2025 Author: Howard Calhoun | [email protected]. Last modified: 2025-06-01 07:12
Cast iron is a hard, corrosion-resistant, but brittle iron-carbon alloy with carbon content C ranging from 2.14 to 6.67%. Despite the presence of characteristic shortcomings, it has a variety of types, properties, applications. Ductile iron is widely used.
History
This material has been known since the 4th century BC. e. Its Chinese roots are in the VI century. BC e. In Europe, the first mention of the industrial production of the alloy dates back to the 14th, and in Russia - to the 16th century. But the technology for the production of ductile iron was patented in Russia in the 19th century. Later developed by A. D. Annosov.
Since gray cast irons are limited in use due to low mechanical properties, and steels are expensive and have low hardness and durability, the question arose of creating a reliable, durable, hard metal, at the same time having increased strength and a certain plasticity.
Forging cast iron is not possible, but due to its ductile characteristics, it lends itself to some types of pressure treatment (for example, stamping).
Production
The main way -smelting in blast furnaces.
Feedstock for BF:
- Batch - iron ore containing metal in the form of ferum oxides.
- Fuel - coke and natural gas.
- Oxygen - injected through special lances.
- Fluxes are chemical formations based on manganese and (or) silicon.
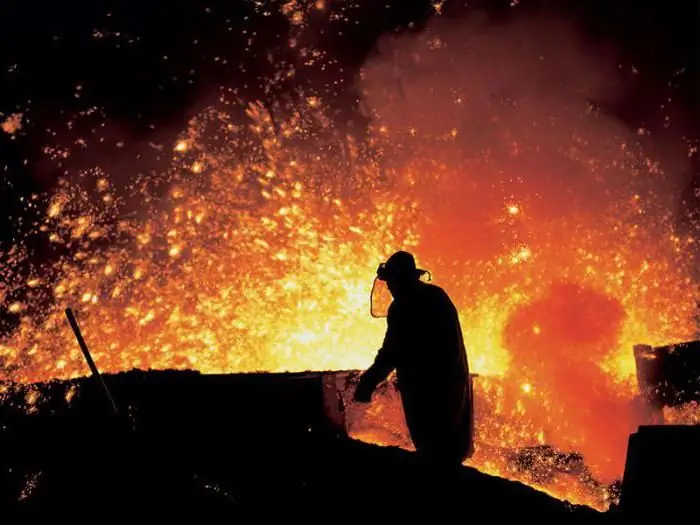
Stages of blast-furnace:
- Recovery of pure iron by chemical reactions of iron ore with oxygen supplied through lances.
- Combustion of coke and formation of carbon oxides.
- Carburization of pure iron in reactions with CO and CO2.
- Saturation of Fe3C with manganese and silicon, depending on the required output properties.
- Draining finished metal into molds through cast-iron tapholes; slag discharge through slag tapholes.
At the end of the working cycle, blast furnaces receive pig iron, slag and blast-furnace gases.
Blast Furnace Metal Products
Depending on the cooling rate, microstructure, saturation with carbon and additives, it is possible to obtain several types of cast iron:
- Purchased (white): bonded carbon, primary cementite. They are used as raw materials for the smelting of other iron-carbon alloys, processing. Up to 80% of all blast furnace alloy produced.
- Foundry (gray): carbon in the form of fully or partially free graphite, namely its plates. Used for the production of low-responsibility body parts. Up to 19% of produced blast-furnace castings.
- Special: rich in ferroalloys. 1-2% of the considered type of production.
Ductile iron is obtained by heat treatment of the pig iron.
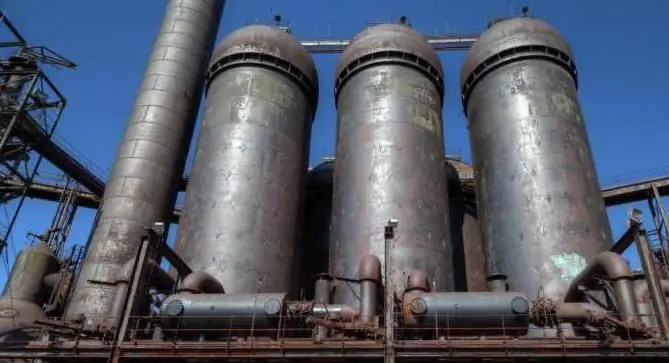
Theory of iron-carbon structures
Carbon with ferum can form several different types of alloys according to the type of crystal lattice, which is displayed on the microstructure option.
