more easily reduced than water and metal "plates" at the cathode.
It is necessary to pass sufficient current between the electrodes, otherwise a non-spontaneous reaction will occur. By carefully adjusting the electrical potential, metal impurities that are active enough to oxidize copper at the anode, the substances are not reduced at the cathode, and the metal is selectively deposited.
Important! Not all metals are reduced or oxidized more easily than water. If so, the electrochemical reaction requiring the lowest potential will occur first. For example, if we were to use electrodes, both anode and cathode, the metal potential would be oxidized at the anode, but then the water would decrease at the cathode and the aluminum ions would remain in solution.
To create electrolysis, you need to usethe following copper refining method:
- Pour the copper sulfate solution into a glass.
- Place two graphite rods in the copper sulfate solution.
- Connect one electrode to the negative DC power terminal and the other to the positive terminal.
- Fill two small tubes completely with copper sulfate solution and place a stopper on each electrode.
- Turn on the power supply and check what happens at each electrode.
- Test any gas produced with a flaming tire.
- Record your observations and the results of your tests.
Results should look like this:
- Brown or pink solids appear in solution.
- There are bubbles.
- Bubbles should be colorless.
- A substance in gaseous form.
All results are recorded, after which the gas is extinguished by the tire. There is also another way to clean the metal from impurities and third-party dirt - this is the fire refining of copper. How this happens, we will tell later, but now we will present other options for refining the metal.
Methods of refining copper - how else can chemical stripping of the desired metals take place?
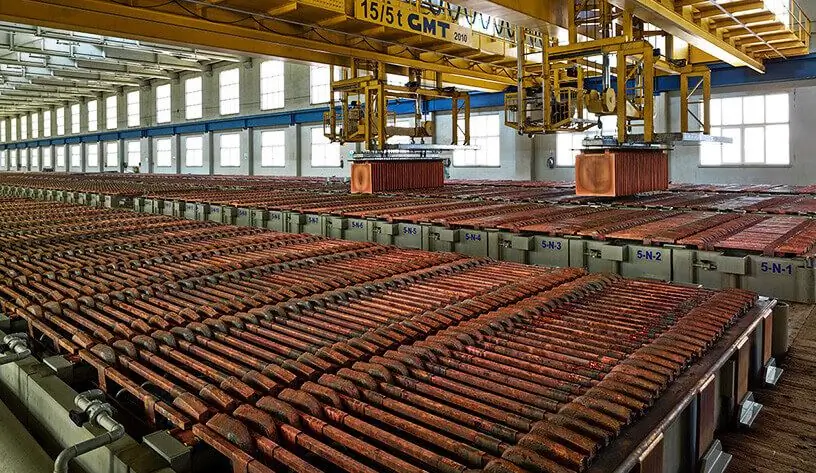
Since electrolysis is the action of sulphates and current, what is the electrolytic method for obtaining pure products? Completely different things, although similar in sounding names. However, the electrical refining of copper is based on the use of acids. We can say that this is the oxidation of the metal, but not quite.
Clean production is important for making electrical wire, as the electrical conductivity of copper is reduced by impurities. These impurities include precious metals such as:
- silver,
- gold;
- platinum.
When they are removed by electrolysis and restored in the same way, electricity is spent as much as would be enough to supply electricity to dozens of homes. The purified component saves energy, powering even more homes in less time.
In electrolytic refining, an impure composition is made from an anode in an electrolytic bath of copper sulfate - CuSO4 and sulfuric acid H2SO 4. The cathode is a sheet of very pure copper. As current is passed through the solution, positive copper ions, Cu2+ are attracted to the cathode, where they take on electrons and are deposited like neutral atoms, thereby creating more and more pure metal at the cathode. Meanwhile, the atoms in the anode donate electrons and dissolve in the electrolyte solution as ions. But the impurities in the anode don't go into solution because the silver, gold, and platinum atoms don't oxidize (become positive ions) as easily as copper does. Thus, silver, gold and platinum simply fall from the anode to the bottom of the tank, where they can be cleaned.
