2025 Author: Howard Calhoun | [email protected]. Last modified: 2025-01-24 13:10
Shaft-type grain dryers are currently in great demand. They provide uniform and stable blowing of the grain. Let us consider in more detail the device of a mine grain dryer.
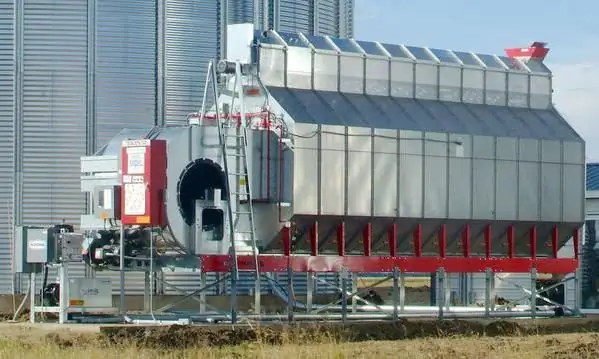
General information
The task of any grain drying equipment is to provide high-quality blowing of grain and oilseeds to reduce moisture. This allows you to store the product for a long time.
With the right choice of the operating mode of the equipment, it is possible to create conditions for the ripening of grain and thereby improve its quality characteristics.
One of the main advantages of modern equipment for drying grain is the almost complete elimination of the possibility of spontaneous combustion of the product.
Mechanism of action
The principle of operation of the mine grain dryer is as follows. Grain material (previously cleaned) is fed into the mine. Air currents heated by a heat block pass through the product layer. They come evenly from the inlet boxes, which alternate with the outlet ones. The boxes are arranged in a checkerboard pattern. They are open at the bottom and are tent-shaped.
Vertical partitions are installed above the boxes. Due to them, the incoming grain is divided into separate streams. This ensures uniform movement of the product along the height of the entire shaft and eliminates the creation of dead zones.
The waste coolant (air) is sucked in through the exhaust ducts by the fan and sent to the cyclone.
An unloader is installed at the outlet. They regulate the time spent by the product in the mine. With the help of a screw conveyor, grain is fed into the 2nd stream of the elevator (lifting mechanism). Then the product is sent either again to the mine or to the container for dried grain.
In a shaft-type grain dryer, the chamber is divided into three zones vertically: the first and second are for direct drying, and the third is for cooling.
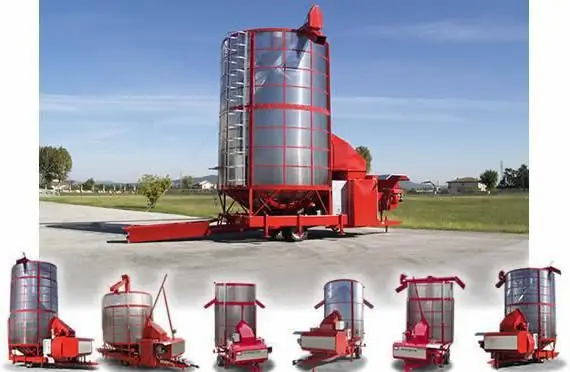
In the 1st zone, the air temperature is controlled by the heat block nozzle. In this section of the mine grain dryer, surface moisture is usually removed from the product. In the second zone, capillary moisture is already eliminated. The temperature here is lower than in the first compartment. The temperature in the second zone is controlled by dampers in the supply channel.
SZS-16
This unit is installed in cleaning and drying complexes and is used for drying feed, seed and food grains.
The design of this mine grain dryer consists of the following elements:
- 2 fans.
- Fireboxes.
- Graduationpipes.
- Diffuser.
- Drying chambers.
- Bunkers.
- Nori.
- Grain pipes.
- Cooling columns.
- Sluicegate.
- Unloader.
- Spigot.
- Pipeline.
Firebox
This is a self-contained unit connected to a shaft dryer. It is mounted in a separate building.
