2025 Author: Howard Calhoun | [email protected]. Last modified: 2025-01-24 13:10
The casting mold is the most important element that is used to process the molten metal in order to obtain a casting that meets all requirements for size, roughness, structure, and product properties.
Shell Types
Currently, there are two fundamentally different types of forms. The difference between them is in the production technology of the mold. There are multi-layer types that are produced by applying a suspension, as well as using subsequent processes of coating and drying.
The second type is two-layer. The production of these forms is carried out by the electrophoretic method. The main requirements for the shell of the mold are hot, rigid, gas-permeable, precise, with a smooth contact surface, and also one-piece.

Multilayer shells
The process of obtaining a multilayer shell proceeds as follows: the surface of the mold is wetted with a suspension. This process is carried out by dipping the form in the required substance. After removing the block from the suspension, it is immediately sprinkled with a granular substance. The slurry sticks to the surface of the block, which allows you to recreate its configuration with great accuracy, and the granular material is necessary in order to fix the slurry on the surface of the mold, as well as to make its layer denser and thicker.
The freshly applied layer of slurry and granular material practically does not adhere to the mold surface. The only thing that keeps it from sliding is the wetting forces. Giving the necessary strength to this form is carried out in the subsequent drying process - chemical hardening. It turns out that for the manufacture of a multilayer casting mold, it is necessary to carry out three stages - moisten the shell with a suspension, sprinkle it with granular material, and then dry it. This procedure is carried out on average 4 to 6 times. However, if it is necessary to prepare a stronger casing, the quantity can be increased up to 12 times.
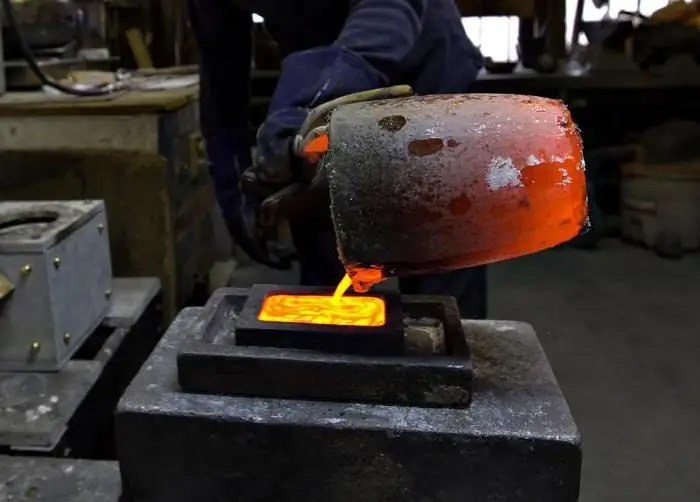
Double-layer casings
The production of two-layer molds is carried out with fewer procedures. The first stage of mold preparation is no different from the production of multilayer molds. The block is wetted and sprinkled with a granular product. However, before starting to apply the second layer, which is called phoretic, the first one must be moistened again with a suspension, which necessarily contains an electrolyte. For example, the composition may include hydrochloric acid, which is a conductor of the 2nd kind. In addition, the slurry must also contain a binder for the mold. And after wetting, sprinkle with granular material again.
After two layers have been applied to the block, the process of drying the mold begins. This is sufficient if it is necessary to obtain a mold whose wall thickness will not exceed 6-8 mm. If this figure needs to be increased, then two more layers are applied.
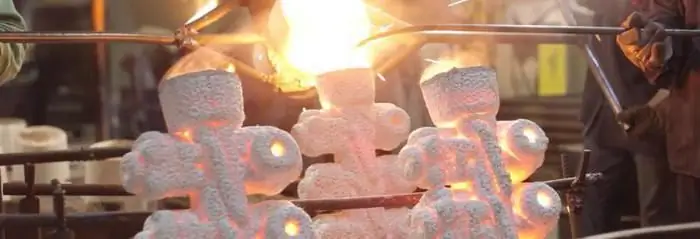
Varieties
For the metal casting process, a casting mold is needed, into which the molten substance is always poured. The main difference between these forms is one-time and multiple use. However, these two different types of forms are also divided into several classes.