- Solid solution penetration into α-iron - ferrite.
- Solid solution penetration into γ-iron - austenite.
- Chemical formation Fe3C (bound state) - cementite. Primary is formed by rapid cooling from a liquid melt. Secondary - slower temperature decrease, from austenite. Tertiary - gradual cooling, from ferrite.
- Mechanical mixture of grains of ferrite and cementite - perlite.
- Mechanical mixture of grains of perlite or austenite and cementite - ledeburite.
Cast irons have a special microstructure. Graphite can be in a bound form and form the above structures, or it can be in a free state in the form of various inclusions. The properties are affected by both the main grains and these formations. Graphite fractions in metal are plates, flakes or balls.
The lamellar shape is characteristic of gray iron-carbon alloys. It makes them fragile and unreliable.
Flake-like inclusions have malleable cast irons, which have a positive effect on their mechanical performance.
The spherical structure of graphite is even moreimproves the quality of the metal, affecting the increase in hardness, reliability, exposure to significant loads. High-strength cast iron has these characteristics. Malleable cast iron determines its properties by ferritic or pearlitic bases with the presence of flaky graphite inclusions.
Production of ferritic ductile iron
It is produced from a white pig hypoeutectoid low-carbon alloy by annealing ingots with a carbon content of 2.4-2.8% and the presence of additives corresponding to them (Mn, Si, S, P). The thickness of the walls of the annealed parts should be no more than 5 cm. For castings of significant thickness, graphite has the form of plates and the desired properties are not achieved.
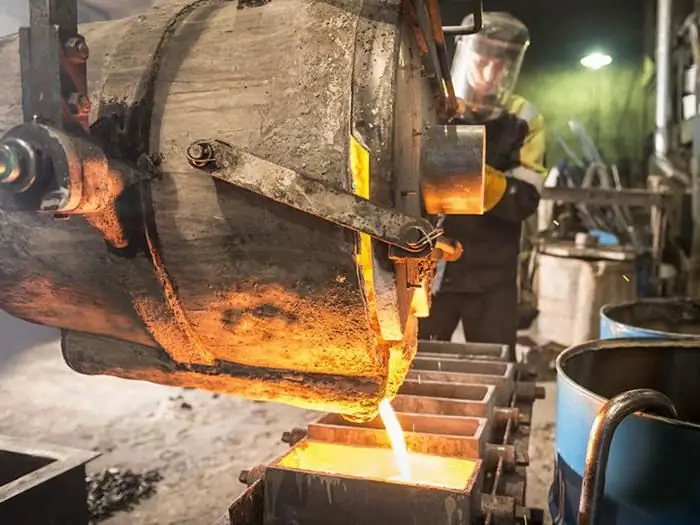
To get ductile iron with a ferritic base, the metal is placed in special boxes and sprinkled with sand. Tightly closed containers are placed in heating furnaces. Carry out the following sequence of actions during annealing:
- The structures are heated in ovens to a temperature of 1,000 ˚С and left to be kept at constant heat for a period of 10 to 24 hours. As a result, primary cementite and ledeburite disintegrate.
- The metal is cooled to 720 ˚С together with the furnace.
- At a temperature of 720 ˚С they are kept for a long time: from 15 to 30 hours. This temperature ensures the decomposition of secondary cementite.
- At the final stage, they are cooled again together with the working stove to 500 ˚С, and then removed to the air.
Such technological annealing is called graphitizing.
After the work done, the microstructure of the material isferrite with flaky graphite grains. This type is called "black-hearted" because the break is black.