The coolant is obtained by mixing flue gases with air or by heating the latter. In the first case, the efficiency of the unit will be higher. In this regard, heated air is used only for drying food batches of cereals and grains.
The coolant enters through the pipeline and the inlet diffuser.
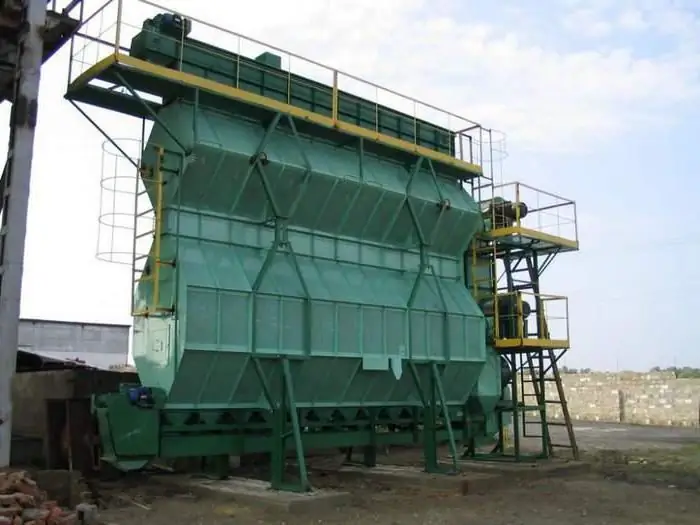
Drying chamber
It is a shaft, the size of which is 98019803650 mm. The shafts are mounted on a concrete base in such a way that the space formed between them is blocked by an inlet diffuser. A pipeline is connected to it.
Diffusers are installed on the side walls of the chambers, which are used to remove exhaust air. They are connected to a branch pipe and a suction ventilation window. There are blinds with a regulator in the branch pipe.
Mine Features
The design includes a frame, walls, five-sided boxes. There are 8 boxes in a row. The edge of each of them is directed upwards, and the open part is directed downwards.
The ends of the supply boxes are attached to the windows located in the wall facing the inter-minespace.
Bunkers
They are mounted above the shafts. The hoppers are of closed design.
On their vertical walls, sensors of the lower and upper levels of the grain material are installed, which automatically control the unloading device. It is located in the lower zone of each mine.
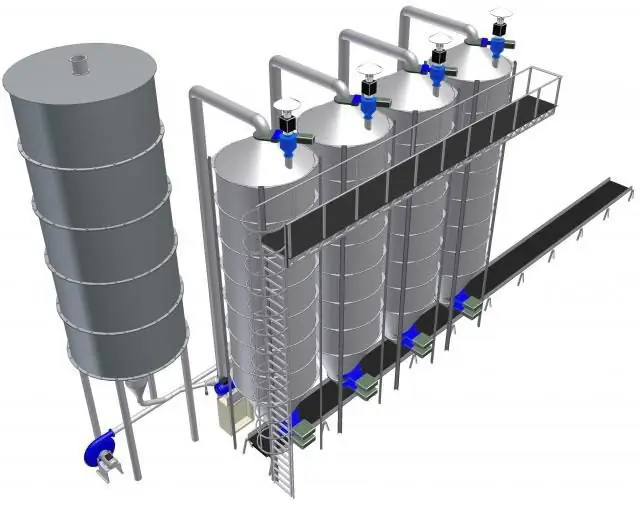
Unloader
It consists of a tray fixed box. It has 8 windows and a movable carriage on which the plates are fixed.
Under the action of a special mechanism, the reciprocating movement of the carriage is carried out.
Control of the speed of grain in the shaft dryer is carried out by changing the gap between the plates of the carriage and the outlet windows, as well as the amplitude of the vibration of the plates. For each move, a portion of grain is dumped into the bunker. The result is a continuous unloading of the dried product, the movement of the entire volume of grain material from top to bottom.
