2025 Author: Howard Calhoun | [email protected]. Last modified: 2025-01-24 13:10
With the increasing complexity of metalworking technologies, new alloys for structures appear, and many areas in the metallurgical field cease to be relevant. However, materials that have stood the test of time and have remained indispensable due to their qualities are still actively used in various industries.
Iron casting is still one of the main directions in the work of most metallurgical companies. The reason lies in the fact that products made from this material are in high demand. Such products are distinguished by a long service life, as well as durability.
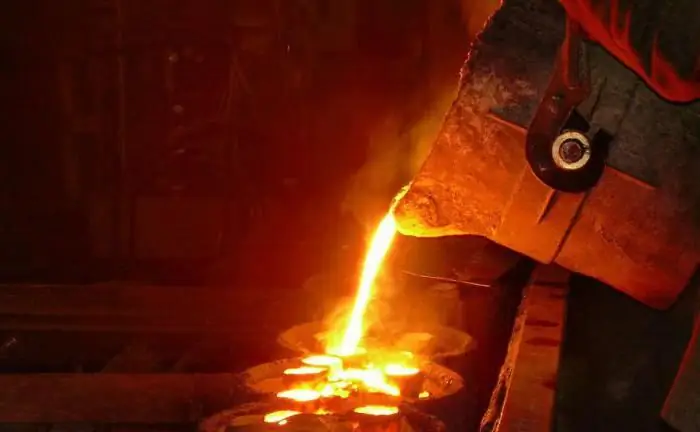
Iron casting technology
The production process has not changed much over time. Cast iron casting is the production of cast iron castings according to certain drawings, in which their parameters are set.
The execution process depends on the technology used in a particular enterprise. At the same time, in general, it assumes that the alloy in liquid form is fed into special forms. After the cast iron has cooled and solidified, it can be cut and removed from the mold, and then subjected to further operations. In the production of cast iron castings, it is assumed that further machining of products will be performed.
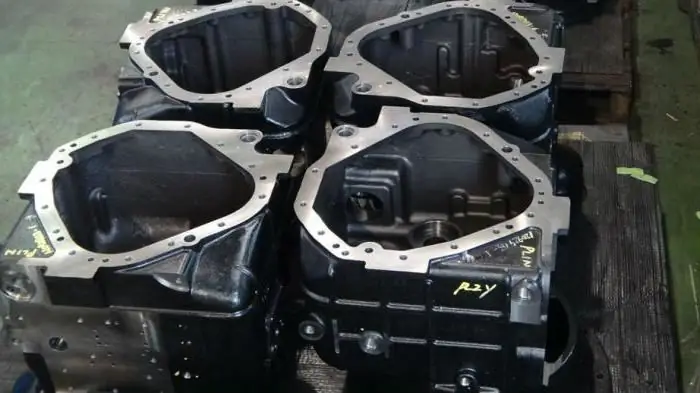
Companies that specialize in certain casting techniques produce a wide range of spare parts for various industries. The areas of use and performance of cast iron castings depend on the grade of this material.
Production
In the industrial sector, namely in the production of machines and machine tools, water disposal and water supply complexes, there is a high demand for parts that are made of cast iron, called "gray". The reason for this lies in the fact that such material is durable and wear-resistant. These properties are ensured by the fact that graphite is added to the alloy.
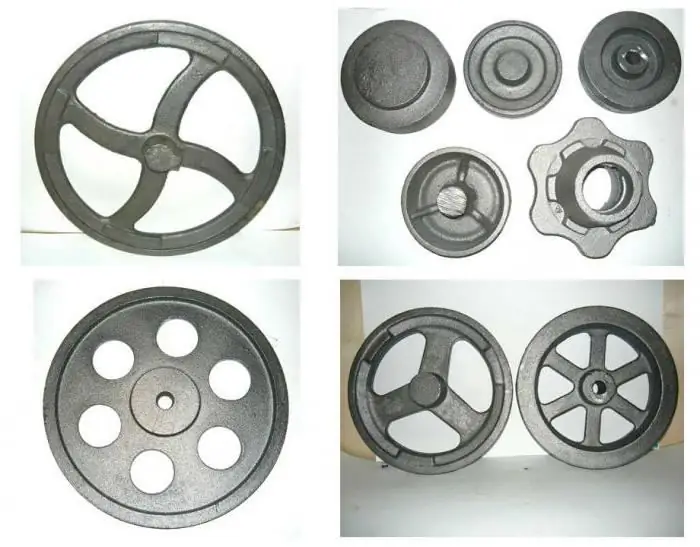
Different industrial companies apply for such a service as custom casting of cast iron products. Although there are differences in the requirements for the technological process, which are explained by the peculiarities of the activities of individual customers, there is a general requirement. It consists in the fact that the manufacture of cast iron must comply with the characteristics of the part, which are indicated in the drawings and documents.