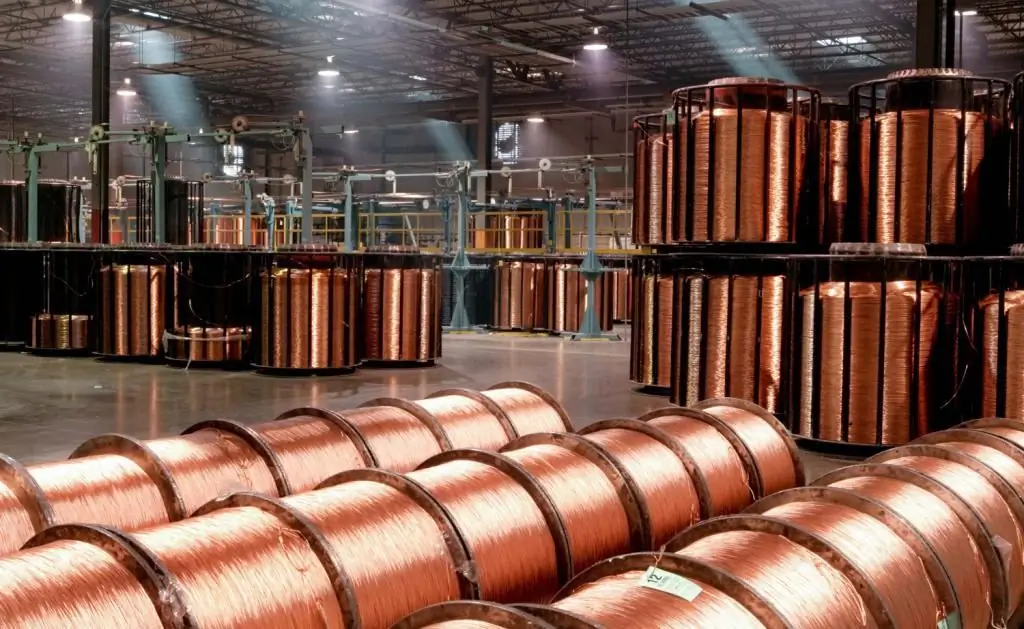
But there is also electrolytic refining of copper when tanks are used:
- Electrolytic treatment tanks areseparate workshop in industrial production. The anode plates are suspended by "handles" in a tank for cleaning electrolytic copper. Pure copper cathode sheets suspended on solid rods are inserted into the same tank, one sheet between each anode. When an electric current is passed from the anodes through the electrolyte to the cathodes, the copper from the anodes moves into solution and is deposited on the starter sheet. Impurities from the anodes settle to the bottom of the tank.
- Injection molding machine with copper anodes (plates). It will smoothly turn into anode plates in molds. After pre-treatment, tin, lead, iron, and aluminum are removed. Next, the copper material begins to be charged into the furnace, followed by the smelting process.
- When impurities are removed, slag removal and reduction phase with natural gas follows. The reduction is aimed at removing free oxygen. After recovery, the process ends with casting, where the final product is cast as copper anodes. The same machine can be used to cast these anodes during component recycling or to recycle anodes for scrap metal in an electrolysis copper smelter.
- Clean cathode sheets. The modifying anodes extracted from the refining furnace are converted into electrolytic copper with a purity of 99.99% through the electrolysis process. During electrolysis, copper ions leave an impure copper anode and, since they are positive, migrate to the cathode.
From time to time pure metal is scraped off the cathode. copper anode impurities such as gold,silver, platinum and tin collect at the bottom of the electrolyte solution and precipitate as anode slime. This process is called the electrowinning and refining of copper.
Obtaining a fossil - what kinds exist and are they all necessary in practice?
A slightly different way of cleaning metal. There is also fire and electrolytic refining of copper, when one process immediately follows another. An important "separating" stage becomes concentration or concentration. Once concentration is complete, the next step in creating the finished product is copper fire refining.
Usually this happens near a mine, at a processing plant or a smelter. Through copper refining, unwanted material is gradually removed and copper is concentrated to a purity of up to 99.99% Grade A. The details of the refining process depend on the type of minerals with which the metal is associated. Sulfide-rich copper ore is pyrometallurgical processed.