Production of pearlitic ductile iron
This is a kind of iron-carbon alloy, which also originates from hypoeutectoid white, but the carbon content in it is increased: 3-3.6%. To obtain castings with a pearlite base, they are placed in boxes and sprinkled with crushed powdered iron ore or scale. The annealing procedure itself is simplified.
- The temperature of the metal is increased to 1,000 ˚C, held for 60-100 hours.
- Designs cool with oven.
Due to languor under the influence of heat, diffusion occurs in the metal environment: the graphite released in the cementite decay partially leaves the surface layer of the annealed parts, settling on the surface of the ore or scale. A softer, more ductile and ductile upper layer of "white-hearted" ductile iron with a hard center is obtained.
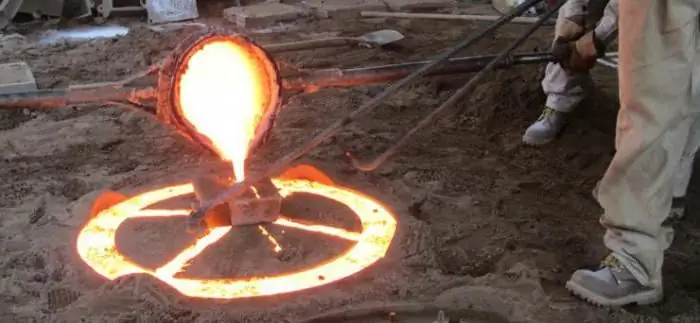
Such annealing is called incomplete. It ensures the disintegration of cementite and ledeburite into lamellar perlite with the corresponding graphite. If granular pearlitic ductile iron with higher impact strength and ductility is required, additional heating of the material up to 720 ˚С is applied. This results in the formation of pearlite grains with flaky graphite inclusions.
Properties, Markings and Applications of Ferritic Ductile Iron
Long "languishing" of the metal in the furnace results in the complete decay of cementite and ledeburite into ferrite. Thanks totechnological tricks, an alloy with a high carbon content is obtained - a ferritic structure characteristic of low-carbon steel. However, carbon itself does not disappear anywhere - it passes from a state bound to iron to a free state. Temperature effect changes the shape of graphite inclusions to flaky.
Ferritic structure causes a decrease in hardness, an increase in strength values, the presence of such characteristics as impact strength and ductility.
Marking of ductile irons of ferritic class: KCh30-6, KCh33-8, KCh35-10, KCh37-12, where:
KCh - variety designation - malleable;
30, 33, 35, 37: σv, 300, 330, 350, 370 N/mm2 - maximum load that it can withstand without collapsing;
6, 8, 10, 12 - relative elongation, δ, % - plasticity index (the higher the value, the more the metal can be processed by pressure).
Hardness - about 100-160 HB.
This material, in terms of its performance, occupies a middle position between such as steel and gray iron-carbon alloy. Ductile cast iron with a ferritic base is inferior to pearlitic in terms of wear resistance, corrosion and fatigue strength, but higher in terms of mechanical endurance, ductility, and casting characteristics. Due to its low price, it is widely used in industry for the manufacture of parts operating under low and medium loads: gears, crankcases, rear axles, plumbing.
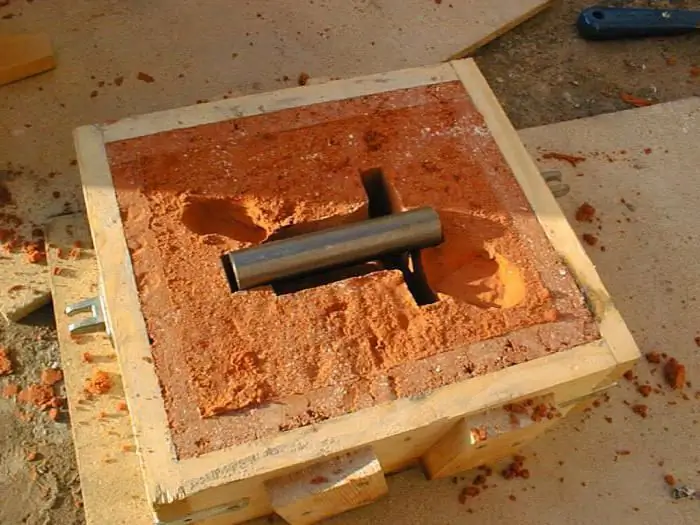
Properties, Markings and Applications of Pearlitic Ductile Iron
Due to incomplete annealing, primary, secondary cementites and ledeburite have time to completely dissolve in austenite, which at a temperature of 720 ˚С turns into pearlite. The latter is a mechanical mixture of grains of ferrite and tertiary cementite. Actually, part of the carbon remains in a bound form, determines the structure, and part is “released” into flaky graphite. In this case, perlite can be lamellar or granular. Thus pearlitic ductile iron is formed. Its properties are due to its saturated, harder and less pliable structure.