Methods
Cast iron in cold-hardening mixtures is one of the modern technologies. This solution assumes that the molds are made from a mixture that includes binders such as resins. The advantage of a mold made from such a mixture is increased tightness. This eliminates the possibility that the integrity of the structure of the product will be violated during production.
Sand casting is also popularforms. This technology uses sand that has been compacted. This method is suitable for mass production of large parts, such as turbine blades or large parts of other mechanisms.
Currently, iron casting is undergoing active development. New production methods are successfully introduced into the technological field.
Recommended:
How to cook cast iron by electric welding: work technology and necessary materials
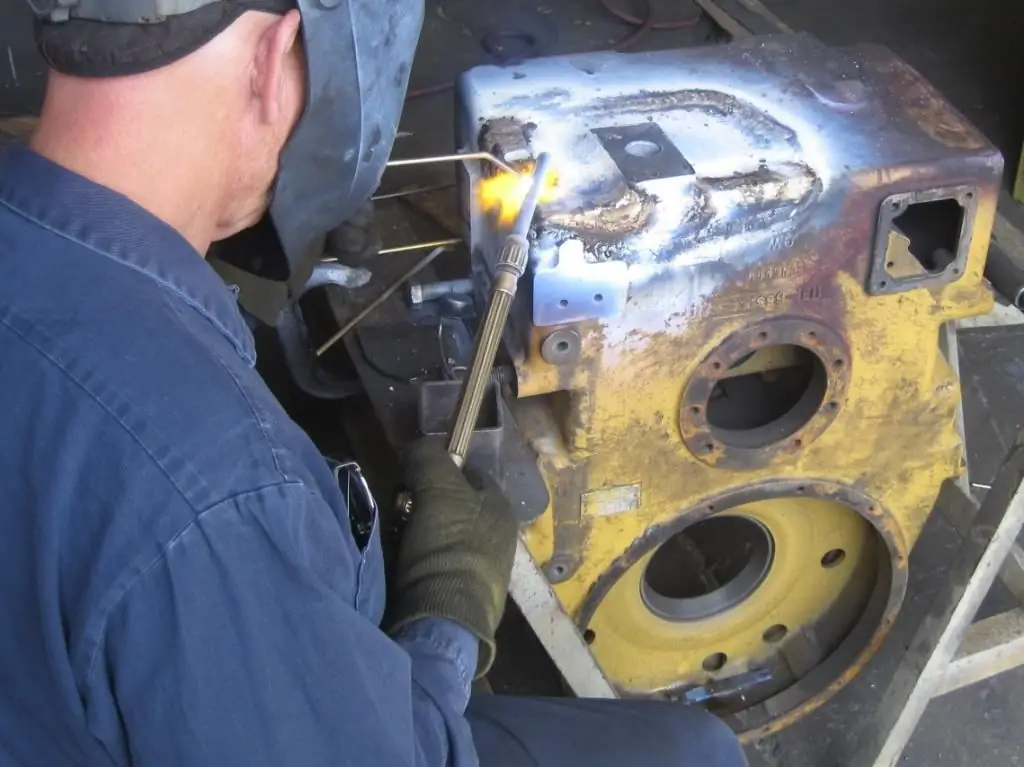
The main composition and types of cast iron. Difficulties and features of welding cast iron products. Cast iron welding methods. Preparatory operations before welding. How to cook cast iron by electric welding in a cold and hot way, as well as gas equipment. Features of the electrodes used for welding cast iron. Safety measures during welding
Resource-saving technology. Industrial technologies. The latest technology
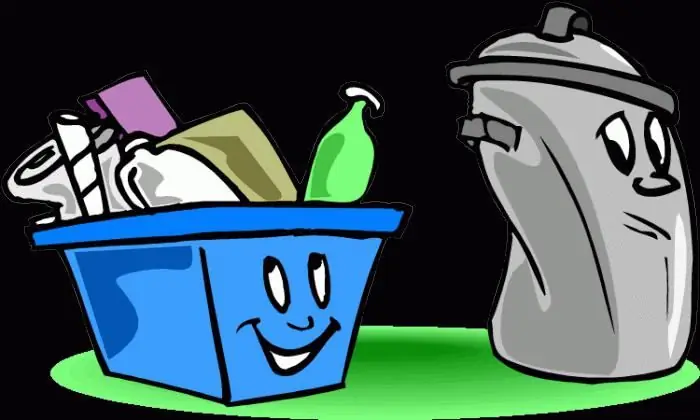
Modern industry is developing very dynamically. In contrast to past years, this development is proceeding intensively, with the involvement of the latest scientific developments. Resource-saving technology is of great importance. This term