Refining & Pyrometallurgy:
- In pyrometallurgy, copper concentrate is dried before being heated in a furnace. The chemical reactions that occur during the heating process cause the concentrate to separate into two layers of material: a matte layer and a slag layer. The matte layer on the bottom contains copper, while the slag layer on top contains impurities.
- The slag is discarded and the matte layer is restored and moved into a cylindrical vessel called a transducer. Various chemicals are added to the converter that react with the copper. This leads to the formation of converted copper, called"blister". Once precipitated, it is extracted and then subjected to another process called fire cleaning.
- In a fire scrubber, air and natural gas are blown through to remove the remaining sulfur and oxygen, causing the refined composition to be processed into the cathode. The metal is cast into anodes and placed in an electrolyzer. After charging, pure copper is collected at the cathode and removed as 99% pure product.
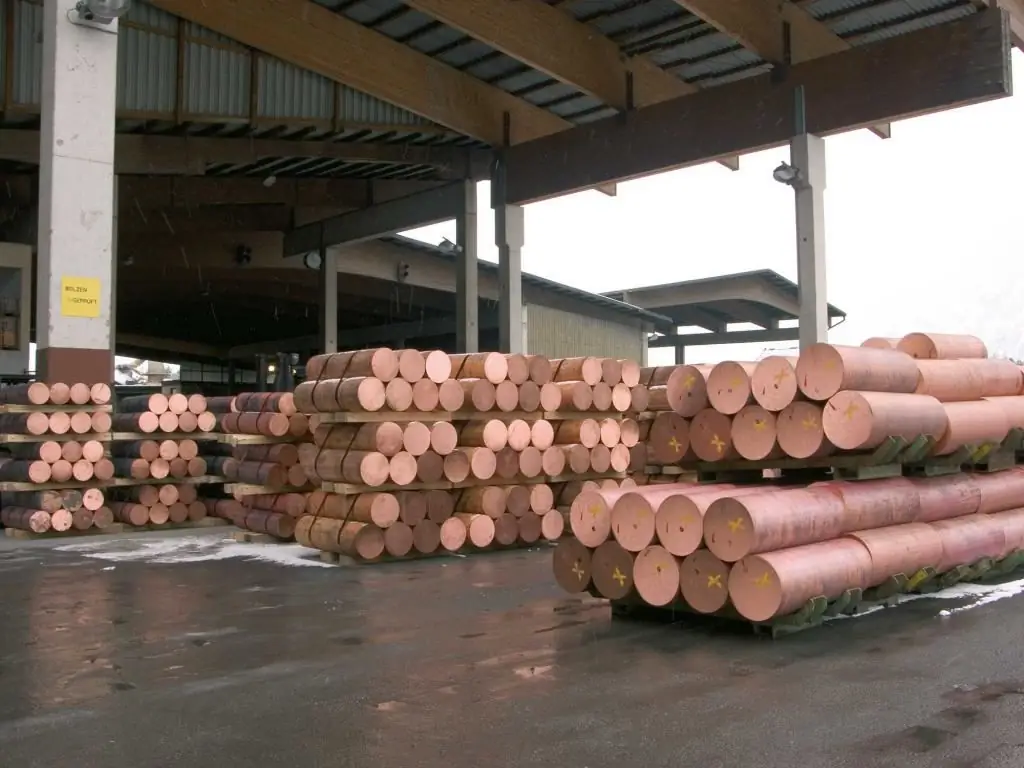
Refining & Hydrometallurgy:
- In hydrometallurgy, copper concentrate is processed through one of several processes. The least common method is carburizing, where metal is deposited onto scrap metal in an redox reaction.
- The more widely used purification method is solvent extraction and electrolysis. This new technology became widespread in the 1980s, and approximately 20% of the world's copper is now produced this way.
- Solvent extraction starts with an organic solvent that separates the metal from impurities and unwanted materials. Sulfuric acid is then added to separate the copper from the organic solvent to form an electrolytic solution.
- This solution is then subjected to an electrolysis process that simply puts the copper in solution on the cathode. This cathode can be sold as is, but can also be made into rods or source sheets for other electrolyzers.