The gap is adjusted within 0-20mm by raising and lowering the carriage. The oscillation amplitude is regulated by changing the relative position of the drive eccentrics.
Accelerating the unloading of grain material is provided by a special switching mechanism. With its help, the carriage moves to a large amplitude, as a result of which the exit holes open completely.
Workflow Features
Wet grain is sent continuously by elevators to the bunker of each mine. The product enters the space between the boxes. Upon reachinggrain of the upper sensor automatically turns on the drive of the carriages. Under the force of gravity, the product in the shaft dryer begins to move down. When emptying the hopper to the lower sensor, the drive of the carriages will be automatically disabled.
During the movement of the grain down, a coolant passes through it, heats it, evaporates moisture, taking it away from the dryer.
The product is unloaded into the next hopper, then enters the elevator and is sent to the cooling towers. After cooling, the grain enters the next hopper with a sluice gate, then it is fed for further processing.
Process control
Periodically it is necessary to take grain samples to determine its moisture content and quality. To control the temperature, 3-4 samples are taken from different parts of the product in the lower boxes with a special scoop. The grain is poured into a box in which a thermometer is installed.
If the temperature is above the maximum allowable, the output of the material from the dryer is increased. If the humidity remains high, the product is sent for reprocessing.
After 5-7 days of operation, the shaft dryer must be cleaned.
Vesta series dryer
The mine grain dryer VESTA is considered a universal unit. It can be used to process grains, legumes and oilseeds.
The unit is made of galvanized steel, which is highly resistant to aggressive environmental factors.
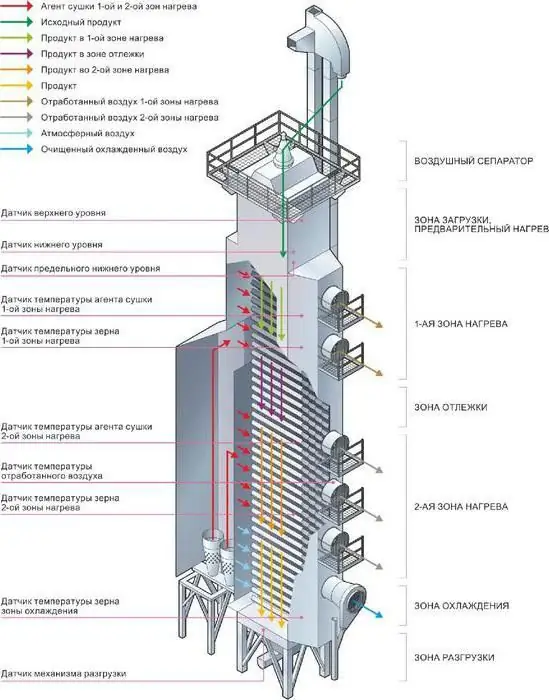
The tower of the machine is conditionally divided into 8 zones, going from top to bottom. Each zone has its ownpurpose, however, they all perform one common task - free the grain from moisture.
The design of the grain dryer includes:
- Cleaning and distribution area.
- Overdrying hopper.
- Preheat compartment.
- First heating zone.
- The resting area.
- Second heating zone.
- Cooling compartment.
- Unloading area.
At the inlet, the grain material passes through an air separator equipped with a spreading mechanism. At the same time, the grain is cleaned of impurities that appeared during transportation, and is also evenly distributed over the entire area of the dryer.
Process control is carried out in an automated mode. The unit is equipped with sensors:
- filling;
- temperature control;
- heating;
- exhaust air;
- fire zones;
- cooling zones;
- unloading mechanism.
Features of column dryer
This unit is also called modular. Column dryers can be vertical or horizontal.
In the operation of the units, the principle of transverse air flow (hot and cold) is used through a layer of grain material, which, in turn, passes between the walls made of perforated sheets.