refers to a whole system of measures aimed at a significant reduction in resource consumption, while maintaining a high level of product quality. Ideally, they try to achieve the lowest possible level of consumption of raw materials
Casting in silicone mold: equipment. Vacuum casting in silicone molds
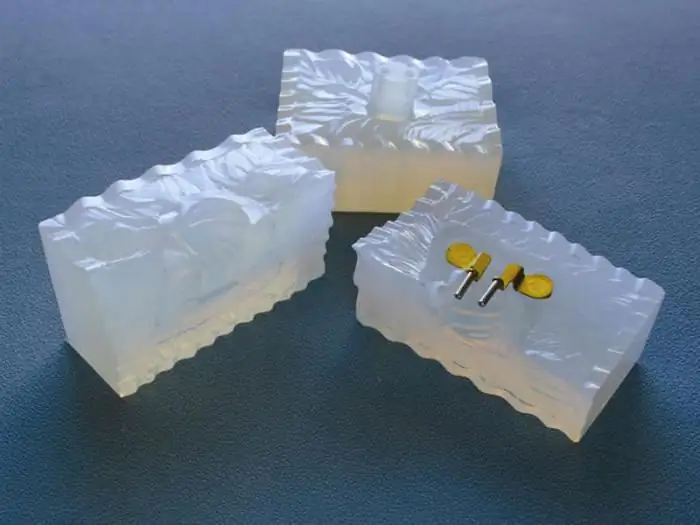
For the manufacture of a small number of plastic blanks, vacuum casting into silicone molds is most often used. This method is quite economical (making a metal mold requires more time and money). In addition, silicone molds are used repeatedly, and this also significantly reduces the cost of production
Casting mold: features, technology, types
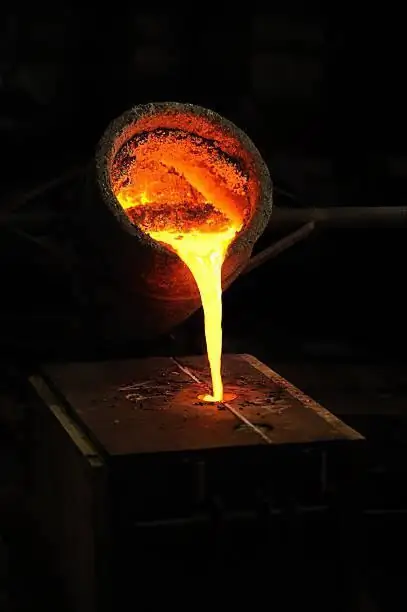
One of the most important processes in the industry is the process of casting various parts, raw materials and other things. However, in order to successfully produce the desired thing, it is necessary to make a mold for it, which largely determines the final result
Lost-wax casting: technology, advantages and disadvantages
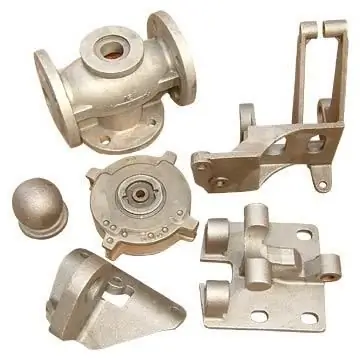
The use of investment models is a fairly popular method of foundry production. It is used where it is necessary to accurately observe the dimensions and ensure high quality of the surface of the parts. This is how turbine blades and high-performance tools, dentures and jewelry are cast, as well as sculptures of complex configuration. The mold for casting is one-piece, the model of low-melting materials is not removed during molding, but is melted out