Mining companies can sell copper in concentrate or cathode form. HowAs mentioned above, the concentrate is most often refined elsewhere than at the mine site. Concentrate manufacturers sell concentrate powder containing 24 to 40% copper to copper smelters and refineries. The terms of sale are unique to each smelter, but in general the smelter pays the miner approximately 96% of the cost of the copper content in the concentrate, minus processing fees and refining costs.
Smelters generally charge tolls, but they can also sell refined metal on behalf of the miners. Thus, the entire risk (and reward) from fluctuations in copper prices falls on the shoulders of resellers.
Fire refining - how dangerous is it?
The hottest fire refining can't be safe, but the processing method is currently used by most industrial plants. Separately, it is worth describing the technology of refining blister copper.
Blister copper is already almost pure (more than 99% copper). But for today's market, this is not very "clean". The metal is further purified using electrolysis. In industrial production, a method called fire refining of blister copper is used. The ink copper is cast into large slabs to be used as anodes in the electrolyser. Electrolytic post-refining produces the high-quality, high-purity metal required by the industry.
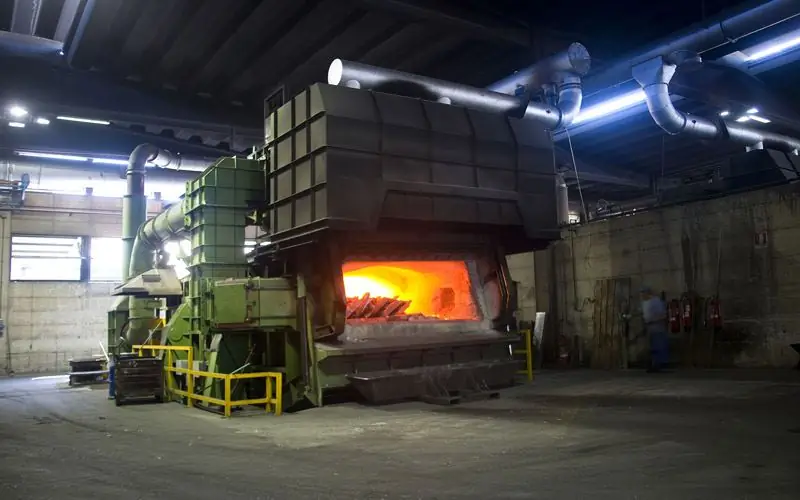
In industry, this is done on a massive scale. Even the best chemical method cannot remove all impurities from copper, but electrolytic refining can produce 99.99% pure copper.
- The anode blisters are immersed in an electrolyte containing copper sulfate and sulfuric acid.
- Clean cathodes are located between them, and a current of more than 200 A passes through the solution.
Under these conditions, copper atoms dissolve from the impure anode to form copper ions. They migrate to the cathodes, where they are deposited back like pure copper atoms.
- At the anode: Cu(s) → Cu2 + (aq) + 2e-.
- At the cathode: Cu2 + (aq) + 2e- → Cu(s).
When the switch closes, the copper ions at the anode will begin to move through the solution towards the cathode. Copper atoms have already given up two electrons to become ions, and their electrons are free to move around in wires. Closing the switch pushes the electrons clockwise and causes some copper ions to settle in solution.
The plate repels ions from the anode to the cathode. At the same time, it pushes free electrons around the wires (these electrons are already distributed over the wires). The electrons in the cathode recombine with the copper ions from the solution, forming a new layer of copper atoms. Gradually, the anode is destroyed, and the cathode grows. Insoluble impurities in the anode fall to the bottom to precipitate. This valuable bio-product is being removed.
Gold, silver, platinum and tin are insoluble in this electrolyte and therefore do not deposit on the cathode. They form a valuable "silt" that accumulates under the anodes.