These, in comparison with ferritic, have higher anti-corrosion, wear-resistant properties, their strength is much higher, but lower casting characteristics and ductility. The pliability to mechanical stress is increased superficially, while maintaining the hardness and viscosity of the core of the product.
Marking of malleable cast iron pearlitic class: KCh45-7, KCh50-5, KCh56-4, KCh60-3, KCh65-3, KCh70-2, KCh80-1, 5.
The first digit is the strength designation: 450, 500, 560, 600, 650, 700 and 800 N/mm2 respectively.
Second - the designation of plasticity: elongation δ,% - 7, 5, 4, 3, 3, 2 and 1, 5.
Perlitic malleable cast iron has been used in mechanical engineering and instrumentation for structures operating under heavy loads - both static and dynamic: camshafts, crankshafts, clutch parts, pistons, connecting rods.
Heat treatment
The material obtained as a result of heat treatment, namely annealing, can be rebe subjected to temperature influences. Their main goal is to further increase strength, wear resistance, resistance to corrosion and aging.
- Hardening is used for structures requiring high hardness and toughness; produced by heating up to 900 ˚С, the parts are cooled at an average rate of about 100 ˚С/sec using engine oil. It is followed by high tempering with heating up to 650˚С and air cooling.
- Normalization is used for medium-sized simple parts by heating in an oven to 900 ˚С, holding at this temperature for a period of 1 to 1.5 hours and then cooling in air. Provides troostite granular perlite, its hardness and reliability in friction and wear. It is used to obtain anti-friction malleable cast irons with a pearlitic base.
- Annealing is repeated in the manufacture of anti-friction: heating - up to 900 ˚С, long-term holding at this heat, cooling together with the furnace. The ferritic or ferritic-pearlitic structure of anti-friction ductile iron is provided.
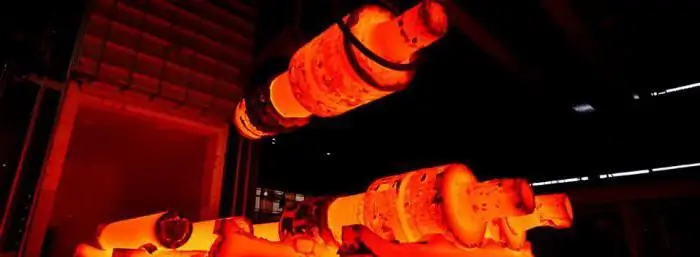
Heating of cast iron products can be carried out locally or in combination. For local use, high-frequency currents or an acetylene flame (hardening). For complex - heating furnaces. With local heating, only the upper layer is hardened, while its hardness and strength increase, but the ductility and viscosity of the core remain.
It is important to point out here that forging cast iron is impossible not only due to insufficient mechanicalcharacteristics, but also because of its high sensitivity to a sharp temperature drop, which is inevitable when hardening with water cooling.
Anti-friction ductile irons
This variety applies to both malleable and alloyed ones, they are gray (ASF), malleable (ASC) and high-strength (ACS). Ductile iron is used for the production of ACHK, which is annealed or normalized. The processes are carried out in order to increase its mechanical properties and form a new characteristic - wear resistance during friction with other parts.
Marked: AChK-1, AChK-2. It is used for the production of crankshafts, gears, bearings.