There are disposable sand-based molds. For the manufacture of casting molds of this type, special siliceous sand is used, which is mixed in a special machine with water, as well as other binding elements. Molds from this category are used to produce parts of any configuration and size.
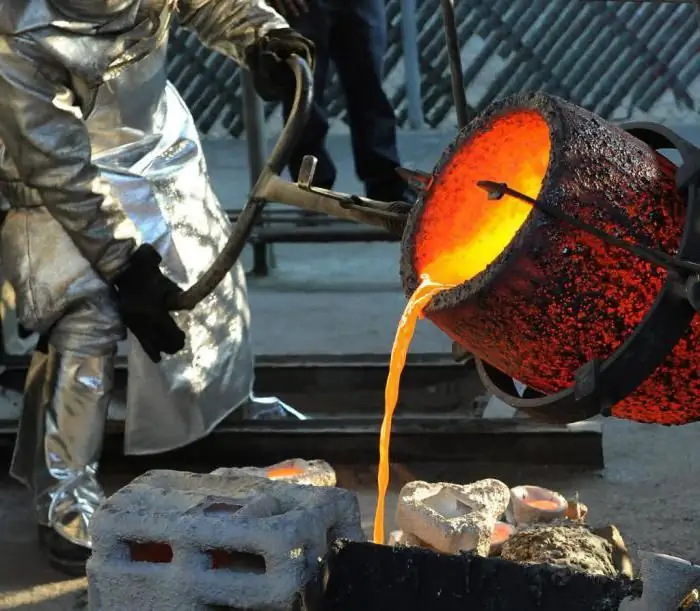
When casting non-ferrous metals, disposable shell molds are most often used. Gypsum shell molds (consisting of gypsum and a fast-hardening polymer) are used for the process of lining a casting model. After the plaster shell form dries, it is cut into two parts, which are dried again. After that, the form is connected and metal can be poured into it.
Fusible casting
In order to successfully implement the melt casting process, shell molds based on silicon dioxide are used. This substanceis a powder that is held together by various binding elements. The use of such molds occurs if it is necessary to produce a part with a high melting point.
Fusible metal casting mold is filled with various elements. It can be paraffin or subsequently frozen mercury, or plastic. After the production of the model, it is lined with some kind of refractory material. Vibration is used to compact the mold and the refractory layer. After the hardening process is completed, the shell is heated, due to which the block melts and flows out, while the mold remains and can be used to pour metal into it.
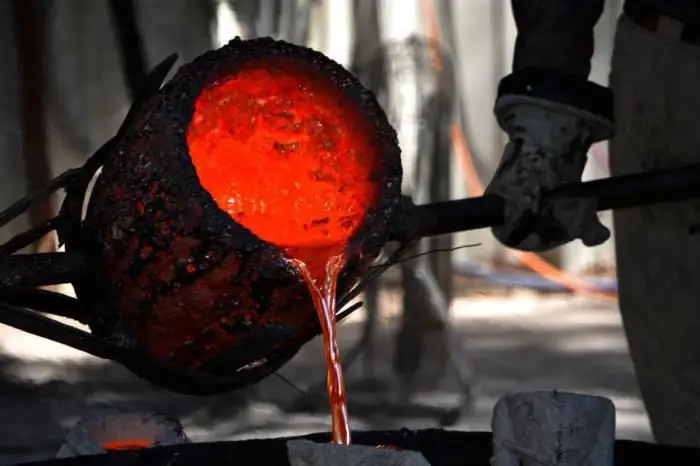
Reusable molds
Casting molds, which are reusable in terms of their use, are made from materials such as cast iron, copper, brass or heat-resistant steel. Reusable molds have found their application in non-ferrous metal casting. They are used for casting zinc, brass or aluminum alloys. In addition to them, molds made of graphite material are also actively used. Such blocks withstand up to several hundred castings. The process of manufacturing molds from graphite is carried out by mechanical action on the material. Most often, the design of this form consists of several parts that are fastened together. The only open part of this mold is the hole through which the melt is poured.