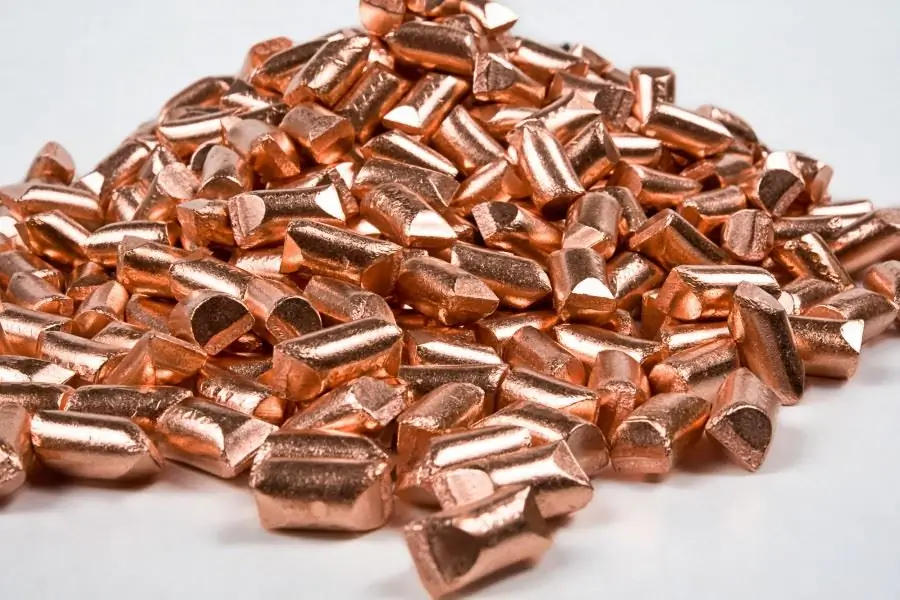
Soluble impurities of iron and nickel are dissolved in the electrolyte, which must be constantly cleaned to prevent excessive deposition on the cathodes, which will reduce the purity of copper. Recently, stainless steel cathodes have been replaced by copper cathodes. The same chemical reactions take place. Periodically, the cathodes are removed and pure copper is purified. Electrolytic production and refining of copper under these conditions is quite common in non-ferrous metal processing plants.
Electrochemical version of metal purification
Fire cleaning can be called chemical, because in this process a chemical reaction occurs with other substances and impurities. The above was an example of an oxidative reaction. All types and methods of extracting pure copper are similar, as is the electrochemical refining of copper, where identical tactics are used, but in a different sequence.
The chemical auxiliary element becomes the by-product itself:
- Caustic soda
- Chlorine.
- Hydrogen.
This is the cheapest way to get expensive raw materials without spending money on an alternative component mining system. In addition, valuable metals are mined, which are noble in composition and valuable in the industrial invention of electrical appliances.
Copper Furnace - Metal Cooking Industry
The Fired Copper Refining Furnace is specially designed and capable of processing scrap copper into liquid metal with controlled impurities. It is designed for pyrometallurgical processing of scrapeconomical and environmentally friendly technology. The main technology proposed for the production of molten copper is suitable for the production of copper stick, strip, billet or other copper products using scrap as raw material (Cu> 92%).
The capacity of incineration and cleaning systems was calculated for a cleaning cycle (from charging to recovery) of 16-24 hours, depending on the type of scrap. Copper refining furnaces have special design and functions:
- The furnace body is made of steel segments and rigid section-type structures.
- The furnace is lined with refractory material from the inside.
- It is equipped with a hydraulic station operating in the tilting furnace mode with two speeds: creep speed when tilting for casting and high speed during movement, which does not require much precision.
- Operations are performed by two hydraulic cylinders installed at the bottom of the furnace. A special device returns the oven to a horizontal position during power outages.
- The material loading hatch is located on the side of the oven. It is closed by a door driven by a hydraulic cylinder.
- The furnace is equipped with cooled lances for copper oxidation and reduction operations.
There is also one universal burner that consumes both liquid and gaseous fuels.