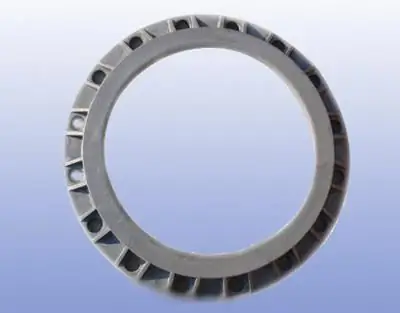
Influence of additives on properties
In addition to the iron-carbon base and graphite, they also contain other components that also determine the properties of cast iron: manganese, silicon, phosphorus, sulfur, and some alloying elements.
Mangan increases liquid metal fluidity, corrosion resistance and wear resistance. It helps to increase hardness and strength, bond carbon with iron in the chemical formula Fe3C, the formation of granular perlite.
Silicon also has a positive effect on the fluidity of the liquid alloy, promotes the decomposition of cementite and the release of graphite inclusions.
Sulfur is a negative but inevitable component. It reduces mechanical and chemical properties, stimulates the formation of cracks. However, the rational ratio of its content with other elements (for example, with manganese) allowscorrect microstructural processes. So, at the Mn-S ratio of 0.8-1.2, perlite is preserved at any time of temperature influences. When the ratio is increased to 3, it becomes possible to obtain any necessary structure, depending on the specified parameters.
Phosphorus changes fluidity for the better, affects strength, reduces impact strength and ductility, affects the duration of graphitization.
Chromium and molybdenum hinder the formation of graphite flakes, in some contents they contribute to the formation of granular perlite.
Tungsten improves wear resistance in high temperature areas.
Aluminum, nickel, copper contribute to graphitization.
By adjusting the amount of chemical elements that make up the iron-carbon alloy, as well as their ratio, it is possible to influence the final properties of cast iron.
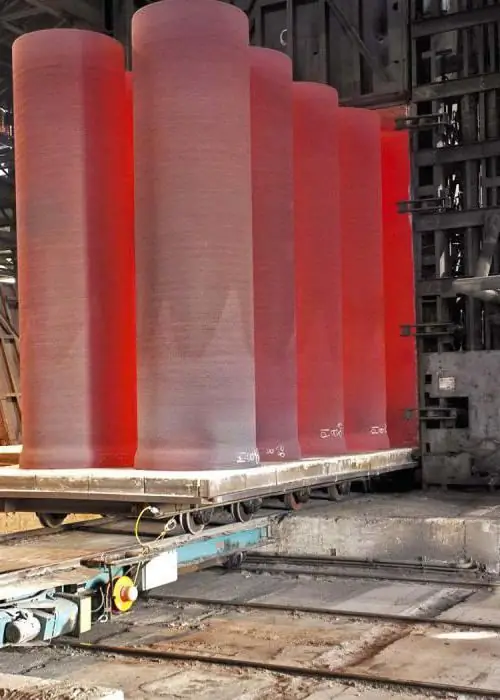
Advantages and disadvantages
Ductile iron is a material that is widely used in engineering. Its main advantages:
- high hardness, wear resistance, strength along with fluidity;
- normal toughness and ductility characteristics;
- manufacturability in forming, unlike gray cast irons;
- various options for correcting properties for a specific part by methods of thermal and chemical-thermal treatment;
- low cost.
Disadvantages include individual characteristics:
- fragility;
- presence of graphite inclusions;
- poor cutting performance;
- considerable weight of castings.
Despite the existing shortcomings, ductile iron occupies a responsible place in metallurgy and engineering. Such important parts as crankshafts, brake pad parts, gear wheels, pistons, connecting rods are made from it. Having an insignificant variety of grades, ductile iron occupies an individual niche in the industry. Its use is typical for those loads in which the use of other materials is unlikely.