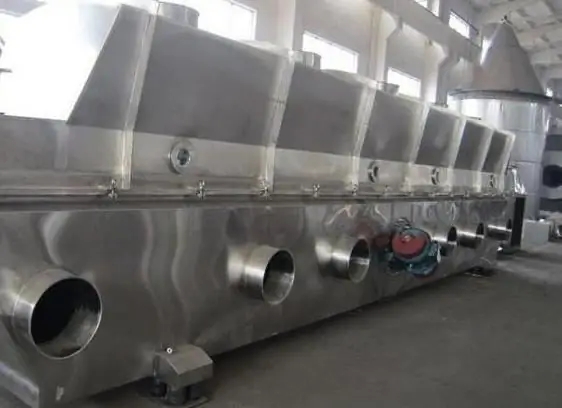
Column or modular such grain dryers are called because of the design features of the layout. They consist of columns (modules), the number of which is determined by performance,declared by the consumer.
Specific work
The mechanism of operation of column dryers is quite simple. It consists of the following:
- The grain material is fed into the upper part of the unit. There is a screw that distributes the product along the entire length of the machine. The columns are loaded sequentially. The dryer may look like a round tower with double walls. In this case, filling occurs under the influence of gravity, and the upper screw, respectively, is missing.
- The fan begins to blow air into the chamber, which is subsequently divided into 2 streams. One enters the mixing zone, the second is heated by a burner. In the chamber, both streams are mixed with the help of reflectors. This ensures temperature uniformity at any point.
- Due to the fact that the walls of the column are perforated, the grain is blown at a constant temperature.
- In the lower zone of the dryer there are dosing devices. They are called rollers. Their rotation speed regulates the residence time of the grain material in the columns. Thus, the necessary mode of product processing is provided.
- Unloading of grain material is carried out by the lower scraper or screw conveyor.
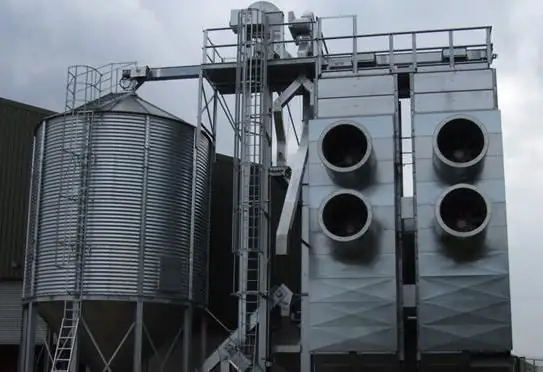
Flat perforated walls are under constant grain pressure. In this regard, the dryers are provided with a powerful and complex frame. When feeding, the grain material should be distributed along the dryer. Then it needs to be collected. In this case, the uniformity of the process should be ensured and inparallel sections. For this, paddle feeders and screw conveyors are provided in the design.
Recommended:
Fodder grain: quality and storage. How is feed grain different from regular grain?