Oxidative refining in industry
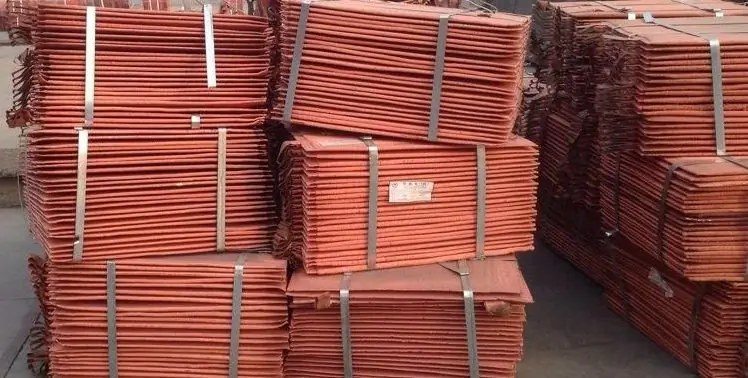
Operation of copper oxidation is carried out after the completion of the smelting of the feedstock. The process is carried out by injecting compressed air into the melt through tuyeres. The resulting slag is manually removed from the surface of the melt using a special rake and dumped into a container. The slag contains copper, impurities, lead, tin, etc. The reduction process must be carried out to remove oxygen from the melt and reduce copper oxides. The operation is performed by injecting natural gas into the melt.
From the furnace, exhaust gases are fed into the gas cleaning system, pass through the dust collector, which captures coarse dust. The collector is equipped with a vent pipe in case of emergency gas release into the atmosphere. The fire cleaning furnace operates continuously. The work cycle of the technological process includes:
- loading raw materials;
- oxidation, slagging, reduction;
- loading refined metal.
The whole subsequent process is called copper oxidative refining. It cannot be separated from the overall refining process, as it is part of the entire pure metal recovery process. After the required parameters are eliminated, the copper melt is used for the next technological process.
Iodide refining of non-ferrous metals
Copper(II) ions oxidize iodide ions to molecular iodine, and in this process they themselves are reduced to copper(I) iodide. The original mixed brown mixture separated into an off-white precipitate of copper(I) iodide in the iodine solution. Use this reaction to determine the concentration of copper (II) ions in solution. If you add the prescribed volume of solution to the flask,containing copper (II) ions, and then add an excess of potassium iodide solution, you will get the reaction described above.
2Cu2+ + 4I- → 2CuI (s) + I 2 (aqueous solution)
You can find the amount of iodine released by titration with sodium thiosulfate solution.
2S2O2-3 (solution) + I 2 (solution) → S4O2-6 (water solution) + 2I- (aqueous solution)
When the sodium thiosulfate solution is run from the burette, the color of the iodine disappears. When it's almost all gone, add starch. The entire copper iodide refining reaction will be reversible with iodine to produce a deep blue starch-iodine complex that is much easier to see.
Add the last few drops of sodium thiosulfate solution until the blue color disappears. If you trace the proportions through the two equations, you will find that for every 2 moles of copper(II) ions you should have started with, you need 2 moles of sodium thiosulfate solution. If you know the concentration of sodium thiosulfate solution, it is easy to calculate the concentration of copper (II) ions. The result of this attempt is to obtain a simple compound of copper (I) in solution.
Phosphorus treatment

Phosphorous copper refining is a phosphorous deoxidized hard copper, which is a general purpose tough resin. It is deoxidized by copper phosphorus, in which residual phosphorus is maintained at a low level (0,005-0.013%) to achieve good electrical conductivity. It has good thermal conductivity and excellent welding and soldering properties. The oxide after refining copper in this way, remaining in the solid copper resin, is removed with phosphorus, which is the most commonly used deoxidant.
The table shows different performance from annealed (soft) to hard state of copper.
Tensile strength | 220-385 N/mm2 |
Tear Strength | 60-325 N/mm2 |
Length | 55-4 % |
Hardness (HV) | 45-155 |
Electrical conductivity | 90-98 % |
Thermal conductivity | 350-365 W/cm |
Drive Frames connect wiring to electrical terminals on the semiconductor surface and large scale circuits on electrical devices and printed circuit boards. The material is selected to meet process requirements and be reliable in installation and operation.