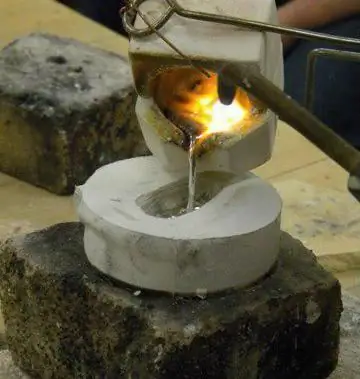
Molds
Speaking ofmultiple molds used for casting, molds can also be distinguished. These are open-type molds, in which the flow of molten metal is carried out by gravity. Most often, the manufacture of a casting mold is carried out from cast iron. However, you should be aware that when casting metal into molds, you must strictly follow certain rules and take into account some features.
- It is necessary to carefully monitor the cleanliness of the mold before each subsequent stage of pouring the metal.
- It is necessary to prevent splashing of metal on the walls of the mold when it is poured inside.
After each casting process, the mold is cleaned, and molding non-stick paints are always applied to the inner surface. The mold can hold up to 100 castings before becoming unusable.
Forming Materials
Materials used to make casting molds are called molding.
To form single-use molds, care must be taken to ensure that the material meets requirements such as strength, resistance to the dynamic effects exerted on the mold, and the ability to withstand the hydrostatic pressure exerted by the poured metal.
In order to make molds for reusable use, it is necessary to make higher demands on the material in terms of its strength. However, it is important to understand that with all the requirements that apply to these materials, they must have an acceptable price. Otherwisemanufactured parts in such forms will have a very high final cost. And the selling price will be even higher.
Recommended:
Casting in silicone mold: equipment. Vacuum casting in silicone molds
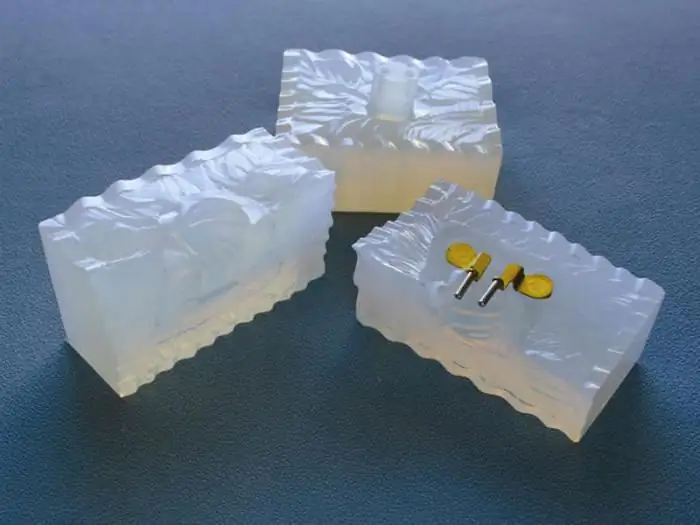
For the manufacture of a small number of plastic blanks, vacuum casting into silicone molds is most often used. This method is quite economical (making a metal mold requires more time and money). In addition, silicone molds are used repeatedly, and this also significantly reduces the cost of production
Iron casting technology
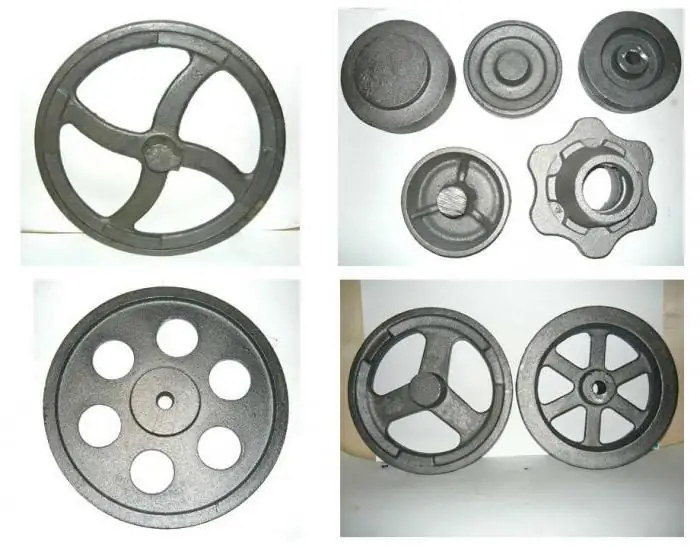
A brief review and description of the technology of casting iron products. Methods, methods and applications of cast iron parts
Shell mold casting: basic mold making operations
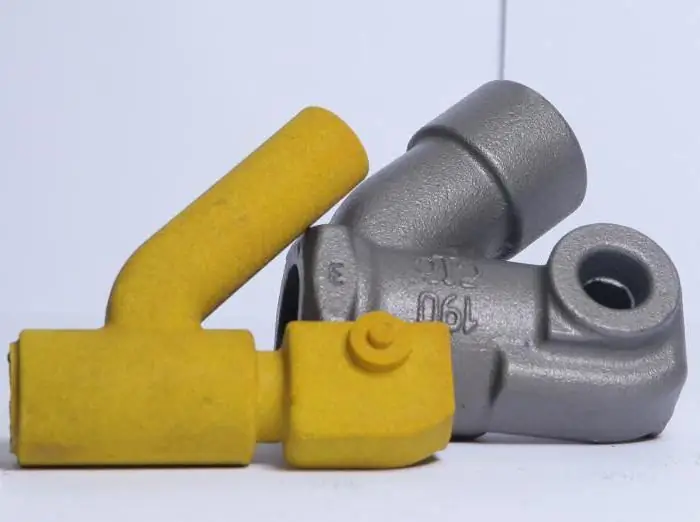
Currently, the industry is seriously developed and many different methods are used in casting. One such method is shell casting
Lost-wax casting: technology, advantages and disadvantages
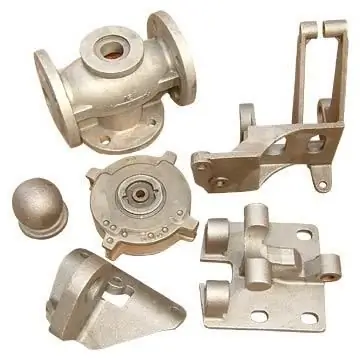
The use of investment models is a fairly popular method of foundry production. It is used where it is necessary to accurately observe the dimensions and ensure high quality of the surface of the parts. This is how turbine blades and high-performance tools, dentures and jewelry are cast, as well as sculptures of complex configuration. The mold for casting is one-piece, the model of low-melting materials is not removed during molding, but is melted out
Gating systems: types, device. Casting mold
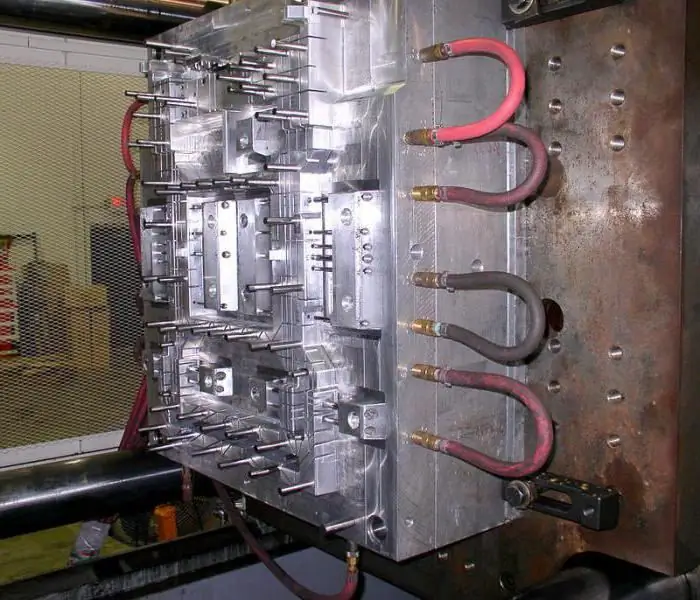
Gating systems: principle of operation, description, features, device, operation. Mold for casting: purpose, characteristics, photo