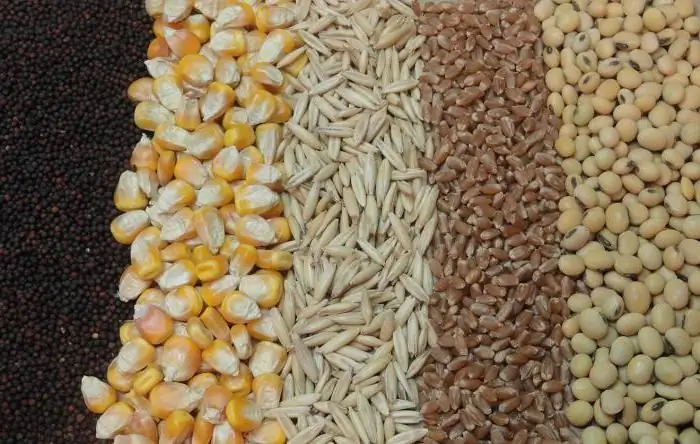
The development of animal husbandry makes it necessary to increase the amount of feed for livestock. According to statistics, about half of the total average annual grain harvest is spent for these needs. At the same time, 15-20 million tons of this mass falls on wheat. To reduce the cost of livestock products, instead of more expensive food cereals, feed grain is used
Thermal imaging control of electrical equipment: concept, principle of operation, types and classification of thermal imagers, features of application and verification
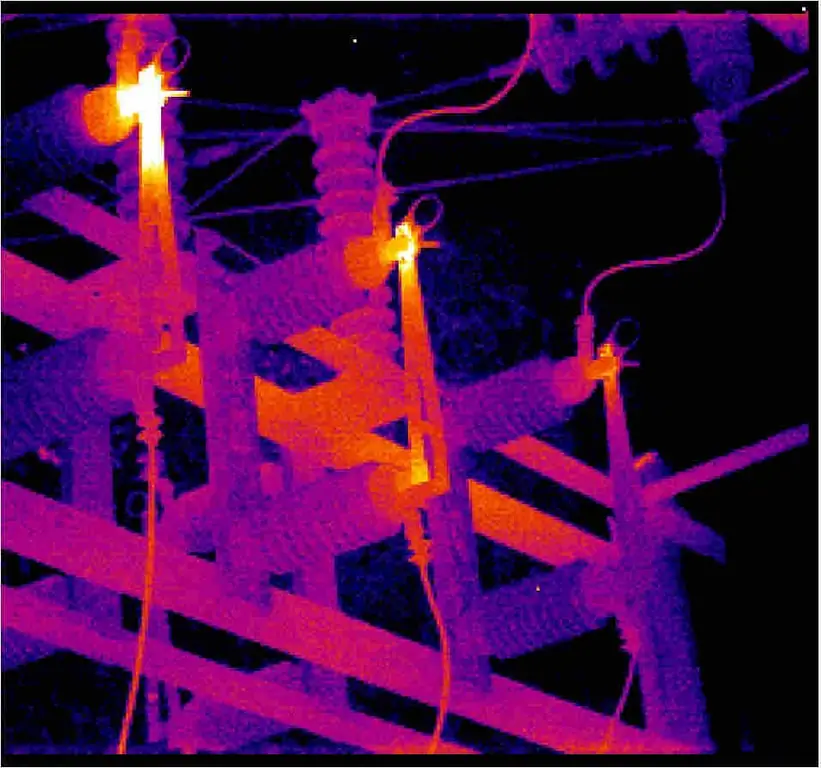
Thermal imaging control of electrical equipment is an effective way to identify defects in power equipment that are detected without shutting down the electrical installation. In places of poor contact, the temperature rises, which is the basis of the methodology
Continuous casting of steel: principle of operation, necessary equipment, advantages and disadvantages of the method