Recommended:
Alloy cast iron: grades, properties and applications
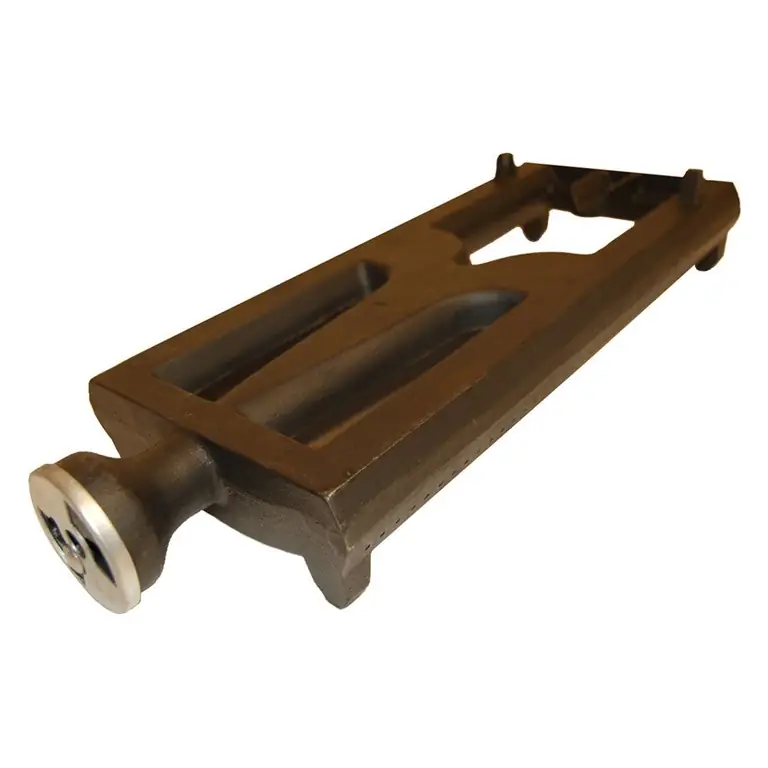
Alloyed iron is a material that is produced by smelting in blast furnaces. It can contain different amounts of carbon. Depending on the quantitative content of this substance, two types of cast iron are distinguished. The first is called conversion, or white, and the second is gray, or foundry
Types of cast iron, classification, composition, properties, marking and application
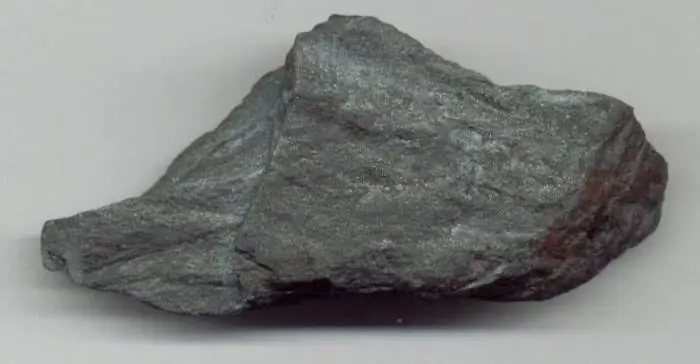
The types of cast iron that exist today allow a person to create many products. Therefore, we will talk about this material in more detail in this article
Marking of bronze: characteristics, properties and scope
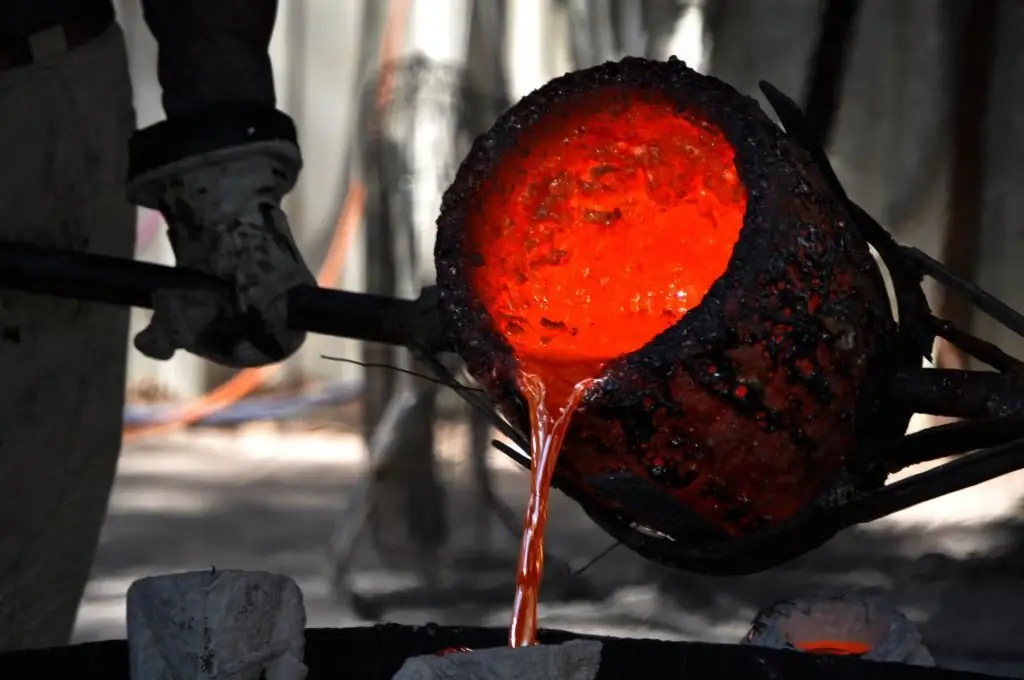
Due to its decorative features and many other properties, bronze has become popular. It is very difficult even for connoisseurs to name all the impurities and additives that are present in bronze alloys. This article will focus on bronze and its marking