Composition of copper after electrolysis
The composition of copper after fire refining includes 99.2% of the metal. Much less of it remains in the anodes. When impurities are completely removed, 130 g/l of cathode bases remain in the composition. The aqueous solution of vitriol becomes weak, and the acidic component of copper cathodes reaches 140-180 g/l. Blister copper contains 99.5% of the metal, iron has 0.10%, zinc up to 0.05%, and gold and silver are only 1-200 g / t.
Recommended:
Copper ore: mining, refining, deposits and interesting facts
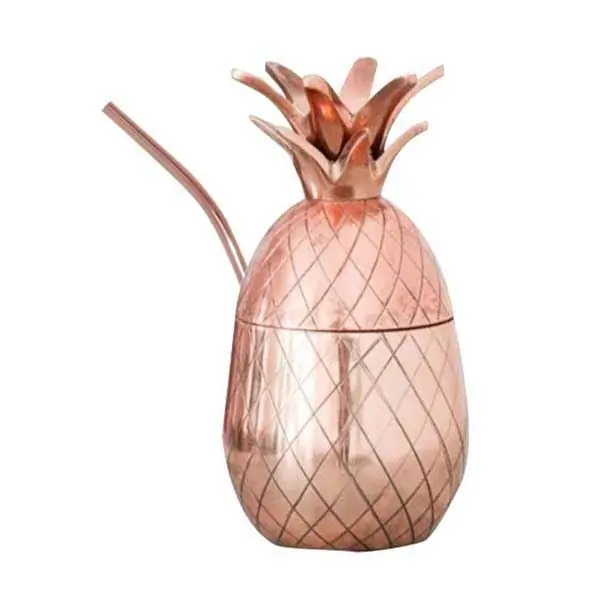
Copper is quite widely used in almost any of the existing industries, it stands out from a variety of ores because it is the most in demand. copper ore is a natural resource derived from an ore called bornite that is often used in industry. Great demand for this ore appeared not only due to the large amount of copper in the composition, but also due to the good reserves of bornite in the ground
Steel: composition, properties, types and applications. Composition of stainless steel
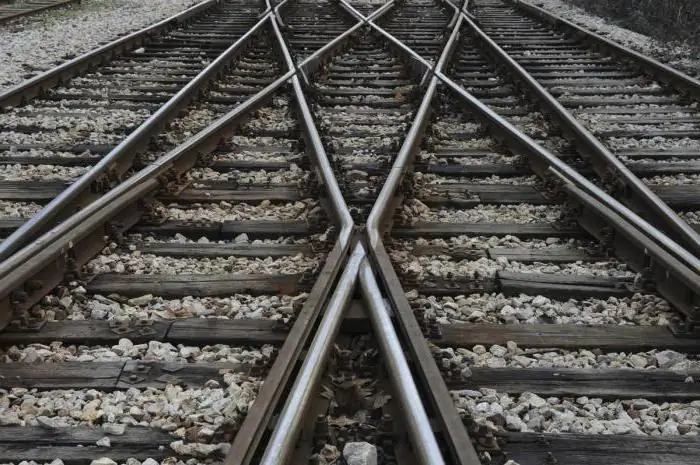