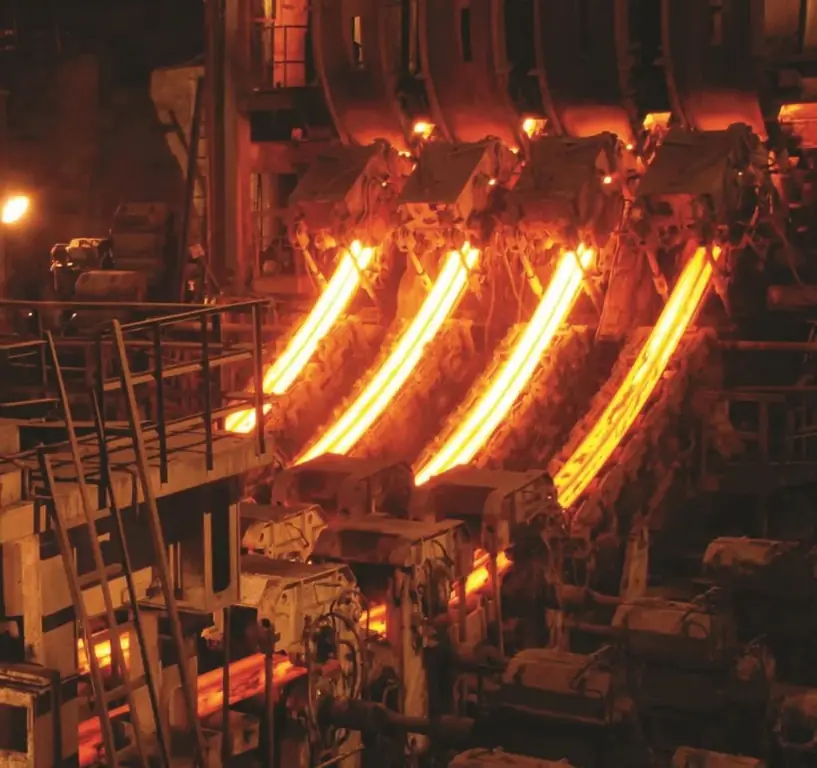
Today, a huge number of various things, parts, etc. are made of steel. Naturally, this requires a large amount of source material. Therefore, the plants have long been using the method of continuous casting of steel, characterized by the most important feature - high productivity
Cathodic corrosion protection of pipelines: equipment, principle of operation
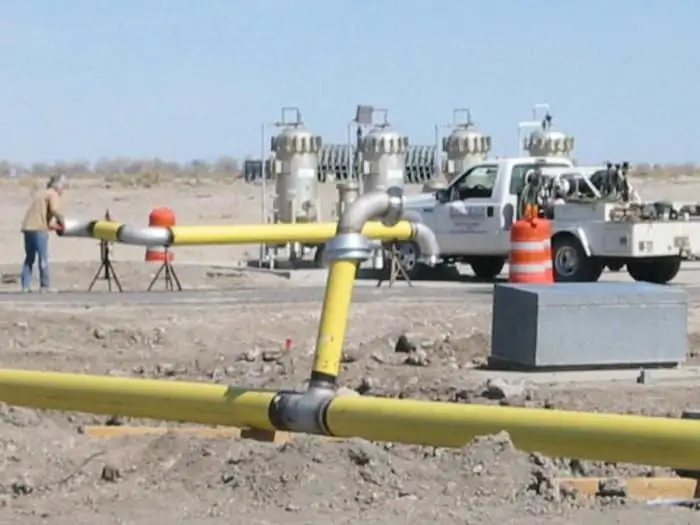
The article is devoted to the cathodic protection of pipelines from corrosion. The types of stations that implement such protection and the principle of operation of the technique are considered
HPP: principle of operation, scheme, equipment, power
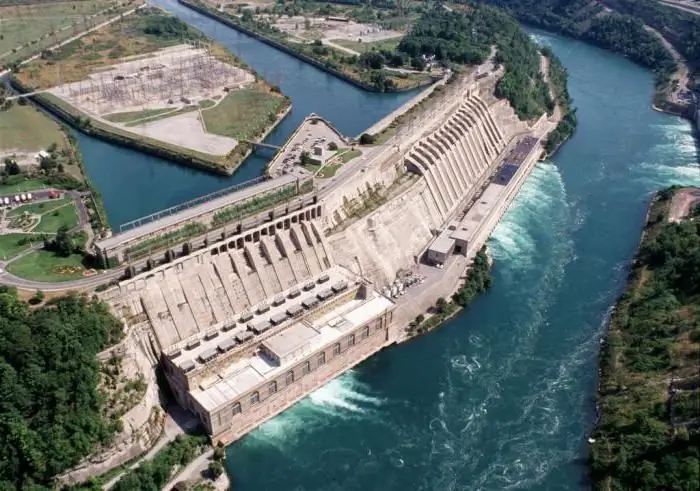
Almost everyone imagines the purpose of hydroelectric power plants, but only a few truly understand the principle of operation of hydroelectric power plants. The main mystery for people is how this whole huge dam generates electrical energy without any fuel. Let's talk about this