Rock s alt halite: properties, description and scope
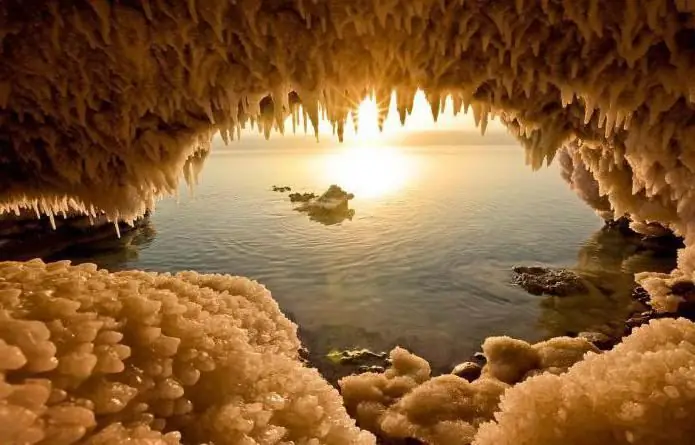
S alt halite is a natural mineral from which the well-known table s alt is obtained. The technical mineral has a number of properties, the application of which was found in 14,000 areas. The most common of them is the treatment of road surfaces in the fight against ice
White cast iron: properties, application, structure and features
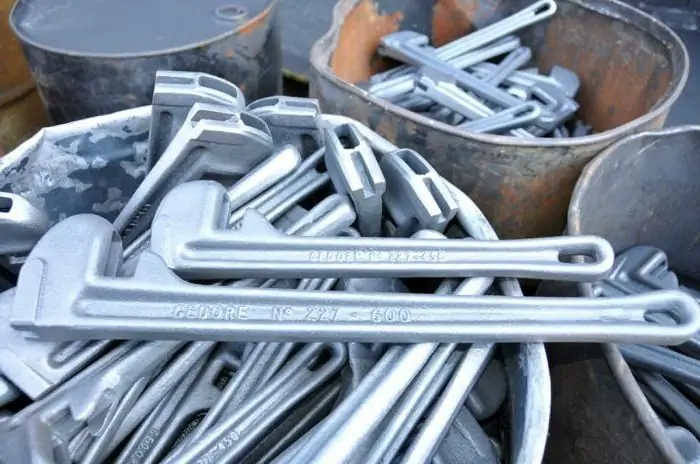
Initially, the technology of casting iron was first mastered in China in the 10th century, after which it became widespread in other countries of the world. A prominent representative of such an alloy is white cast iron, which is used in mechanical engineering for the manufacture of parts, in industry and in everyday life