Today, steel is used in the vast majority of industries. However, not everyone knows that the composition of steel, its properties, types and applications are very different from the production process of this product
Tinned copper: concept, composition, manufacture, characteristics and application
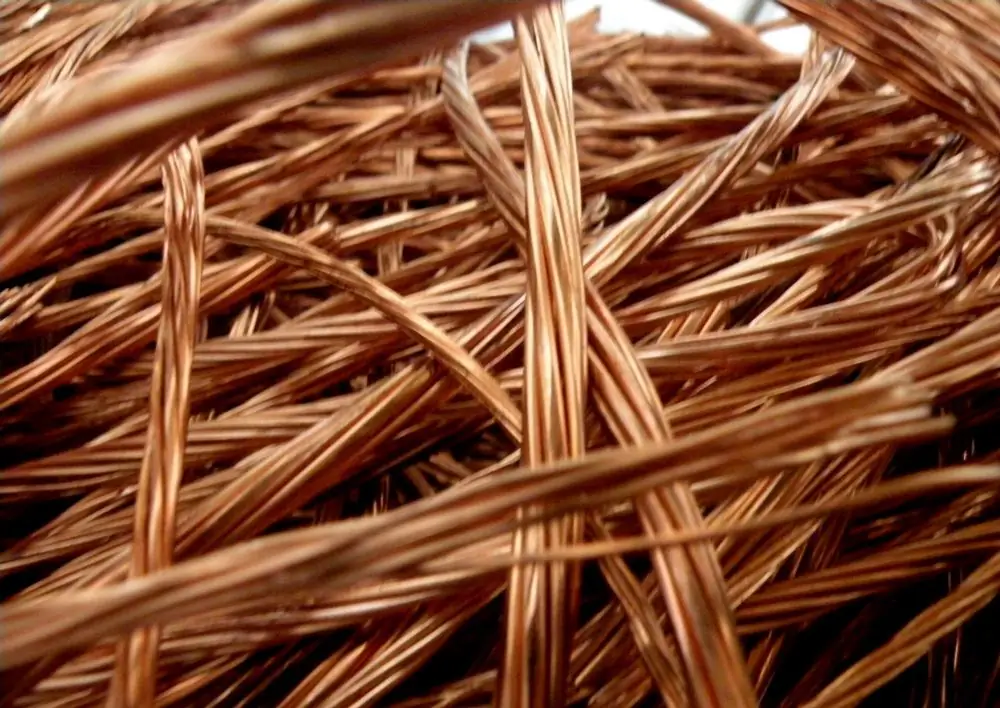
Tinning means to cover metal products with a thin layer of tin, which in turn prevents the process of oxidation of metal surfaces. But if we take into account the maintenance of the soldering iron, then the process is slightly different
Biodegradable polymers: concept, properties, methods of preparation and examples of reactions
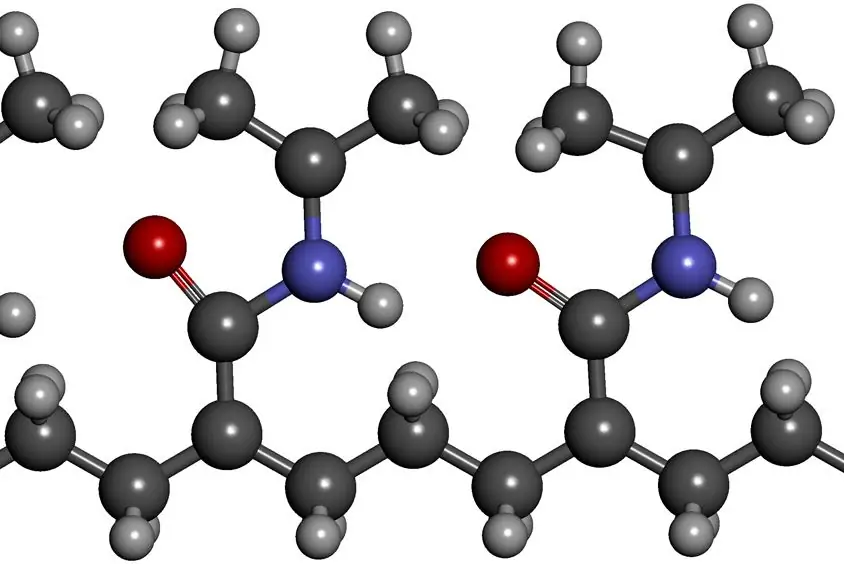
Biodegradable polymers were developed as an answer to the problem of plastic waste disposal. It's no secret that their volume is growing every year. The word biopolymers is also used for their abbreviated designation. What is their peculiarity?
Solder for soldering copper, aluminum, brass, steel, stainless steel. Solder composition for soldering. Types of solders for soldering
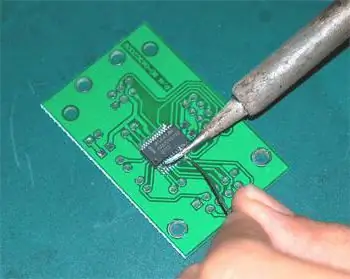
When it is necessary to securely fasten various solid joints together, soldering is most often chosen for this. This process is widespread in many industries. We have to solder and home craftsmen